With the thought of what labor rationing is, many of us have associations of production, an uninterrupted workflow. This term is of great importance in planning the economy. And although today you can often hear the opinion that the rationing of workers is an echo of the Soviet production system, most industrial enterprises are in no hurry to refuse to use this tool.
Why establish labor standards
It is impossible to imagine a modern management process without production costs, especially if there is such a component as payment for the work of employees. But what is labor rationing, what is meant by this concept? First of all, this is a mechanism for determining the costs of working time for the implementation of a particular type of work in the production environment. Labor rate is a unit of measure that allows you to plan, analyze the total labor costs in the organizational and technical conditions.
An acute need for labor regulation arises during a crisis. The desire of entrepreneurs to reduce costs leads to the development of new, more effective economic instruments. Rationing labor costs is one of them. All companies, production associations of the sector of heavy and light industry, construction, transport, communications, wish not only to maintain their place in the niche of the domestic market, but also to achieve higher results, which is impossible without the use of innovative approaches and increased competitiveness.
Management of labor standards is an important element of production management, which is used by both domestic and foreign entrepreneurs. The experience gained in this segment applies not only to the production of material products, but also to the service sector. Economists find it appropriate to work on labor standards in budgetary institutions if the number of employees exceeds 50 people. In simple words, adhering to rational and effective labor standards is necessary in any professional industry. Neglecting them in a volatile market economy is quite risky.
What is the difference between a norm and a norm?
Often in a non-professional environment these two terms are mixed. They are considered synonyms that have exactly the same meaning, but in fact, despite the apparent proximity, these concepts have a different definition. The standard is a scientifically sound, centrally developed indicator of labor costs. Moreover, it can be introduced at the enterprise or serve as a kind of model for the organization to independently develop its own indicators of the norm. The use of standards can be repeated over a long period, and the norm is set only for one specific task and is replaced by another at the slightest organizational and technical adjustment.
The concept of rationing
Standards and norms are used everywhere, at any level, at any stage of the production process. What is labor rationing? This is a kind of way of rational distribution of labor resources and time costs. Norms are used in the process of primary and secondary production. There is a certain sense in setting labor standards for conveyor, manual (mixed), piece or large-scale, mass production. Moreover, recommendations are being developed on the standardization of labor of employees of the enterprise staff and management.
Setting standards and measures of labor should be considered in a wide and narrow sense. First of all, it is an ordered complex of special tools and methods that are intended for the effective determination of labor measures. Its purpose is to obtain an objective assessment of the existing efficiency of the production process and the compliance of the applied labor costs with the size of material remuneration.
In a broader sense, it is possible to determine what labor rationing is: this is an area of ββeconomic, engineering, and social activity. To implement the standards of the labor process, they use such tools as regulatory materials and the results of economic and theoretical research using computer programs to calculate the minimum, maximum and average values.
Classification of labor standards
This measure can be expressed by various indicators - the volume, time, number of executive and serviced objects. In the applicable labor regulation systems, great importance is given to the development of standards for the implementation of one product unit by one or a group of performers. As an example, take a team of assemblers, which collects one vacuum circuit breaker in 2 hours. In parallel with the time indicator, the inverse of labor rationing is taken into account - the rate of production. In fact, this standard involves establishing the amount of work, a kind of plan that workers need to complete in one shift. Since a team of assemblers collects one switch in an average of two hours, they are faced with the task of collecting at least four of the same switches per shift.
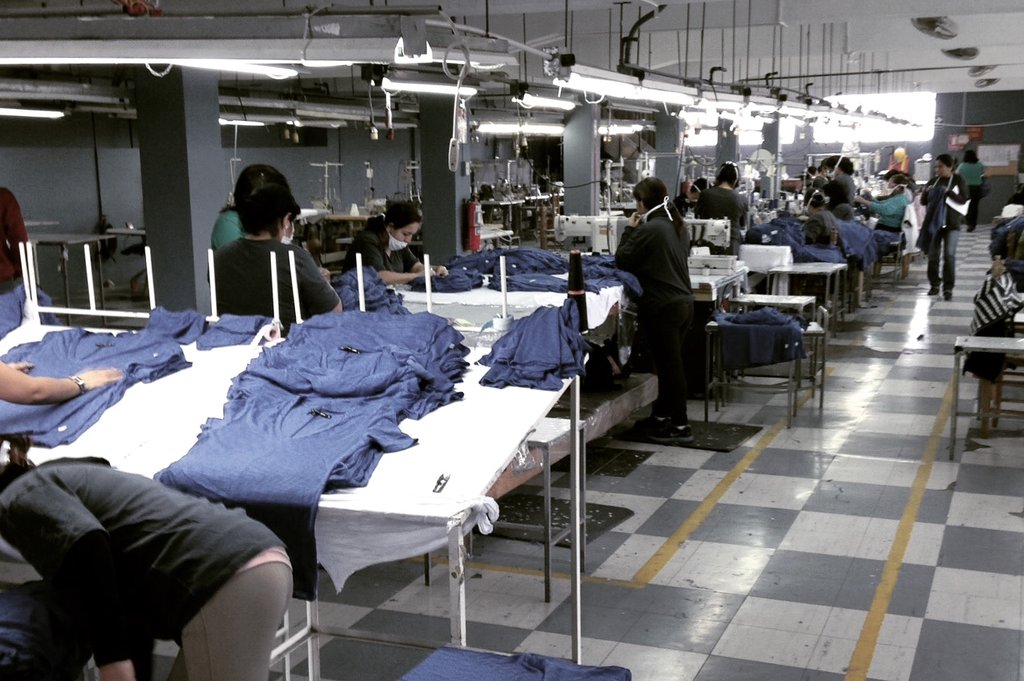
Another standard in labor standards is service metrics. It is set for performers and determines how many facilities they need to serve for a specific period of time. For example, an equipment installer needs to repair seven machines per shift. The inverse measure of the number allows you to calculate how many workers you need to engage to perform a given amount of work or maintenance of a production facility per unit time.
Labor rationing in budgetary organizations presupposes the existence of such a standard as a controllability measure reflecting the number of employees who may be under the direction of the director. The second name for this indicator is the norm of the number of subordinates. For example, a site master manages a workflow in which no more than 35 people can participate.
Under the norm of service time, it is assumed a measure that approves the rational expenditure of time on work with one object. We can talk not only about servicing industrial equipment, but also about other sectors of the service sector. For example, a specialist is given no more than 15 minutes to serve one visitor to a multifunctional center.
Calculation Methods
Rationing of labor of workers is a separate scientific field of the economy, which has its own tools and methodology. Conventionally, all methods for calculating the norms for fulfilling work tasks can be divided into analytical and total.
The second group includes techniques that do not require the separation of production operations into several stages. The total methods do not imply an analysis of the labor process, an assessment of the rationality of the resources used and labor. Such techniques allow us to determine normalized indicators using statistical and operational information. Moreover, in this sense, the competence of the normalizer is of great importance, so the so-called human factor plays an important role here.
Analytical calculation methods are more often used to standardize labor in budgetary institutions. They suggest carrying out a deep analysis of the labor process, its differentiation into several stages of work performance by performers. In this case, the specifics of job standards and instructions for performing professional duties are always taken into account. The category of analytical methods for calculating labor standards includes research, calculation and mathematical-statistical tools.
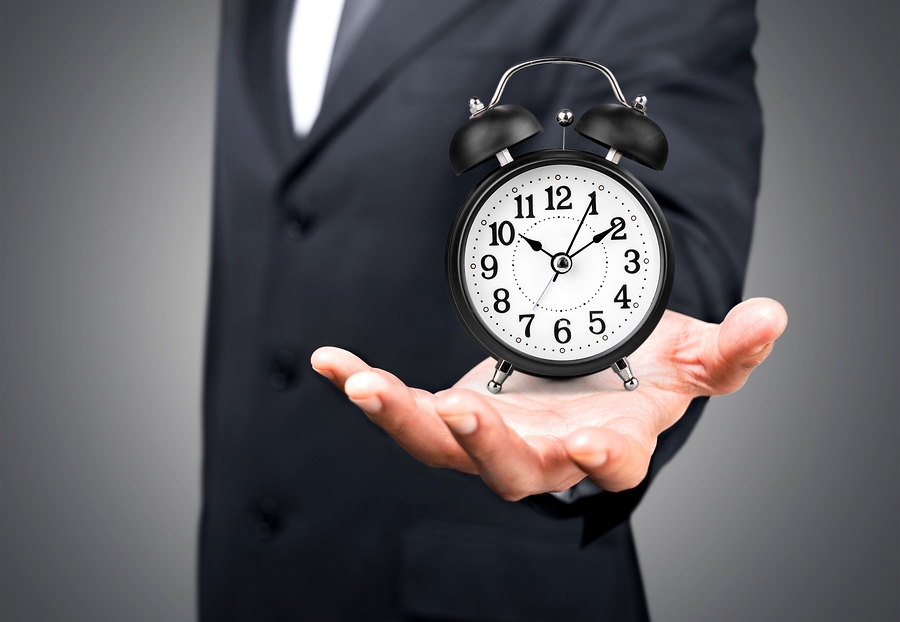
The research method involves the analysis based on the information collected during the creation of time-lapse production technologies and planning of working hours. Timing in the labor standardization system is such a technique in which measures are determined for repeated repetition of the same operational and technical elements in machine or manual type of production. The task of timing is to establish the main and auxiliary time for the execution of certain operations for the implementation of the labor process. Timing is used as a direct tool for rationing in production and verifying the effectiveness of the applicable standards by a calculated or elective method.
Additionally, the method of moment observations can be used, which allows you to evaluate labor costs without measuring indicators directly related to them. The basis of this tool is probability theory. There is no need for continuous time recording, since the method allows you to cover several objects and their activities at once.
Main tasks
The main goal when setting labor standards at a manufacturing or non-manufacturing enterprise, a budgetary institution is to provide satisfactory conditions for maximum labor potential efficiency, increase product competitiveness indicators and occupy higher positions in the domestic or foreign market by reducing labor costs and introducing innovative technologies into the workflow.
The primary task of labor standards is to solve a number of problems:
- ensuring rational planning of labor costs and distribution of resources ready for use;
- establishing the optimal ratio between the amount of equipment available and the number of employees who service it and perform production tasks;
- development of rules and regulations of labor activity within a specific enterprise.
The system of labor standards used in production is commonly understood as a set of strategic methods for organizing, coordinating and managing the work process. This complex also includes other important elements of rationing in production:
- the choice of a methodological approach to establishing standards for various lines of activity and categories of employees;
- an algorithm for assessing standards according to quality criteria, as well as the use of an effective procedure for their replacement;
- maintaining relevant supporting documentation reflecting the tasks of labor standards.
All of the above conditions are necessary for the efficient rationalization of the resources used and the reduction of production costs. That is why managers are interested in improving the applicable labor standards for reasonable, progressive indicators, taking into account the characteristics of jobs and the intensity of work.
Organizational and planned functions of labor standards
Each enterprise has its own regulations on labor standards. How effective the applied system is is evidenced by economic indicators, including sales growth, increased demand for products or services, and increased competitiveness. Ideally, labor standards should cover the vast majority of production processes and categories of performers. It also matters how quickly and timely new standardized indicators are developed, reviewed and implemented.
The provision on the system of regulation of labor in production pursues the fulfillment of two main functions - planned and organizational. The first is expressed by a set of necessary conditions, without which harmonious development and effective interaction of all divisions, departments, branches of the enterprise is impossible, taking into account consumer demand and supply on the market. The regulation on labor standards applied in a production company is the basic basis of planning processes for the main indicators of its core business. Forecasts are used in all sectors of the economy to determine a long-term work plan. The importance of effective planning today is hard to overestimate. It is no coincidence that it is one of the requirements of the modern economy, because the introduction of the most advanced systems for evaluating indicators contributes to a stable increase in labor productivity and a more rational consumption of resources.
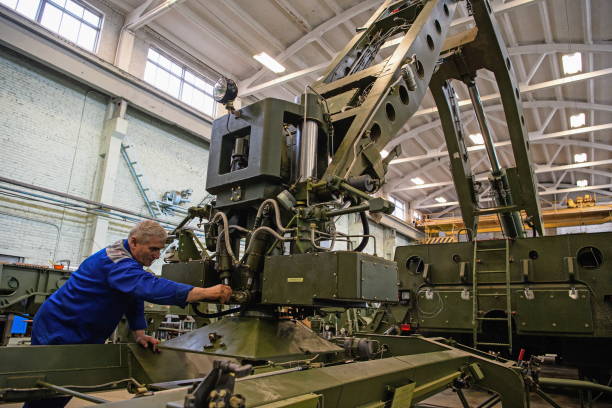
Rationing also performs an organizational function that allows you to establish progressive relationships between the separate components of the production chain, find effective use of the unclaimed material and intangible resources of the enterprise. Thanks to labor standards, it is possible to form a common production system, consisting of capital, equipment and labor, and to support its working capacity and productivity in the future. Basically, the regulation of labor, and more precisely, its organizational function, is the main guideline in the placement of personnel, the implementation of processes to optimize the structure of the enterprise and the number of personnel.
Economic and socio-legal feasibility of rationing
In work on the regulation of labor, great attention must be paid to the influence of natural economic processes and laws in force in our time. If you ignore a number of features that are inextricably linked with the model of modern market relations, it is impossible to plan and calculate the exact amount of labor costs, to find out the degree of demand for the finished product and its equivalent barter exchange.
The economic purpose of labor standards is to non-stop stimulation of productivity, increasing productivity with maximum time savings - these are determining criteria for evaluating the effectiveness of the technologies used at the enterprise and progressive models for organizing the production process. Many recommendations on labor standards imply the preference for an economical option for resource consumption in order to minimize overall costs.
In addition, modern labor standards are designed to provide a more stringent impact of the market mechanism on the increase in the efficiency of performance indicators and the improvement of quality characteristics. Given that labor regulation is the most convenient tool for measuring labor costs with finished products of activity, it is important for each business entity to ensure a stable and high level of profit.
The economic function of production is also influenced by the managerial function of the standardization system. Without well-coordinated management work at the enterprise, it is difficult to achieve a consistent return on all elements of the production chain. If we study the mechanism of labor costs at a particular workplace, then we can no doubt say that rationing is involved in shaping the production behavior of personnel. The administrative function of labor standards is not only to determine the time spent on certain operations, but also to establish an algorithm for their implementation. The more directions the labor organization model used in production has, the more pronounced is the manifestation of managerial functions, which subsequently determine the degree of effective management of all production processes.
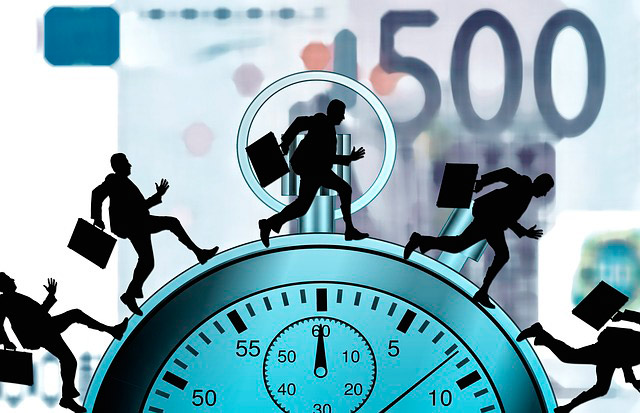
The social significance of labor standards cannot be discounted. In the process of the emergence of labor processes and the trusting relationship between management and staff, a special role is played by the confidence of employees in the desire of management to maintain labor safety, increase the prestige, the attractiveness of production work, the satisfaction of performers with working conditions and material remuneration.In addition, the regulation of labor in the legal field establishes the duties and rights of each employee, regulates the interaction between representatives of the managerial level and subordinates, ensuring legitimate mechanisms for resolving conflicts in accordance with labor legislation. Also, the active use of labor standards allows us to establish exemplary discipline in production and to stop its violations.
Labor standards in the outsourcing sector
. , , , :
, , , . -, . . , , , -, , , , . .
? It is impossible to unequivocally answer this question. , :
, , .
All processes in the economy are interdependent and interconnected. Moreover, the role of economic factors in the development of labor relations during the crisis is growing rapidly. Business owners are trying to do everything in order to get maximum income with minimum expenses. Each entrepreneur is looking for his own formula for success, but on the whole there is a noticeable trend:
- reduce staff;
- efficiently distribute and rationally use labor resources;
- save working time and prevent its losses;
- avoid factors that could negatively affect the quality of manufactured products or services.
At the same time, the employees themselves also strive to use their working time with the greatest efficiency, but wish to work in safe conditions at a satisfactory degree of intensity. Consequently, all parties to labor relations are interested in rationing.