The effectiveness and quality of work depends on the availability of the necessary tools, materials and skills. Success in any business, no matter what direction it is, is also significantly affected by knowledge of the theory. Welding is considered to be one of the most common.
This type of activity requires material, equipment, work experience, as well as theoretical knowledge. Having mastered the necessary information, a person gets an idea of ββwhat a seam is, what kind of classification of welds exists and how to choose the best option for adhesion of various metal products.
What is a weld?
During welding, three metal sections are involved in the process: two pieces of iron are fastened together with the help of a third, which acts as an electrode. At the junction of metal parts with each other, a thermal process occurs, forming a seam. Thus, a seam is a part of a metal structure obtained as a result of exposure to fused and hardened iron.
Any metals can be joined by welding. They have their own structural features, according to which a certain type of fastening is selected. The classification of welds is made depending on the type of adhesion, material and other parameters. Each connection has its own instructions and its own execution order.
Dimensions
There is a classification of welds by length. Depending on the size, welding seams are:
- Short. The size does not exceed 30 cm. Such a seam appears as a result of welding performed in one direction from the very beginning to the end.
- Medium. The seam length is from 30 cm to 1 meter. These seams are welded from the middle to the edges. The reverse step method is ideal for them. Its essence lies in the fact that the entire seam is divided into several sections, which are alternately processed by welding. Each of these segments has a length of 10 to 30 cm.
- Long (over one meter). They are welded in the same way as the middle seams, with the only difference being that the number of sections here will be greater.
Types of welded joints
Classification of welds is also carried out according to the type of fastening. There are four types of compounds:
- butt;
- T-shaped;
- overlap;
- angular.
Most common type
During butt adhesion, the thickness of the product is taken into account. This saves a significant part of the material.
Butt grip is considered the most popular. This is due to the fact that this welding process is the fastest and most economical.
T-welding. Features and recommendations
This type of clutch is characterized by a T-shaped connection of metal products. As in the butt joint, special attention is paid to the thickness of the metal, depending on which the seams are unilateral and bilateral.
When applying this type of clutch, it is necessary to adhere to the following recommendations:
- Performing T-welding in the adhesion of two products having different thicknesses, it is necessary to keep the welding torch in relation to the product thicker at an angle of 60 degrees.
- Welding work can be facilitated by placing the structure in the boat. This position of the workpiece will exclude undercuts, missing undercooked areas, which are considered the most common defects for this type of clutch.
- If one pass of the welding torch is ineffective, because defective areas may remain, they should be cooked by oscillating the welding electrodes.
- In T-joints, one-sided welding can be limited. To do this, use Oineo Tronic Pulse welding equipment, which allows RW cooking.
Lap welding
The principle of this type of connection is the two-sided welding of products whose thickness is not more than 1 cm. This welding is used in cases where it is necessary to prevent moisture from entering the gap between the steel sheets. As a result of such work, two seams are formed. This type of welded joint is considered to be long and not economical, since more materials are required for work.
Corner grip
This type of welding is used to connect metal products in a position perpendicular to each other. Depending on the thickness of the sheets, corner welding is characterized by the presence or absence of beveled edges. If necessary, this type of connection is made from the inside of the product.
Weld Shapes
The classification of welds according to the shape of the outer surface defines three types:
- Flat. Effective under dynamic and alternating loads, since these seams (as well as concave ones) do not have a stress concentration that can cause sudden changes and destroy the welding adhesion.
- Concave. The concavity of the seam, not exceeding 0.3 cm, shall be considered admissible. Otherwise, the concavity of the weld shall be considered excessive and shall be regarded as a defect. The concavity level is measured in the area where there is the greatest deflection.
- Convex seams. They arise as a result of the accumulation of a large amount of solidified metal and are considered uneconomical. But at the same time, a welded joint giving a convex seam is more effective under static load than a joint with a flat or concave welded seam. The bulge is the distance from the surface of the base metal to the point of greatest protrusion. Convexities not exceeding 0.2 cm for lower welding and not more than 0.3 cm for welding performed in other positions are considered standard.
Classification of welds by position in space
According to the space placement criterion, there are four types of welds, each of which has its own characteristics and recommendations for welding:
- Bottom seams. In the technical aspect are considered the simplest. Welding of the lower seams is carried out on a flat surface in the bottom position. This process is characterized by high efficiency and quality. This is due to more comfortable conditions for the welder. The weight of the molten metal is directed into a horizontal weld pool. Itβs easy to keep track of the bottom seams. Work is fast.
- Horizontal seams. Weld a little harder. The problem is that the melted metal flows under the influence of its weight on the lower edges. This may result in undercutting at the top edge.
- Vertical seams. They are the result of joints of metal products placed in a vertical plane.
- Ceiling seams. This welding is considered the most difficult and responsible. It is characterized by minimal comfort. The welding process makes it difficult to emit slag and gases. Not everyone can cope with this matter, a lot of experience is needed, since it is not easy to keep the slag falling on the face during work. It is important to observe the quality and strength of the connection.
How are welds and joints labeled?
Classification and designation of welds is carried out using special icons, lines and leaders. They are placed on the assembly drawing and on the structure itself. The classification of welded joints and seams is indicated, according to the regulatory document, using special lines, which can be solid or dashed. Continuous denotes visible welds, dashes - invisible.
Symbols of the seam are placed on the shelf from the leader (if the seam is located on the front side). Or, conversely, under a shelf if the seam is placed on the back. Using the icons, the classification of the welds, their intermittence, and the placement of segments for welding are indicated.
Next to the main icons are additional. They contain supporting information:
- on removing the reinforcement of the weld;
- on surface treatment for a smooth transition to the base metal and to prevent sagging and bumps;
- about the line along which the seam is made (whether it is closed).
For identical designs and products of one GOST standard symbols and technical requirements are provided. If the design has the same seams, then it is better for them to give serial numbers and divide them into groups, which are also assigned numbers for convenience. All information on the number of groups and seams should be indicated in the regulatory document.
Seam position
Welds are classified based on the position of the weld. They are:
- One sided. They are formed as a result of welding sheets, the thickness of which does not exceed 0.4 cm.
- Bilateral. They occur during the double-sided welding of metal sheets with a thickness of 0.8 cm. For each connection, it is recommended to leave 2 mm gaps to ensure adhesion quality.
Possible flaws
Defects during welding can occur due to excessively high current and arc voltage. It may also be the result of improper manipulation of the electrodes. Classification of defects of welds at their location:
- Internal To identify them, a technique is used that consists in the control: not destroying the structure, destroying fully or partially.
- Outdoor. They are easily detected by external examination.
Due to a violation of the welding mode caused by a lack of necessary experience, insufficient preparatory work, incorrect measurements, defects are divided into:
- Lack of penetration. It manifests itself in the local absence of fusion between the connected elements. The defect leads to an increase in stress concentration and a decrease in the cross-section of the seam. A design with such a flaw is characterized by reduced strength and reliability. The cause of lack of penetration can be both insufficient current strength and fast welding.
- Undercut. The defect is a local decrease in the thickness of the base metal. This problem is observed near the boundaries of the welds.
- Burn through. The defect has the appearance of a cavity in the weld. It occurs due to leakage of molten metal from the weld pool. Burn-through is an unacceptable defect, it needs to be urgently fixed.
- An undigested crater or indentation. It occurs due to arc breaks during the approach to the end of the seam.
- The influx. The defect is manifested in the flow of weld metal onto the base metal without fusion.
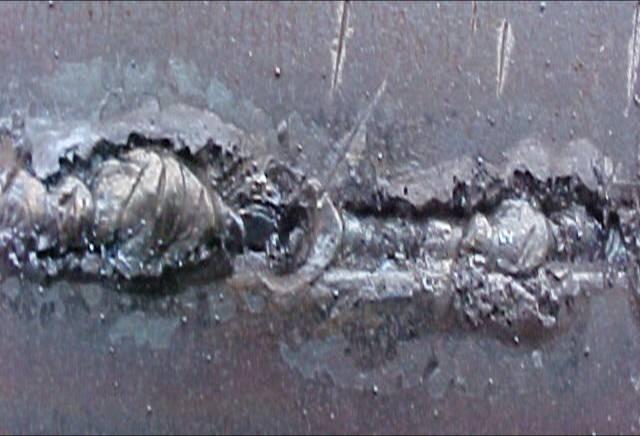
The causes of defects can be very different, but they are equally able to reduce the adhesion strength, operational reliability, accuracy and spoil the appearance of the product.