After welding, mandatory flaw detection is performed to determine the quality of the weld, its surface structure and flaw parameters. Inspection must be carried out in a non-destructive manner so as not to damage the workpiece or the structure in use. The capillary control method, which is widely used both in construction and in industries associated with the use of welding operations, meets these requirements.
What is capillary flaw detection?
This is one of the most popular methods for detecting defects on the surface of the target workpiece. It is important to emphasize the applicability of control precisely to identify the parameters of external disturbances - this technique is not used to diagnose the internal structure of the seam. After welding is completed using the capillary inspection method, the master can record such characteristics of defects as surface position, length, orientation, etc. Cracks and insufficient penetrations are most often the target defects.
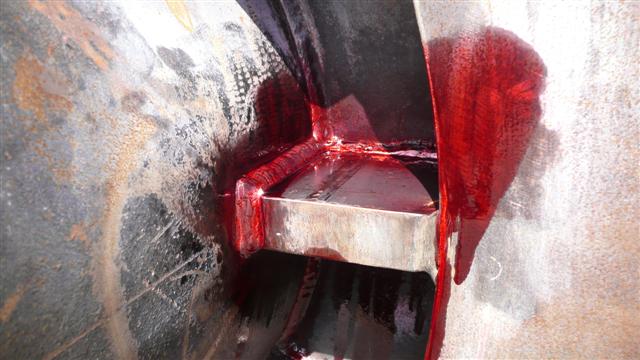
But why is it so important to use a special technique, ignoring the standard visual inspection, albeit with the connection of professional optics? One of the main advantages of this method is the ability to detect small defects that can be missed with traditional visual inspection. Using optical equipment like a microscope or a magnifier, for example, will not allow you to detect defects due to their low contrast against the background of a metal surface, not to mention the small field of vision at significant magnifications. In turn, the capillary technique allows you to fix flaws in large workpieces with high accuracy.
The requirements for the organization of work and the technique for their implementation govern the standards of the normative document for the capillary control method - GOST 18442. In accordance with the official definition, this technology for checking the quality of welds is presented as a way to analyze and record through and surface discontinuities of the material. By the way, the origin of the workpiece in a production or construction environment does not matter: in addition to ferrous and non-ferrous metals, the technology successfully works with ceramics, plastics and glass.
The essence of the method
The principle of operation of the capillary control method is to manifest the structure of the defect with the help of a coloring penetrant, which processes the target surface. The high penetrating ability of the active composition allows it to penetrate into the smallest pores of the surface, marking the contours of cracks or lack of fusion with bright color. Phased production technology of the capillary method for monitoring welds can be represented as follows:
- Surface preparation. The quality of flaw detection will depend on the cleanliness of the working area. The slightest obstruction in the form of dirt, dust and grease may interfere with the capillary marking process. Therefore, surface cleaning, and sometimes grinding, is carried out with subsequent refinement.
- Applying a coloring composition. As a rule, a red penetrant is used. It is sprayed or applied with a brush in sufficient volume so that the mass can freely fill all existing defects.
- Cleaning excess penetrant. To make it more convenient in the future to control the defective zone, unnecessary coloring solution is removed from the surface. It is important not to touch the marked contours of the cracks directly.
- Application of the developer. Some time after the penetrant dries, the developer is laid - the composition is white, which will allow revealing structural violations in contrast.
- Quality control. After the development process is completed, the operator fixes the traces and contours of the defects.
The functional nature of the capillary control method can be reduced to two technological factors for detecting defects. Firstly, this is the described process of point visual manifestation of the structure of cracks and lack of fusion. Secondly, this is a procedure for direct registration, measurement and analysis of defect parameters, but with the help of other functional tools.
Classification of the main methods of capillary defectoscopy
The most significant sign of the separation of different methods of capillary control is the type of indicator mixture - the same penetrant. The most popular red marker composition was considered above, but there are other variations that show themselves favorably in various flaw detection conditions. And in this context, the following classification of capillary control methods can be proposed:
- Luminescent. This method involves the use of a solution or suspension of a phosphor in combination with organic solvents, oils and kerosene. In the process of analyzing the revealed defect structure, special ultraviolet irradiation is not required - even in a dark room, the phosphor provides sufficient contrast, allowing microcracks to be fixed up to 0.1 microns thick.
- Luminescent color method. It gives the most sensitive effect of detecting external defects. Modification of the luminescent indicator, which consists in the use of long-wave ultraviolet radiation. The method is used in laboratory conditions for fixing ultra-small crack patterns.
- Brightness method. It is also called achromatic and is one of the most accessible and simple methods of capillary control, the capabilities of which are sufficient to verify the quality of most of the welding seams. Kerosene-chalk indicator fluid is used in the work, providing a contrast manifestation of the outlines of a possible defect.
- Filtered suspension method. In this case, it is not a liquid, but a kind of powder approach to the manifestation of the defect, which leads to its extremely low sensitivity. Nevertheless, the use of filtered dispersed particles of the suspension as a marker is the best control option when surface treatment of the workpiece with liquid solutions is not allowed.
Combined capillary flaw detection methods
A group of methods, a feature of which is a combination with other non-destructive surface control techniques. Moreover, the basis must necessarily be a method of marking a defect. So, the following combined methods of capillary inspection of welds are distinguished:
- Capillary electrostatic. Allows you to identify defects in non-metallic workpieces by the indicator trace, which was formed by particles of electrified powder on the surface of the penetrant.
- Capillary electro-inductive. As an additional active factor, an electric conductor is used that works directly along the penetrant contours without other foreign inclusions.
- Capillary magnetic particle. The method is specifically designed for ferromagnetic magnetizable products with defect monitoring along the indicator trail formed by the ferromagnetic powder above the penetrant layer.
- Capillary radiation. Control is carried out on the basis of the analysis of the spectrum of ionizing radiation in the area of ββthe defective zone, pre-treated with a liquid indicator.
The capillary method of non-destructive testing with the use of stable nitroxyl radicals deserves special attention. They are mixed with the basic composition of the penetrant and, due to the paramagnetism of nitroxides, make it possible to use spectroscopy of paramagnetic resonance. This is a highly accurate method for detecting microcracks that deeply penetrate the structure of the material, where conventional means of external analysis are ineffective.
Characteristics of the capillary control method

In the general group of non-destructive testing techniques, this method corresponds to the second level of sensitivity, at which defects may occur with an opening potential of up to 1 ΞΌm. To the target discontinuities can be attributed through defects, the cross section of which varies in the range of 0.1-500 microns. The main physical and operational characteristics of capillary non-destructive testing include viscosity, density, tension and penetration. In many respects, indicators for these parameters depend on the specific indicator composition. For example, medium penetrant impregnation is characterized by good wettability and high surface tension. Compositions based on kerosene, benzene, liquid oils and turpentine, in particular, provide a surface tension of up to 10-2 N / m. As for the luminance contrast coefficient, it can increase by 30-50% depending on the initial data of the marker and the conditions of application of the method.
Work Requirements
The following set of general requirements for control by non-destructive capillary methods is given in the normative and technical documentation:
- The technology is intended for non-destructive flaw detection in order to detect through and surface discontinuities in workpieces after welding activities.
- In the process of flaw detection by capillary methods, the dimensions of cracks, gaps, chips and other technological damage, including their position and orientation to the surface, should be detected.
- Capillary methods are designed to control objects regardless of their shape and size.
- The technology can also be used to control workpieces made of ferromagnetic materials. But in this case, the configuration of the location of the defects and the magnetic properties of the product must correspond to the operating characteristics of the applied marking composition.
According to the requirements of GOST by the capillary method of non-destructive testing, the handling of penetrants and other indicator impregnations due to chemical activity should also be based on fire safety rules approved by another GOST - 12.1.004-91.
Preparation for work
First, a visual inspection of the workpiece and its surfaces is carried out. It is important to pre-mark the areas that will be subject to control. Zoning will enable comprehensive diagnostics without missing hard-to-reach surfaces. Further, on conditionally marked areas, stripping is performed. At the stage of preparation for performing capillary control of welded joints in critical structures, it is recommended to use solvents and machining agents. Liquids for dissolving substances will eliminate the traces of oil and grease stains on the surface, and, for example, a sandblasting device will eliminate scale and rust from the coating. If there is no pneumatic tool at hand, you can use simple abrasives like a metal brush or sandpaper. After mechanical grinding, surface washing and drying are performed.
The use of special equipment will also require the operation of troubleshooting. A typical method of capillary control of welded joints involves the use of the following instruments and devices:
- Complex equipment for non-destructive diagnostics, which includes developers, cleaners, penetrant containment agents and other devices.
- Spray guns. A tool for spraying a liquid indicator.
- Pneumohydropistols. Also allows you to perform cleaning operations in the course of work and carry out the application of technological compounds,
- UV light device. Rather, an optional snap-in, but if high quality diagnostics are required, then you can not do without it. Usually use UV lamps, flashlights and other illuminators with contrast radiation.
- Test panel. A kind of test platform on which work procedures are performed. Moreover, in some cases, flaw detection is performed on the road when it is necessary to examine the weld of a stationary structure. In such cases, mobile panels are used for convenience.
- Photographic equipment for visual inspection. At the final stage of work, such equipment allows automatically registering defect parameters at the software level.
Capillary flaw detection technique
The most time-consuming and at the same time crucial stage of flaw detection, which can be divided into separate procedures:
- Filling cavities with penetrant. After stripping, the prepared solution is applied to the working cavity. Application techniques can vary from conventional brushing to ultrasonic spraying. Most often, a spray gun is used for such purposes. The coating is formed smoothly, without the formation of sagging and omissions. According to GOST according to the capillary control method, to ensure high penetrating ability, the surface temperature must fall within the range of +10 ... + 50 Β° C. The temperature regime of the marker itself depends on its composition, but exceeding the same +50 Β° C is undesirable.
- Penetrant adjustment. Using a rag or napkin, it is necessary to remove the excess liquid applied, if necessary, carefully filling the missing volume in the areas of its divergence along cracks. The discontinuity surfaces should not be in contact with other objects. After that, the working areas are left to dry.
- Application of the developer. A thin developer of white color is also applied with sprayers or hand tools in 2-3 layers. This operation, as already mentioned, is required to create a contrast between the display zone and the base of the workpiece. If the capillary control of the welded joint was correctly performed, then the width of the formed marker trace will be several times greater than the actual width of the conditional joint crack, which will make it possible to easily detect small defects.
Defect registration
The final stage, during which not only the facts of the presence of certain surface flaws are recorded, but also their specific characteristics. For direct documentation of flaw detection results, photo and video equipment can be used. If the conditions are not suitable for using specialized visual inspection techniques, then an adhesive tape is used, on which a discontinuity pattern remains. Conversely, under laboratory conditions, the capillary method of non-destructive testing implies the possibility of high-precision processing by means of photographic and x-ray equipment. Filmed materials are transmitted via a special interface to a computer, where the corresponding software reflects the results of flaw detection in the form of visual graphs and patterns of the smallest cracks in the workpiece structure.
Conclusion
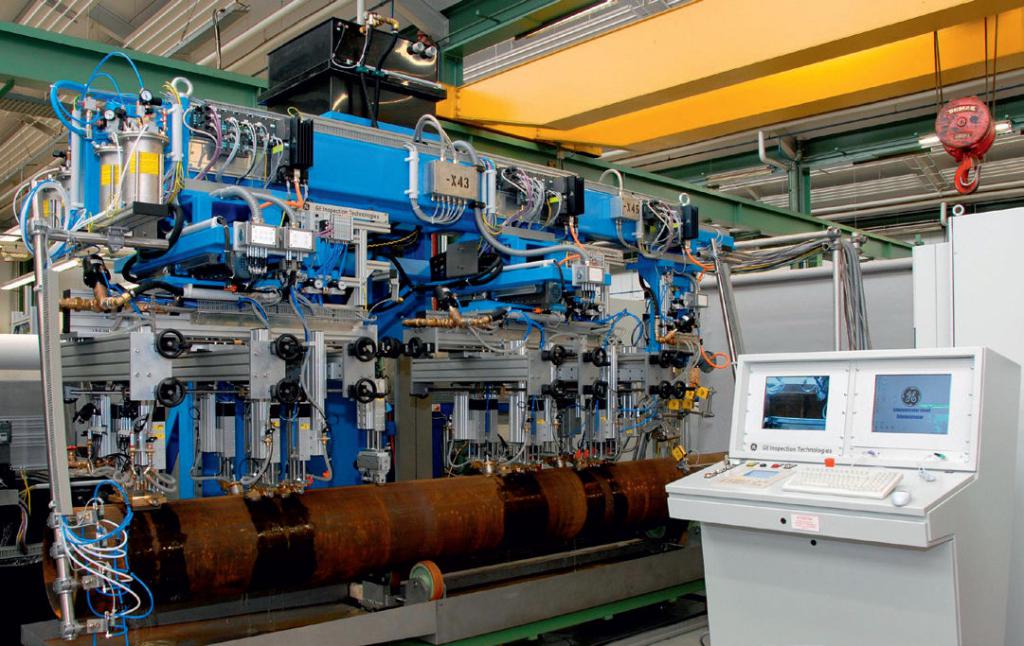
This method of non-destructive diagnostics of welded joints can be used both as an independent flaw detection operation and in a comprehensive inspection of structures. In the second case, the method of capillary color control will be performed primarily, indicating possible foci of discontinuity location. Next, methods of internal diagnostics are used, revealing voids and large pores in the structure of the workpiece. How effective is this method compared to alternative surface analysis techniques after welding? Today, this is far from the most technologically advanced method of flaw detection - especially against the background of electromagnetic and ultrasonic devices, which with high accuracy and with minimal organizational costs make it possible to obtain an equally worthy result. Nevertheless, precisely because of its simplicity and financial affordability, capillary control is still popular in surveys at remote sites where it is not possible to fully use modern equipment.