Laminate is a well-known floor covering that has long won the sympathy of people due to its strength, practicality, durability, comfort and low cost. A floor made of good material looks expensive and presentable. At the same time, practical characteristics also remain high. Installation of such a coating is simple and does not require special skills. Many use the laminate for many years, mistakenly believing that the reason for this is only its quality. People are willing to spend a lot of time choosing material for flooring, disregarding preparation for laying it. In fact, the duration of operation and maintaining an attractive appearance by 90% depends precisely on the quality installation of the coating, where one of the main roles is played by the substrate for the laminate. Therefore, the correct choice of the substrate depends on how long and practical the floor will last.
Substrate Purpose
The main functions of the substrate include slight floor leveling, moisture absorption and sound insulation. The fact is that in its structure the laminate is a very capricious and weakly protected material. This is pressed wood dust coated on both sides with cardboard. And only on the front side the material has an ornament covered with a film that protects the coating from moisture and abrasion. But in case of moisture penetration between the seams of the laminate panels, the floor can โswellโ and creak when walking. By virtue of its purpose, it is a dense material that abuts against the base of the floor and cannot independently absorb physical effects. It turns out that each step will be felt and "give" when walking. Moreover, even minor floor irregularities adversely affect the fastening of panels, which when exposed to an uneven floor quickly wear out and cease to reliably perform their functions. The result is a creak, chips along the edges of the panels, since the floor is no longer a single unit, but is divided into sections of poorly bonded panels.
It is the substrate on the floor under the laminate that prevents its deformation due to small irregularities, does not allow moisture to penetrate from the base and performs small cushioning and soundproofing functions, โsofteningโ walking. From this it can be argued that it is absolutely necessary to ensure a long and comfortable service of the material, as well as to preserve its appearance.
Varieties and choice of substrates
There are several types of substrates for a laminate, which should be selected based on the following parameters:
- which laminate will be laid;
- on what basis;
- how smooth the base is;
- what are the indicators of moisture and room temperature.
Now we will consider in detail which substrates for the laminate exist:
- Foamed polypropylene.
- Cork.
- Foamed polystyrene.
- Coniferous.
- Foil.
- Polyethylene film.
- Combined substrates.
Foamed Polypropylene
This type of substrate is interesting in its absolute moisture resistance and the ability to effectively smooth out unevenness and floor thresholds. But polypropylene does not withstand physical pressure and can be of different thicknesses if its bubbles burst as a result of a large load. Also, such a substrate will not be able to protect against noise.
Cork backing
This type of substrate will last a long time and deliver only pleasant sensations from use. The cork does not mold and does not rot, perfectly absorbs the load and is absolutely environmentally friendly. But the disadvantages include its high price and poor moisture resistance. However, here the manufacturers were not taken aback and offered their customers a rubber-cork substrate or bitumen impregnation for rooms with high humidity. But still it's not worth joking with humidity, and experts advise putting a plastic film on the floor base before laying the cork under the laminate .
It should also be noted that the cork is very demanding on a completely flat surface. With large and constant loads (for example, with furniture pressure) in places with small gaps, the coating simply swells.
Expanded polystyrene
This substrate is most common on the modern market of materials for construction and repair, as it is produced by many domestic manufacturers. The advantages of extruded polystyrene foam include durability, high thermal insulation, moisture resistance and the ability to easily withstand heavy loads. But at least a little to level the base of the floor, he is not able, therefore, it is used exclusively on a perfectly flat surface. Also a serious disadvantage of polystyrene foam is its high flammability. In the event of a fire, the fire will instantly spread through this material. And the valuable properties of expanded polystyrene will last no more than 7 years. It turns out that such a material will not be suitable for a long and safe floor service.
Coniferous substrate
It is pressed wood glued with natural resins that are contained in needles. Available in the form of plates and laid accordingly without any additional devices and adhesives. It is breathable and free of toxins. The advantages of such a substrate also include excellent sound insulation and damping of vibrations when walking. Also, the needles are endowed with the ability to retain heat as much as possible and not allow cold from the base of the floor, and therefore such a warm laminate substrate is widely used in the northern regions. Even the manufacturers noticed softness of conifers, which began to be used to even out irregularities, sometimes even significant ones.
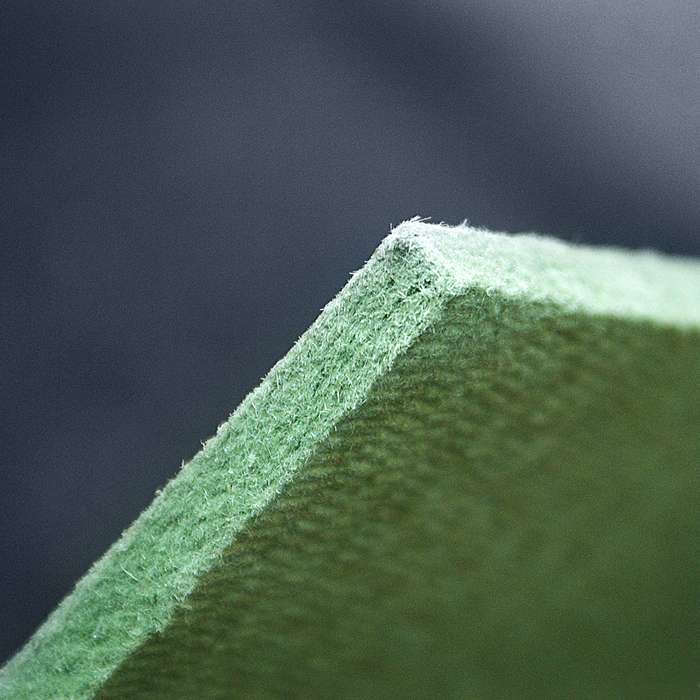
But not without flaws. Due to its "breathing" abilities, the needles are excellent moisture permeable, which contributes to the formation of fungus and mold. The conditions for their appearance are low temperature and humidity in the room. Therefore, lay out such a substrate should be exclusively on a dry base. In case of excess moisture, needles should not be used as a substrate, despite all its advantages.
Foil backing
This substrate is coated with a metal foil glued to one or both sides of the substrate. As the latter, polypropylene or expanded polystyrene can be used. All layers are glued together to perform different functions.
Mostly such a substrate is used for more reliable protection against moisture through the screed and to increase thermal insulation up to 30%. With foil backing, there is no need to use a plastic film for wet rooms. It will also be the best laminate backing in places with a risk of mold and mildew. According to experts, the most suitable thickness for such a substrate would be 5 mm.
Polyethylene film
Despite the continuous development of laying technologies, a plastic film is still used as a substrate for the laminate. Naturally, it will be deprived of almost all the properties and advantages developed by technologists of modern substrates, but polyethylene is the most budgetary option for laying flooring. Of course, every stacker should understand that when using such a substrate in a couple of years its minimum qualities will be lost, as well as the properties of the laminate itself. But if the aim is not to provide a comfortable and long service life of the material, but to put the object into operation, then this option is most suitable for the task.
When laying such a substrate, it is better to use a film 0.2 mm thick, packed in rolls, and lay out with an overlap of 20 cm.
Combo Substrates
This type of laminate substrate combines polypropylene and expanded polystyrene. But when laying on a warm floor, you need to choose a substrate of small thickness, which will not only fulfill its main functions, but also let heat through.
There are cases of combining polyethylene foam with a polyethylene film to prevent mold in wet rooms.
In order to absorb sound from steps, substrates based on foamed polyethylene with high noise absorption can be used.
Today, many well-known manufacturers offer their products with a finished substrate glued to the material. The quality of such a substrate usually reaches a high level and does not cause unnecessary laying trouble. But the cost of such material exceeds the usual.
So, in order to answer the question of which substrate under the laminate is better to purchase, you need to know the characteristics of the particular room and the base of the floor on which the installation will be made.