The concept of floating flooring arose a long time ago and in the early stages of development was expressed in the rejection of the adhesive method of installation. The transition to mechanical locking joints of flooring elements was caused by the desire to eliminate or minimize deformation processes. They arose due to the natural movements of the base of the building, which were reflected in the decorative coating. Accordingly, the rejection of direct interface with the carrier base extended the service life of the material being laid. Today, a floating floor is not just a set of coating elements formed by locks, but a design technologically advanced in its structure, devoid of close interfacing with the rough foundation.
Technology Overview
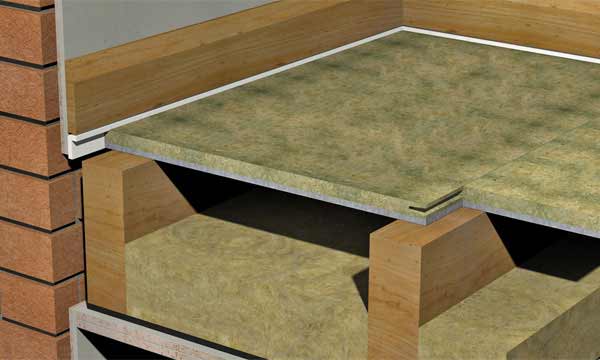
To solve the problem of eliminating, at first glance, the necessary component of the ligament in the construction of flooring, there are various ways. And here it should be noted that increasing the strength of the flooring with the protection of its structure is far from the only goal that the authors of the technology pursued. For example, when laying laminated panels, the task of ensuring sound insulation comes to the fore. Technically, a floating floor system is implemented by damping interlayers. Again, the choice of materials for such an insulator and its structural performance will be determined by the requirements for the result. Side wedges also help eliminate the risk of deformation of an expensive flooring in the form of the same laminate or parquet. This is a special hardware that softens impact under dynamic loads on the floor. But most often, floating coatings are associated with the capital device of the substrate, connecting the decorative layer on the surface and the base.
Materials and consumables
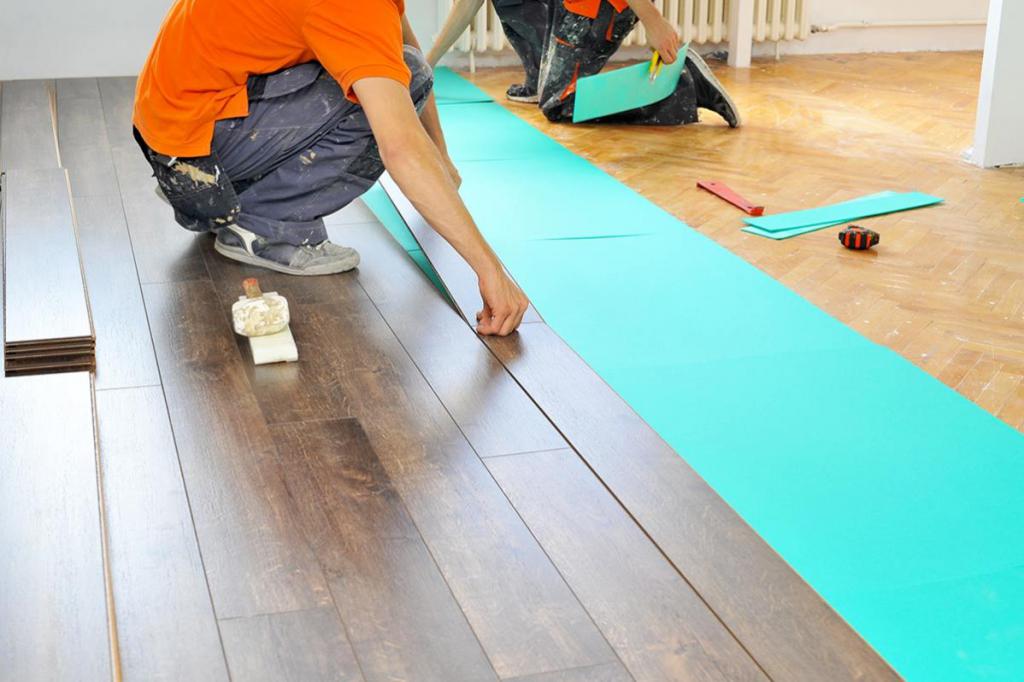
It should immediately be emphasized that the flooring itself is not an element of the damping system. Unless linoleum with a cork as such can complement this function, but the key link will still be a special elastic substrate. In particular, it can be felt screed, polystyrene or mineral wool. Sheets or panels with a thickness of 4-5 cm are used. If it is planned to make a substrate for a hard coating (boards, laminate, parquet), then reinforcement with a mesh should also be provided. Thanks to the reinforcing thin rods, the damping layer will retain its structure and functionality. There is a group of special substrates to improve sound insulation. So, for a floating wooden floor, it is worth using an eco-plate, corrugated cardboard or cork mats. The noise reduction index, depending on the characteristics of such a layer, is on average from 16 to 26 dB. The same applies to thermal insulation, but in this case the choice is not so wide and usually comes down to special modifications of the same mineral wool.
Floor construction
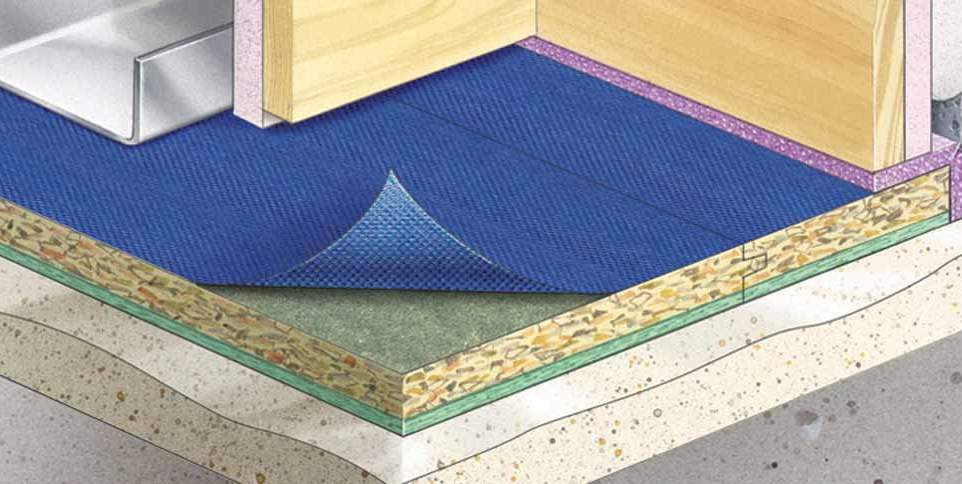
In the simplest systems, the device of such a flooring is based on the damper substrate and the decorative layer itself. If polystyrene is laid on a rough base, and laminate panels are on top, this will already be the target system without a tight bond. Nevertheless, professional SUVs implement floating coatings comprehensively and taking into account the small nuances of operation. If we consider the system from the lower region, then it will begin with a hard base. Logs, plywood sheets, screed or self-leveling self-leveling flooring are laid on the rough base. This layer is needed as the surface on which the damper sits organically. Next, go to the underlayer of the floating floor. The design in this part may include the special materials mentioned above, and expanded clay with rubber. This choice is made based on gender requirements. In addition to providing sound insulation and mechanical protection, for example, a barrier to moisture and steam may be required. This task is performed by vapor-tight foil membranes.
Installation work
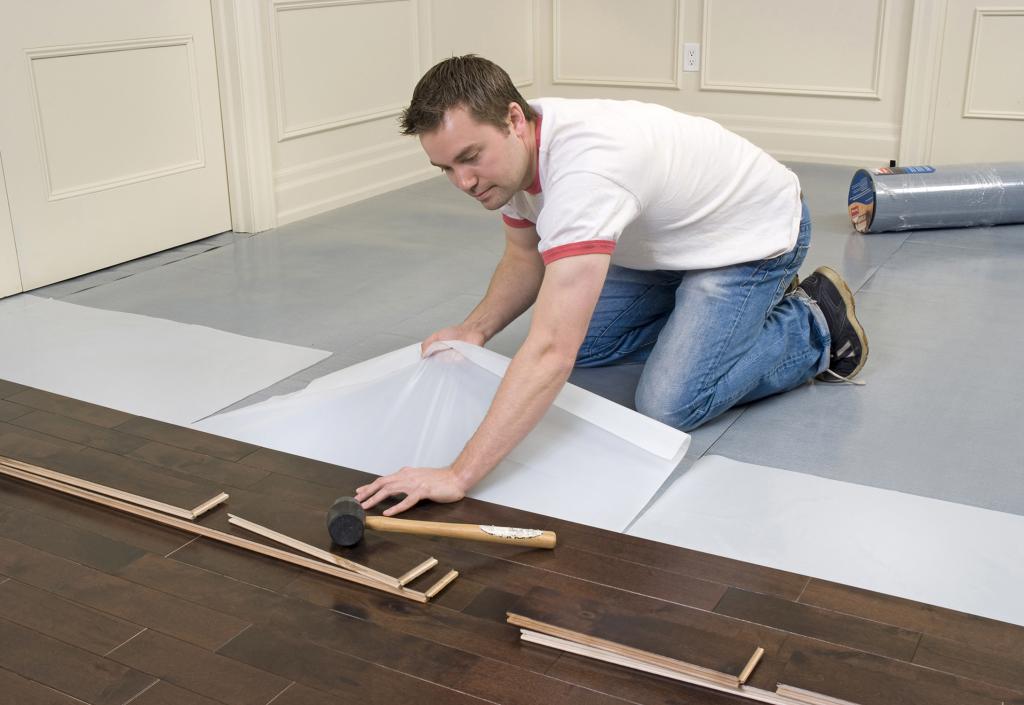
Although the list of the main tasks of the damping substrate includes leveling the defects of the rough surface, it is advisable to minimize them at the stage of preparation for work. Especially for this and lay a hard layer. It should eliminate irregularities and hide deep holes, if any. Already at this level, the device of floating floors allows the inclusion of basic insulators. It will not be superfluous to roll out thin vapor and moisture insulation. If we are talking about a private house and there are no serious restrictions on reducing the height of the floor, then you can organize a small layer of dry sand - it will contribute to the warming function. Then proceed with the installation of the damper material itself. We have already talked about the different types of this substrate, but it is equally important to pay attention to the format of its delivery. It can be rolls, plates, thin panels and mats. Accordingly, rigid products are fixed with locking mechanisms (included), and elastic material is usually beaten with hardware or glued. Now you can consider turnkey solutions for floating flooring from major manufacturers.
ISOVER Models
Under this brand, a whole series of mineral wool panels is produced. The structure of the material is formed by natural components, including fiberglass, limestone, sand and soda. A synthetic binder is also present in the composition, but its content, as a rule, is minimal. By designation, such plates are more likely to be suitable as a solution for insulation - noise reduction, insulation, etc. By the way, the sound insulation coefficient reaches 37 dB. It features ISOVER floating floor and physical resistance. The compressive strength is about 20 kPa, so this base can be used in combination with hard decorative coatings.
Knauf Models
This manufacturer is known for its unique design in the form of waterproof plasterboard panels. They are also used as insulators, but in this context, it is interesting modifications for the installation of a prefabricated floor base. This is a βKnaufβ floating floor made of gypsum-fiber elements 20 mm thick. The functional emphasis of the coating is focused on protecting against the spread of moisture in the room, but such a stove performs the tasks of leveling the rough foundation at a high level. The main thing is to initially create a solid base on which drywall can be used for years.
Rockwool models
If specialized solutions for commercial and industrial use are required, then the RockWOOL SeaRox range of tiles should be consulted. Stone cotton is used as the basis of this material, the outer part of which is provided by a galvanized wire mesh. The thickness of the plate can reach 70 mm, which speaks of a special purpose - substrates of this format are optimally suitable for arranging work shops, offices, corridors of public institutions, etc. Reinforced aluminum foil indicates the possibility of using the floating floor of this company in harsh conditions, the presence of fiberglass for some models and other insulating coatings. According to the manufacturer, SeaRox sheets can withstand thermal loads of around 250 Β° C. This indicator of heat resistance opens up the possibility of using coatings even in the decoration of metallurgical industry facilities.
Features of floor care
The main structural maintenance work consists in updating consumables and applying protective coatings. This is especially true for prefabricated systems that allow for dismantling. Having disassembled the coating, it is possible to replace worn felt linings, deformed plates and aged fasteners. As for the protective layers, the floating floor from the side of the damper is often treated with varnishes and mastics. They will not relieve physical stress, but will protect the structure from biological destruction, which is important for natural materials. The condition of the decorative material on both sides should be checked regularly. It is desirable that an insulator with a strong structure separate it from the elastic base.
Pros and cons of a floating floor
With the merits of technology, everything is obvious. It allows you to minimize physical stress on the decorative surface, improves insulation and generally makes the operation of the floor more enjoyable. But the weaknesses of this design should be taken into account. They are reflected in the complexity of installation work, cost and the need for special services. In small apartments, floating floor technology is completely undesirable due to the reduction in height in the room. At least the flooring will be raised to a thickness of a few centimeters, and if you add a group of thin insulators with a reinforcing layer and a base rigid base, then we will talk about 10-15 cm.
Conclusion
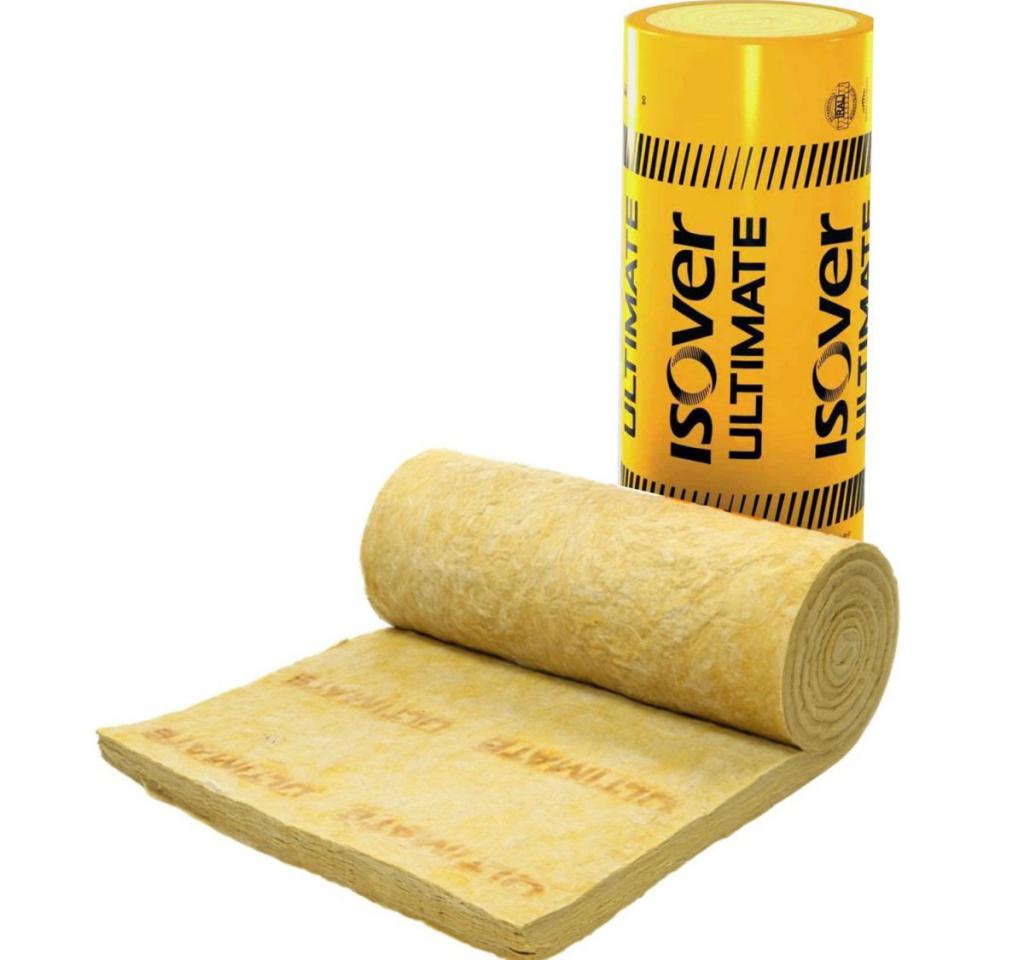
The considered method of arranging the floor is more focused on solving existing problems of its operation. If it is planned to use a laminate, then unpleasant acoustic effects can be expressed, and in houses with poor external insulation, respectively, the problem of warming by means of a floating floor will be solved. The design and device of this system can also be characterized by multifunctionality. Even using improvised means with minimal investment, a skilled home craftsman will be able to implement a structure that increases the strength of the floor, its protection from moisture and cold. If you exclude specialized plates and mats, then the functions of insulators can be assigned to polyethylene, and the cork substrate will provide a damping effect. By the way, the use of needles for lining under laminated panels has been practiced recently. This is not the most profitable solution from the point of view of increasing the structural strength, but this material provides sound insulation with insulation at a high level.