Stonehenge in England, the Peruvian citadel in Machu Picchu, the pyramids of the pharaohs in Egypt - all these great creations of ancient architecture are evidence that natural stone is one of the oldest and at the same time strong building materials in human history. But working with him is very difficult, it is difficult to transport and extremely laborious to process and install.
It would be nice to have a similar material in the form of batter, giving it an arbitrary shape, which after solidification would acquire the properties of a stone. Such an amazing “liquid stone” exists, and we call it concrete. It is a composite material that includes three main elements.
Three simple ingredients for an ideal building material
- Cement (the common name for calcium silicates and aluminates) - occupies 10-15% of the total solution volume.
- Water - 15-20%.
- A mixture of coarse and fine aggregates (sand, gravel, large pieces of crushed rock, recycled glass, etc.) is usually 60-75%.
Speaking about concrete as a composite material, you need to understand that its ingredients, which are not similar to the final product, acquire high strength and durability not just as a result of the drying of the solution, but due to a chemical reaction. When water is added, crystals of cement hydrate begin to grow, forming a crystal lattice and tightly bonding sand and gravel. It is because of this that after pouring concrete has to be moistened for several days, and obtaining a good result is possible only if a number of technological requirements are observed.
Two stages of "growing up" concrete
Due to the fact that this building material is “born” in a liquid state, almost any desired configuration can be given to concrete pouring molds, after which, as a result of hydration, setting and then the concrete hardening stage take place.
- Curing is perhaps the most important and sufficiently fleeting process that begins about two hours after the solution solidifies and ends within an hour after that (at 20ºC). This period is very dependent on the pouring temperature of the concrete and, for example, at 0ºC it can take up to 20 hours, and in the heat, the setting time, on the contrary, decreases significantly.
- Hardening is a nonlinear process that proceeds most dynamically in the first stage, when concrete, within about a month, gains most of its strength, while its final hardening occurs only after a few years.
Everyone has flaws, but the iron core inside will solve any problems.
It’s worth immediately to understand that it is better to pour concrete prepared by an industrial method, purchasing it from a trusted manufacturer, guaranteeing its compliance with the declared brand. This is the only way to obtain material that meets the requirements predefined by the customer and is reflected in the concrete passport (density, filler fraction, frost resistance, water resistance, mixture mobility).
One of the main characteristics that determined the widespread use of concrete is its ability to withstand significant physical compressive loads. For this indicator, the density is determined, determined by the ratio of the mass of the material to the occupied volume. In heavy grades of mortar filled with natural stone of various fractions (gravel, pebbles or gravel), the weight of one cube of concrete pouring is from 1.8 to 2.5 tons. Materials of this type are used in the construction of structures experiencing significant loads (supports, floors, foundations, etc.). For lightweight concrete used for the construction and insulation of walls, floors and lightweight ceilings, perlite, expanded clay and all kinds of foamed polymers are used as fillers. The density of such a solution varies from 0.6 to 1.8 t / m 3 .
Unfortunately, a big disadvantage of concrete is that it can withstand tensile loads about 10 times less than under compression and easily break even with slight bending. This problem is solved by pouring concrete around twisted steel rods (reinforcement), fastened to each other in the form of a lattice.
After hardening, a new composite material is obtained - reinforced concrete, in which concrete provides compressive strength, while steel resists bending and stretching. Sometimes other materials are used for reinforcing, including various types of plastics, but steel has hot and cold deformations about the same as concrete, which means that the material will not collapse from the inside.
The fundamentals of reinforced concrete longevity
It is clear that for a number of objective reasons there is no expediency or possibility in ordering a solution from professional suppliers. Moreover, observing the technical conditions, even by pouring concrete with your own hands, you can get a good result.
The foundation of the house is its foundation and the guarantee of the trouble-free functioning of all that it is called upon to support. There are a great many ways to bookmark it: from block and pile - to create a tape monolithic reinforced belt. However, with all the wealth of choice, in all these cases it will be concrete, or rather, reinforced concrete. In the case of individual development, the most common is the last of the listed options. At the same time, the foundation is poured with concrete in a continuous layer around the entire perimeter of the future building, on top of the reinforcing cage.
All work on the construction of the foundation can be divided into three stages.
- Preparatory - site planning, rebar installation and formwork installation.
- Concrete pouring works - mixing, feeding, laying mortar and concrete care.
- Final - dismantling the formwork, visual inspection and elimination of minor defects.
Foundation: looking for answers to a lot of questions
The overall dimensions of the foundation, in addition to its obvious parameter - the length, depend on many initial conditions: the bearing load (type of wall material, number of storeys, the presence of a basement), type of soil, topography, groundwater level, depth of freezing, height of snow cover and much more .
If we are talking about the minimum dimensions, then the depth of the foundation should be at least half a meter, the extension above the ground is 30 cm, and the width should be at least one and a half times the masonry size of the wall material.
Formwork: a story about how form defines content
The formwork consists of a shield part and an abutment. When forming it, one must take into account that concrete in the first stage is a fluid solution that fills all the free space. Therefore, to obtain a good result, the shield surface should be as even as possible, not contain cracks and differences in height, and to maintain an ideal vertical, it is recommended to use a building level or plumb. At home, formwork panels are made of pine boards with a cross section of 20-25 mm, sewn together by a bar of the same material, as well as plywood, chipboard or metal sheets.
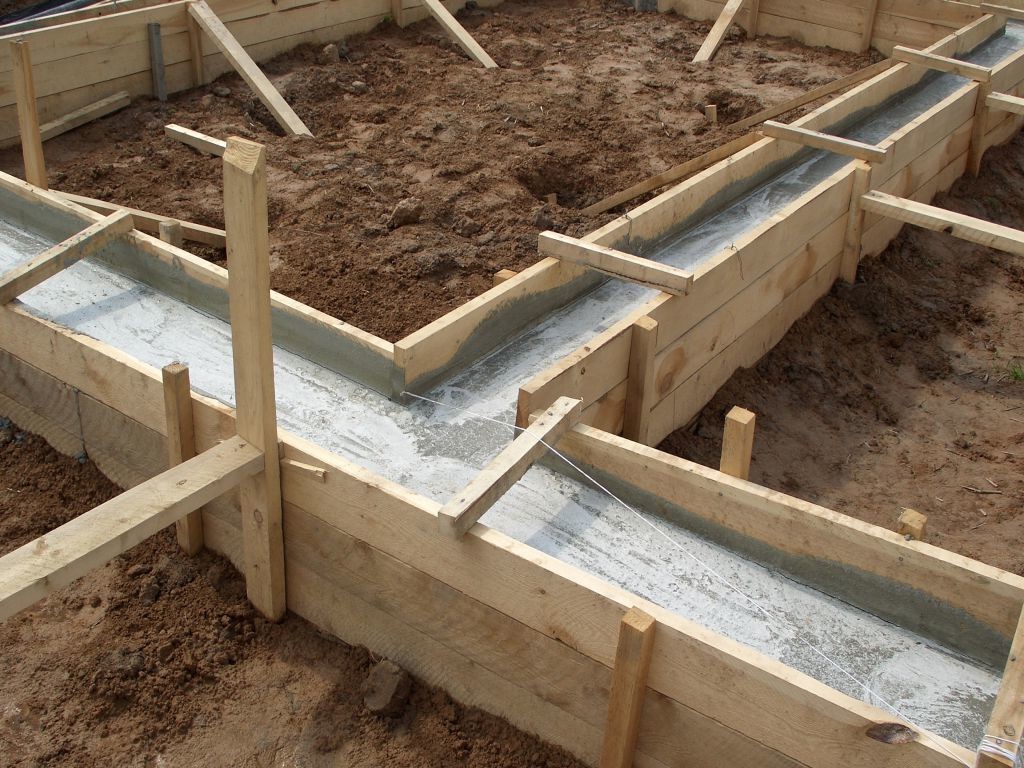
At the same time, it is extremely important not to forget about another property of the concrete mortar, namely its large specific gravity, because the thickness of the shield elements of the formwork and emphasis (usually wooden) should compensate for the pressure of the concrete mass. In addition, it is desirable to grease the working surface of the boards with solid oil or to cover them with a polyethylene sleeve, which will ensure the ideal smoothness of the foundation, eliminate the flow of the solution into the slots of the formwork and simplify its subsequent dismantling.
The reinforcement cage should guarantee an inextricable strapping over the entire surface of the future foundation, as a rule, from 70 to 120 kg of reinforcing bars account for one cubic meter of concrete, depending on the diameter.
The mystery of making concrete potions
At the next stage, the actual preparation of the mixture for pouring concrete is started. Since we are talking about private construction, we will use classic ten-liter buckets as a unit of measure. The brand of concrete depends on the ratios of the materials included in it and for the foundation most often use the M300. Such a solution corresponds to the following proportions: 1 bucket of Portland cement grade 400 accounts for 2 buckets of sand and 4 buckets of rubble. The amount of water strongly depends on the moisture content of the sand and is calculated experimentally during the first batch. Then all the ingredients are thoroughly mixed in a large container or concrete mixer. The finished solution should have a uniform, viscous consistency, not leak out through the joints of the formwork, and at the same time fill all voids well.
Concrete Mixing Procedure
It is necessary to lay the concrete mixture in uniform horizontal layers, about 20 cm high, distributing the solution over the entire width of the formwork and avoiding breaks. This is a very time-consuming and dynamic process, because in order to achieve ideal solidity of the foundation, the next layer of concrete must be applied before the setting of the previous batch. At the same time, during pouring (in the absence of a deep vibrator), the solution must be constantly stirred and pierced with an iron rod or crowbar to fill all voids and decontaminate the concrete in order to obtain a uniform foundation strength.
Healthy “childhood” of concrete determines its long life
Immediately after the completion of pouring, the concrete mixture maintenance phase begins, which, depending on weather conditions, takes from three to five days. This primarily concerns the periodic (every 2-4 hours) wetting of the concrete surface. The higher the temperature, the more often it is necessary to do this, but if the work is carried out in the cool season and the temperature ranges from 0 to + 5ºC, then watering is not done at all, protecting fresh concrete from direct sunlight and temperature drops with damp sand or sawdust. It is also necessary the first two to three days to prevent walking on the flooded surface and protect it from other mechanical damage. The strength of concrete increases most rapidly in the early days, and after a week and a half is about 70% of the declared brand indicators (28 days).
Now you can carefully remove the formwork and evaluate the result. If shells and corner chips are found, the foundation surface is rubbed with a solution based on sand and cement, and excess flows are removed with a trowel.
Concrete, as always, on top
All the advantages of concrete have found their application in the installation of floors. This is primarily strength, evenness, moisture resistance and durability, and the relatively high thermal conductivity in combination with the active use of warm floor systems these days smoothly migrated from the shortcomings to one of the priorities for using this type of material.
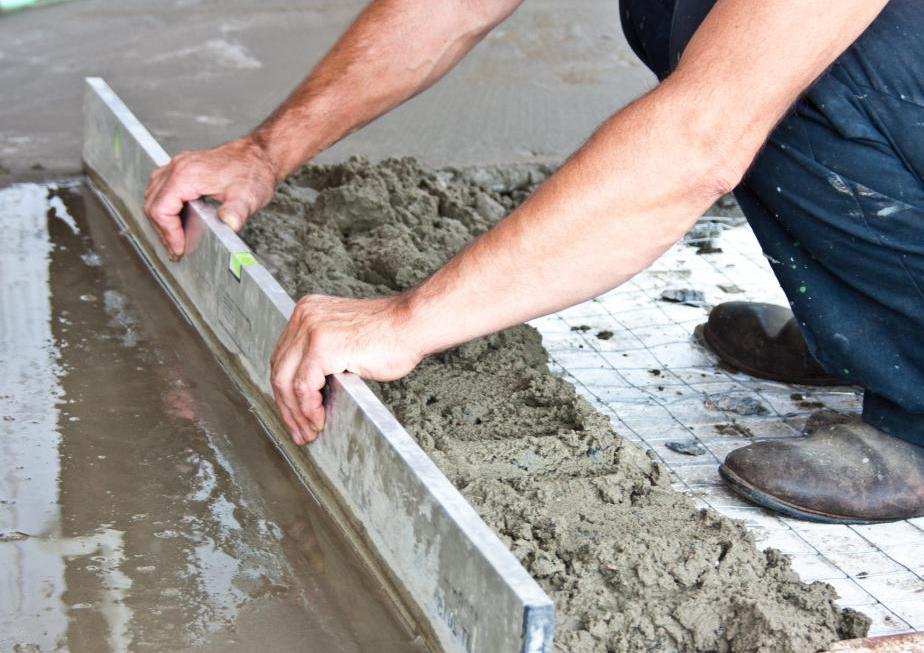
At the same time, the technology of pouring concrete floor is even simpler than the tape foundation device described above. The key point here is the quality preparation of the surface to be coated, which implies the presence of a solid foundation, the creation of a water barrier and thermal insulation for the future floor. In fact, the role of the formwork in this case is played by the flooded area and the walls of the room itself, and with a standard coating thickness of 6 to 8 cm, the whole process does not take much time. In addition, light concrete or fine-grained aggregates with a lower grade relative to the foundation used are often used for such work. As a reinforcement, they use wire masonry mesh, and the main difficulty lies in the ideal alignment of the guiding beacons, which can be cuttings of a regular pipe. Due to the significant size of the open surface, special attention should be paid to the care of the concrete screed after laying, which is similar to the measures given above.
With strict observance of fairly simple conditions of the technological process, concrete structures are able to fulfill the functions assigned to them for many years, pleasing with their reliability not only you, but also your grandchildren.