Wood may not seem to be the best solution for designing a subfloor in terms of strength and reliability, but in some cases it is quite justified for other operational qualities. For example, if you need to correct the shortcomings of the concrete base, create a niche for laying the insulator or create channels for communications. At the same time, the technology of attaching lags to the concrete floor is not as simple as in the case of ordinary wooden boards. Draft flooring is a crucial structural element, the durability of the decorative coating directly depends on the quality of the device.
Logs in the floor system
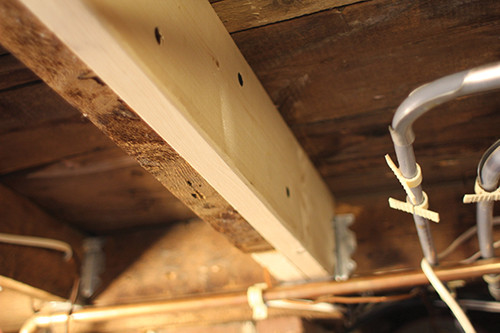
The floor frame consists of several levels, starting from the foundation with grillage and ending with the base, on which the finish coating is laid in the form of tiles, laminate, parquet, linoleum, etc. A concrete screed is usually used as the base material. It is less commonly used in wooden houses, but, for example, city apartments and private brick cottages cannot do without such a platform. The screed can serve as the final layer of the frame, and bearing in relation to the upper part of the base. A kind of superstructure on this design and form a log. They are not laid on a concrete floor in a continuous way, but with indentations of the type of crate. The mounting methods may be different, but the basic quality of the structure will be determined by the characteristics of the tree itself. The lags should be well dried out, free from small flaws and, if necessary, treated with special impregnations. This can be fire-resistant means to prevent fires, and ordinary drying oil, which extends the life of the material.
What tools and materials will be required in the work?
Large-format logs will be difficult to process at home, so it is better to calculate and order elements with the necessary parameters in advance. If this was not possible, then the preliminary processing of the log will require the use of an electric jigsaw, a circular hand saw and a grinder. Already in the process of attaching the lag to the concrete floor, an electric screwdriver or electric drill with bit nozzles will be needed. It is advisable to prepare a tool more powerful - at least with a 1500 W drive. As fasteners you will need metal fastening accessories - anchor elements, bolts, corners, screws, etc. The choice of one or another group of hardware depends on the installation technique.
As for auxiliary supplies, there will be few of them. At a minimum, lining padding is required. As such, plywood sheets or bars of the appropriate format can be used. Also, do not forget about the possibility of insulating coatings. The classic design of the floor on the logs makes it possible to lay both thin vapor-waterproofing insulators and a thick insulation in the form of mineral wool plates.
Varieties of lag for the floor
The most common floor log format is a beam with a rectangular or square cross section, which has length and thickness parameters suitable for specific application conditions. Especially for worm flooring, it is recommended to use rectangular logs as the optimal design option. A beam with such a section takes up less space in the underground niche, but at the same time provides sufficient coverage by segments along the width of the laying. Accordingly, the fastening of the lag to the concrete floor is simplified, since a shorter and stronger hardware is required to fix the element.
There is a division according to the method of manufacturing beams. Planed logs are specially treated to reduce hygroscopicity. This material is more resistant to moisture, so it can be used in the construction of baths and saunas. An alternative to planed beams are sawn bars. This is a rough material with less attractive technical and operational qualities, but it costs less and can justify itself as the first level of the floor frame connecting the foundation grill with the finishing layer of the log.
Calculation of material by size
The ability to cope with loads depends on the correct calculation of design parameters. These indicators, in turn, are determined by the size of the room, the layout and configuration of the premises as a whole. For the basic calculation, you can use the value of the span of the room, correlating it with the dimensions of the beam. For example, a 2-meter span should be made out with a bar with a cross section of at least 110 x 60 mm. For 4 m, a beam of 180 x 100 mm format will be required, and for 6 m, a standard size of 220 x 180 mm. In turn, the cross section will determine the distance between the elements. How to fasten the logs to the concrete floor so that a balance is maintained between the strength of the structure and the acceptable load on the supporting base under the beams? After all, close to continuous placement of the beam can cause excessive pressure on the same grillage. With a board thickness of about 20 mm, experts recommend maintaining indentation of up to 300 mm. At 300 mm, the same parameter will be already 500 mm, and 50 mm elements are located at a distance of 1000 mm between each other.
Preparation for work
In preparation, the greatest attention is paid to the condition of the concrete surface. As already noted, the load from the beams can be critical, therefore, the supporting base should be brought into proper condition. To fix the lag to the concrete floor is reliable and durable, the screed is strengthened with mortars, putties and primers. In case of significant damage, the cover should be renewed with a sand-and-cement pouring of an acceptable thickness of 4-5 cm. If we are talking about local small defects, then we can limit ourselves to the spot application of primers and puttying agents designed specifically for concrete. As a cosmetic leveling solution, it is worth applying a thin leveling fill with tile glue or a self-leveling polymer composition.
The main ways to fix the lag to the concrete floor
The most common installation methods involve fixing the beams using self-tapping screws and anchor joints. A tight fit with a clamp is provided, in which the structure remains stationary even under dynamic loads. How to fix the log to the concrete floor with anchors? To do this, holes are drilled at the designated points of the beam, after which the hardware is integrated according to the standard scheme. The optimum diameter of the anchor bolt is 10 mm, and the length is up to 200 mm. 3-4 fasteners will be enough for one segment.
Fixing technique with corner
Another common way to fix the lag is with the help of corners. Its advantages include a higher degree of reliability, since the lag is fastened to each other. At a basic level, parallel running logs are screwed onto a concrete base. But as an addition, a small-format beam is installed perpendicularly. In places of joints with beams and connecting corners are mounted . As a result, a double fixation system is implemented. It is also possible to fasten the logs to the concrete floor with corners without the use of intermediate bars. In this case, instead of direct anchor joints, the technique of lateral fixing of beams through the corner to the screed is used. Directly fastening is carried out with screws of a suitable size.
Features without drilling
Failure to intervene in the structure of the beams gives many advantages, increasing the durability of the entire structure. But how to achieve reliability of the lag position without the use of hardware? Fasteners will be used, but in relation to auxiliary elements. These are the same consumables in the form of small bars and plywood sheets, which just need to be fixed to the concrete as bearing contours of the substrate. On their platform will be fastened lag without drilling. Support strips are initially mounted on the concrete floor , after which the beams are laid. Rigid force fixation will be provided by means of groove joints. They can be provided both in the βlining-logsβ bundle, and by means of transverse auxiliary bars that will be guided along the entire length of the room. This design is complex and requires careful preliminary calculation.
Insulation Activities
The waterproofing layer can be laid before installing the lag, which will facilitate subsequent insulation measures. But experts still recommend starting such work after the installation of the beams is completed, since operations with fasteners can damage the laid material. As for the insulation, it is laid in the niches formed between the bars. If the optimized laying of the logs on the concrete floor was carried out only along parallel lines, then gaps should remain between the plates of mineral wool. They are additionally treated with silicone or other sealants, which in principle are combined with mineral wool. Pieces of insulation are cut in accordance with the parameters of empty niches, after which they are laid on a waterproofing pad. As a rule, the power fixation of the mineral wool is not performed - it is enough after coating to cover the material with another layer of hydro- or vapor barrier. In the future, a new layer of wooden coating from boards will be performed for the finishing flooring.
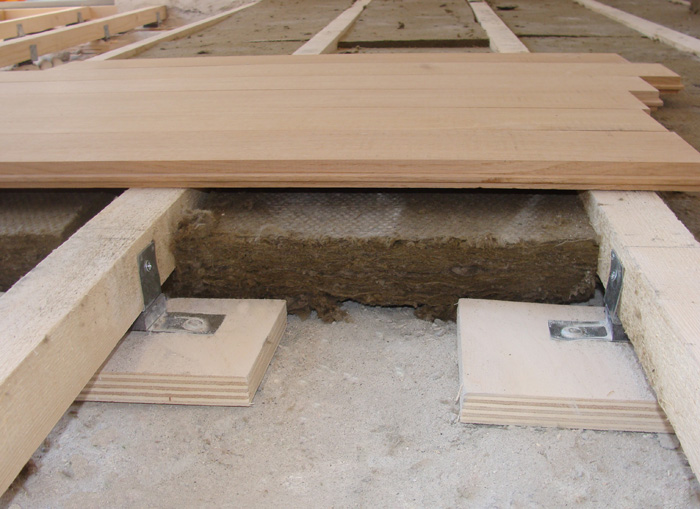
Adjustable Lag Installation
The most functional design that allows you to adjust the height of the floor to suit specific needs. For example, it will be possible to adjust the level of the substrate specifically for the thickness of the insulating material. But how to fix the logs to the concrete floor so that they are adjustable? The fixing system is quite simple and requires the use of only two elements - a rectangular mounting stand with mounting hardware and threaded rods. The supporting function will be performed by a system of supports securely fixed at the points of fixation of the beams using dowels. In the central part of each stand, a hairpin is mounted on which a beam is subsequently wound. This is done with a screw and nut, which will allow in the future to adjust the height of the floor. That is, initially you will need to make holes in the lags with a thickness corresponding to the diameter of the studs.
Conclusion
The bearing base for the floor on the logs is widely used in private housing construction because of the affordable price and ease of installation. After installation, the user will also receive a lot of opportunities for using the free space between the beams - here there can be ventilation channels, the same heat insulator, communication routes, etc. Conversely, among design flaws, fragility and fragility are usually noted. How to fasten the logs to the concrete floor with a high degree of reliability of the formed frame? Firstly, the bond strength of the concrete base and the beam battens must be guaranteed - both directly and by means of auxiliary elements. Secondly, the installation configuration itself should initially be calculated on the specific operating conditions of the house. The design should take into account the indicators of static and dynamic loads, which will more accurately select the mounting hardware.