Polished concrete floors are quite common and famous today. They can be seen in shopping centers, large halls and airports both in Russia and abroad. This flooring technology has proven to be economical and reliable; it is attracting more and more attention from flooring experts. At the moment, polished concrete has already turned into a separate direction in building materials, which has acquired a dynamic development. Let's look at its advantages, production technology, varieties, as well as refute a number of misconceptions that exist on the Russian construction market and lead to irrational monetary losses.
A bit of polished concrete history
Technology has come to our country from abroad. It has been practiced in the United States and other foreign countries for thirty-five years. Abroad, not a single object under construction can do without creating a floor from such material. Polished concrete is very popular here. Photos and other images of such coatings impress with their beauty.
The technology is used almost everywhere, regardless of the purpose of the future object: concrete (polished) is a suitable material for rooms with a large flow of people: shopping malls, warehouses, business centers. It also found application in country houses and apartments, where it is used as the final coating and is for domestic homeowners a new kind of flooring.
Material development in Russia
Currently, the technology for the production of polished concrete has already strengthened in our country. It is becoming more popular every day. Of course, in its development in the domestic market, it experienced some difficulties. One of the main reasons that has prevented the formation of polished concrete as an alternative to other flooring for a long time is its poor quality. For a sufficiently long time, it was not considered as the final material for the floor. Therefore, extensive requirements, such as strength, density and aesthetic appearance, were not imposed on its quality. This prevented the active promotion of such a material as concrete on the domestic market. Polished floor is now actively used. It is not a rough basis, the attitude towards its qualitative characteristics is gradually changing.
Required Properties
Concrete for flooring should first of all have a brand strength of at least B22.5, be well-vibrated and wiped, have any filler except limestone rocks. An important condition is the time elapsed since laying the base of concrete. It should be about twenty-eight days, no less.
Other conditions will primarily affect the speed of work:
- concrete is subjected to leveling operations to eliminate differences;
- such coatings can be restored to smooth chips or caverns;
- old concrete floors can be partially restored.
But such operations require additional financial costs and free time. Only observing the above properties can achieve high quality materials such as polished concrete. Floor, subject to all requirements, will differ from other coatings in durability and aesthetic attractiveness at low cost. Of course, alternative materials can be used: decorative polymer concrete that does not require a ten centimeter screed or reinforcement if there is no desire to do a lot of mechanical work. But then the final price tag of such sexes will increase.
Common mistakes
After receiving the concrete base, you need to proceed to the work of polishing and polishing it. And it is at this stage that the most mistakes are made. Let's look at the main ones.
- Mashing with "helicopters" to give concrete shine. Indeed, with this method of grouting, shine will be present, but will be short-lived and will disappear anyway during operation.
- Grinding with CO or GM machines. Using this tool, it is impossible to achieve the desired gloss. Many tests were carried out using technology, which showed that the surface is only matte. These grinders do not have sufficient rotation speed to produce long-lasting gloss, and they lack a planetary mechanism to achieve a high-quality surface.
- Polishing "grinder". Its use is not recommended, as the result will be poor due to the lack of sufficient weight on the tool, the possibility of observing the horizon and its very low productivity. "Grinder" is best used to perform auxiliary work around the perimeter (it is perfect for polishing hard-to-reach spots).
- Application of a varnish coating in order to obtain shine. This method was used in the nineties, covering ordinary stone floors with wax or varnish to give them a shiny surface. The use of varnish changes the whole essence of the material: polished concrete is incompatible with it. The technology for its preparation implies a natural shine achieved by proper machining. Moreover, the varnish coating is quickly erased during operation and all the aesthetic beauty deteriorates.
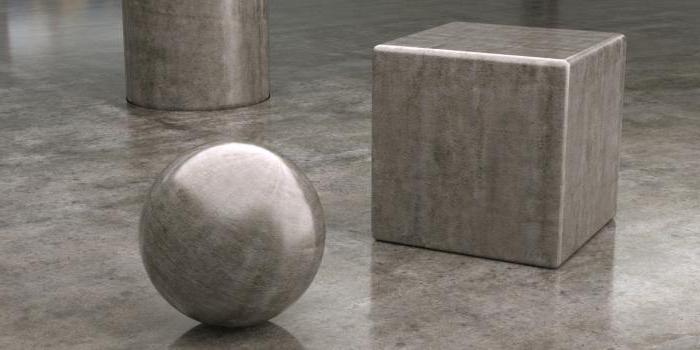
Consider the procedure for properly polishing concrete, as well as the tool used for this.
How to polish concrete?
First of all, it is necessary to carry out preparatory work to study the cultivated area for the absence of foreign bodies and reinforcement, measure the grade strength, analyze the presence of chips, cracks, various drops with their further correction.
To perform the work, it is recommended to involve specialists in the repair of premises. But to get polished concrete with your own hands is also possible with sufficient effort and care. What polishes concrete? It is best to use highly professional equipment - grinding machines with a planetary mechanism of operation.
They allow you to carry out all the preparatory work, as well as the main polishing of surfaces. All grinding usually occurs in dry mode, without the use of water. Therefore, you still need an industrial vacuum cleaner to remove fine dust. For good processing of the perimeter of the surface and hard to reach places it is better to use special edging machines or “grinder”.
In addition to mechanical work to obtain a high-quality concrete surface, it is necessary to use special chemical compositions that allow it to "dust off" and harden. One of the best types of such chemistry in the domestic market is Ultralit.
Polished Concrete Floor Forming Steps
First of all, to obtain an ideal concrete surface, it is necessary to level it and rough grinding. The purpose of such actions is to remove large irregularities. The second stage includes the restoration of potholes and caverns. Their result should be a uniform flat surface. Dust removal and hardening are also performed here.
The third stage is the final grinding or glossing. Micro scratches are removed. And finally, work is being done on the final polishing, which is also called fine grinding. Their goal is the process of caramelization of the surface, through which it acquires a steady shine.
Finally, it is possible to process concrete polished with various chemicals to give it additional properties, for example, anti-slip. It is important to understand that the main parameters in obtaining such concrete will always be the amount of consumable material, its mass and the speed of obtaining the final product. And the right combination of indicators will make a wonderful “mirror” out of the ordinary floor. However, polished and glossy concrete can be used not only for floors. It is also used during the creation of other surfaces.
Concrete worktop production. Preparatory stage.
A worktop is a necessary attribute in the arrangement of any apartment. And it can be made with your own hands from concrete, which then needs to be polished to obtain an aesthetic appeal. Consider the technology of manufacturing countertops with a marble coating.
For work, you just need a grinding machine with a planetary mechanism of work and nozzles for large, small grain and suede, as well as a screwdriver. First of all, you need to assemble a wooden formwork for the future countertop. It is very important to choose a stable and strong frame for it. To do this, you can use ordinary bars measuring fifty by fifty millimeters. To check the strength of the structure, resort to tricks - the frame must support your weight.
The main stage of work is the production and polishing of concrete
To obtain a concrete mortar, you need to stock up with a bucket of cement and water. We mix the components, then add to the mass a couple of buckets of sand and the same amount of rubble buckets. The prepared solution should be slowly poured into the frame to the desired height and left for ten days to solidify. The surface must be smoothed so that there are no bumps. After the required amount of time has passed, the formwork is carefully removed - work on the finishing and polishing of concrete begins. They have already been described previously, so we will not dwell on this in detail. It is worth noting only that polishing is first carried out by a nozzle for large grain, then fine-grained, and after suede with the addition of impregnation. After all the necessary work, you get an excellent tabletop made of polished concrete.
Finally
Finally, it should be noted what properties a high-quality polished concrete (surface) should have, and this should always be remembered:
- it should not dust;
- the surface is not a film material;
- She has an attractive appearance through a lasting shine;
- differs in durability and simplicity in operation;
- it is easily restored.
The domestic market has already adapted to the technology of producing concrete coatings. And now you can meet a sufficient number of masters in this field who are ready to offer their services.