Errors are the deviations of the measurement results from the real value of the quantity. A valid indicator can only be established by performing numerous measurements. In practice, this is not possible.
For the analysis of deviations, the value closest to the true value is considered the actual indicator of the measured value. It is obtained using high-precision measuring tools and methods. For the convenience of measurements, to ensure the possibility of eliminating deviations, different classification of errors are used . Consider the main groups.
Way of expression
If we carry out the classification of errors of measuring instruments on this basis, we can distinguish:
- Absolute deviations. They are expressed in units of the quantity that is being measured.
- Relative deviation. It is expressed by the ratio of the absolute error and the measurement result or the actual value of the quantity being measured.
- The given deviation. It represents the relative error expressed by the ratio of the absolute deviation of the measuring tool and the value taken as a constant indicator in the entire range of the corresponding measurement. His choice is based on GOST 8.009-84.
For many measuring instruments, an accuracy class is established. The given error is introduced because the relative value characterizes the deviation only at a specific point on the scale and depends on the parameter of the measured quantity.
Conditions and Sources
In the classification of errors according to these criteria, the main and additional deviations are distinguished.
The first are the errors of the measuring instruments that are under normal conditions of use. The main deviations are due to the imperfect conversion function, the imperfection of the properties of the devices. They reflect the difference between the actual function of the conversion of the device under normal conditions and the nominal (established in regulatory documents (technical conditions, standards, etc.)).
Additional errors arise when a value deviates from the normal value or in connection with going beyond the boundaries of the normalized region.
Normal conditions
The following normal parameters are defined in the regulatory documentation:
- Air temperature 20 ± 5 degrees.
- Relative humidity 65 ± 15%.
- Mains voltage 220 ± 4.4 V.
- Power frequency 50 ± 1 Hz.
- Lack of magnetic and electric fields.
- The horizontal position of the device with a deviation of ± 2 degrees.
Accuracy class
Permissible deviation limits can be expressed in relative, absolute or reduced error. So that you can choose the most suitable measuring tool, a comparison is made according to their generalized characteristic - accuracy class. As a rule, it is the limit of admissible basic and additional deviations.
The accuracy class allows us to understand the limits of the errors of the same type of measuring equipment. However, it cannot be considered as a direct indicator of the accuracy of the measurements performed by each such device. The fact is that other factors (conditions, method, etc.) also influence the classification of measurement errors. This circumstance must be taken into account when choosing a measuring tool, depending on the accuracy set for the experiment.
The value of the accuracy class is reflected in specifications, standards or other regulatory documents. The required parameter is selected from the standard series. For example, for electromechanical devices, the following are considered normative: 0.05, 0.1, 0.2, etc.
Knowing the value of the accuracy class of the measuring tool, you can find the permissible value of the absolute deviation for all parts of the measuring range. The indicator is usually applied directly to the scale of the device.
Nature of change
This feature is used in the classification of systematic errors . These deviations remain constant or change according to certain laws during measurements. In this classification there are also types of errors that are systematic in nature. These include: instrumental, subjective, methodological and other deviations.
If the systematic error approaches zero, this situation is called correctness.
In the classification of measurement errors in metrology , random deviations are also distinguished. Their occurrence cannot be predicted. Random errors cannot be counted; they cannot be excluded from the measurement process. Random errors have a significant impact on research results. Deviations can be reduced by multiple measurements followed by statistical processing of the results. In other words, the average indicator obtained during repeated manipulations will be closer to the real parameter than the one obtained in one measurement. When the random deviation is close to zero, they speak of the convergence of the indicators of the measuring device.
Another group of errors in the classification is misses. They are associated, as a rule, with errors made by the operator, or unaccounted for by external factors. Misses are usually excluded from the measurement results, are not taken into account when processing the received data.
Value dependent
Deviation may not depend on the measured parameter or be proportional to it. Accordingly, in the classification of errors in metrology , additive and multiplicative deviations are distinguished.
The latter are also called sensitivity errors. Additive deviations usually appear due to interference, vibrations in bearings, friction, and noise. The multiplicative error is associated with the imperfection of the adjustment of individual parts of the measuring tools. It, in turn, can be caused by various reasons, including the physical and moral deterioration of equipment.
Normalization of characteristics
It is carried out depending on which deviation is significant. If the additive error is significant, the limit is normalized in the form of a given deviation; if it is multiplicative, the formula for the relative magnitude of the change is used.
This is such a standardization method in which both indicators are comparable, that is, the boundary of the permissible main difference is expressed in the two-term formula. Therefore, an indicator of the accuracy class also consists of 2 numbers c and d in percent, separated by a slash. For example, 0.2 / 0.01. The first number reflects the relative error under normal conditions. The second indicator characterizes its increase with increasing value of X, i.e., reflects the influence of additive error.
Dynamics of changes in the measured indicator
In practice, a classification of errors is used , reflecting the nature of the changes in the quantity being measured. It involves the separation of deviations:
- On static. Such errors arise when measuring a slowly varying or not changing variable.
- Dynamic. They appear when measuring physical quantities that change rapidly over time.
Dynamic deviation is due to the inertia of the device.
Features of deviation assessment
Modern approaches to the analysis and classification of errors are based on principles that ensure compliance with the unity of measurement requirements.
To implement the goals of assessment and research, the deviation is described using the model (random, instrumental, methodical, etc.). It defines the characteristics that can be used to quantify the properties of the error. During the processing of information, it is necessary to find estimates of such characteristics.
The model is selected taking into account data on its sources, including those obtained during the experiment. Models are divided into non-deterministic (random) and deterministic. The latter, respectively, are suitable for systematic deviations.
The quantity that implements the probability distribution function acts as a general model for a random error. The deviation characteristics in this case are divided into interval and point. When describing the error of measurement results, interval parameters are usually used. This means that the limits within which the deviation can be located are defined as corresponding to a certain probability. In such a situation, the boundaries are called confidence, and the probability, respectively, is confidence.
The point characteristics are used in cases where there is no need or opportunity to assess the confidence limits of the deviation.
Assessment principles
When choosing deviation estimates, the following provisions are used:
- The individual parameters and properties of the selected model are characterized. This is because deviation models have a complex structure. Many parameters are used to describe them. Their definition is often very difficult, and in some situations completely impossible. In addition, in many cases in the full description of the model there is redundant information, despite the fact that knowledge of individual characteristics will be quite enough to implement the tasks and achieve the goals of the experiment.
- Deviation estimates are approximate. The accuracy of the characteristics is consistent with the purpose of the measurements. This is due to the fact that the error characterizes only the zone of uncertainty of the result and its extreme accuracy is not needed.
- Deviation is preferable to exaggerate rather than downplay. In the first case, the quality of the measurement will decrease, in the second, a complete depreciation of the results is likely.
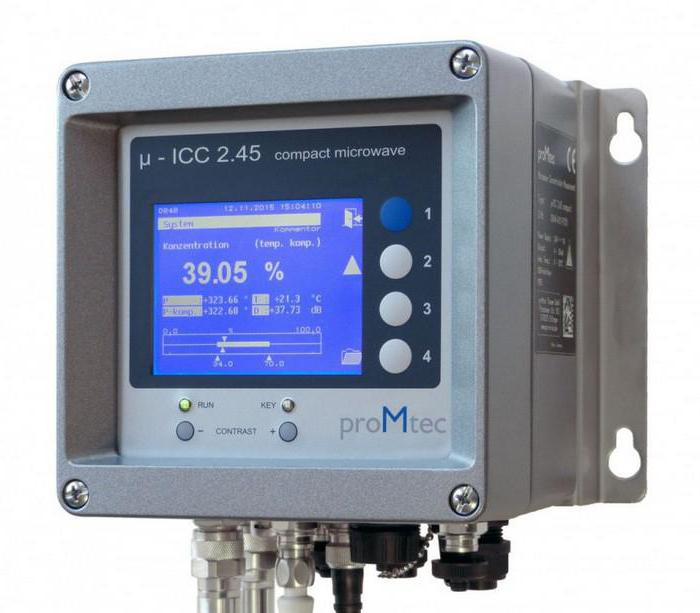
Errors can be estimated before or after measurement. In the first case, it is called a priori, in the second - a posteriori.