Preparing the base for the subsequent laying of decorative flooring in the house is a responsible task, the durability of the coating depends on the quality of its execution. The most reliable way to create a stable draft platform is a screed. Traditionally, it is performed on a sand-cement basis, but today a segment of self-leveling floors with polymer inclusions is developing more and more actively. Such mixtures favorably differ in technical and operational qualities and greatly simplify the installation process.
Technology Overview
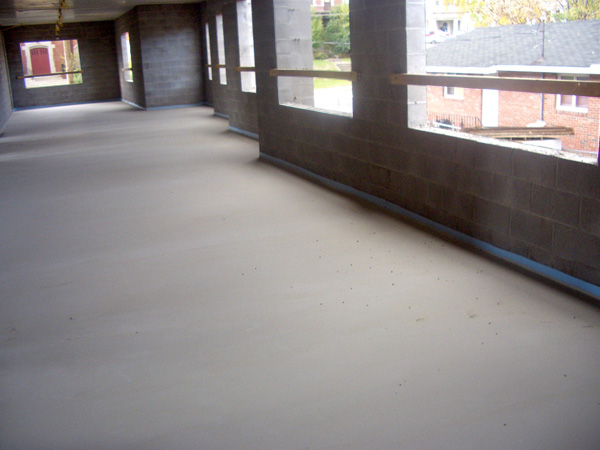
A feature of the method of the device of the bulk screed is the formation of a smooth, durable and (in some cases) aesthetically attractive surface. With low costs, you can get a base suitable for finishing flooring with a minimum number of defects. The cement-polymer composition of the mortar for the floor is also resistant to dusting, mechanical abrasion and small chips. These operational properties determine the prevalence of the method in relation to public and commercial premises, where it is necessary to provide a large area with a flat floor base in a short time. It is important to separate the final self-leveling mixes for the floor and quick-hardening mortars for screed. Both compositions belong to bulk floors, but differ in purpose. Thin, leveling mixtures form a ready-to-use coating, representing a decorative value. Materials for quick-hardening screeds form strong surfaces for subsequent application of finishing coatings on them - parquet, laminate, carpet, etc.
Characteristics of mixtures
On the market, the initial fillers for bulk floors are represented by dry mixes in bags and sacks with an average weight of 20-25 kg. Depending on the type of components, the grain size can be 0.6-0.8 mm. Accordingly, the fine fraction is suitable for finishing coatings, and the coarse fraction is suitable for roughing. Adhesive or strength indicators are expressed in the permissible load under pressure - an average of 1.5-2 MPa. The higher this value, the more durable the coating base. High-strength mixtures are suitable for commercial use, and a high wear resistance class is not required for a home. Also take into account the pour time. Standard self-leveling floors gain optimum strength in 3-4 hours. Thin topcoats, the polymerization of which takes place in just 30 minutes, demonstrate record-breaking performance. In the case of industrial mixtures, this time can reach up to 24 hours. As for the thickness, it is from 2 to 10 cm.
Mixture filling tool
In the work you will need tools and devices that are usually used in plastering events. At a minimum, you should arm yourself with a spatula, a container for mixing the mortar and a mixer (it is advisable to use an electric model). Experienced craftsmen recommend using a needle roller at the leveling stage of the mixture poured onto the platform. Even the most accurate filling of the floor with a self-leveling mixture will not exclude the presence of air bubbles in the structure of the future layer, but the pin design of the tool will reduce their number. Additional consumables can be represented by corners, formwork elements, beacons and other mounting accessories, which will technically correctly organize the formation of a liquid floor at the pouring stage.
Surface preparation for pouring
Although one of the tasks of a self-leveling coating is to hide defects in the rough surface, this does not mean that you can leave deep holes, cracks and chips. In the future, these defects will make themselves felt, deforming and newly laid screed. Therefore, at the preparation stage, all deep flaws should be repaired and, if necessary, the primer of problem areas should be completed. The target area is also marked. In order for the self-leveling floors to fall strictly according to the designated area, a formwork is created from wooden boards and panels. It can be formed with small rails or a metal profile - the main thing is that it matches the planned thickness of the coating in height.
Material consumption
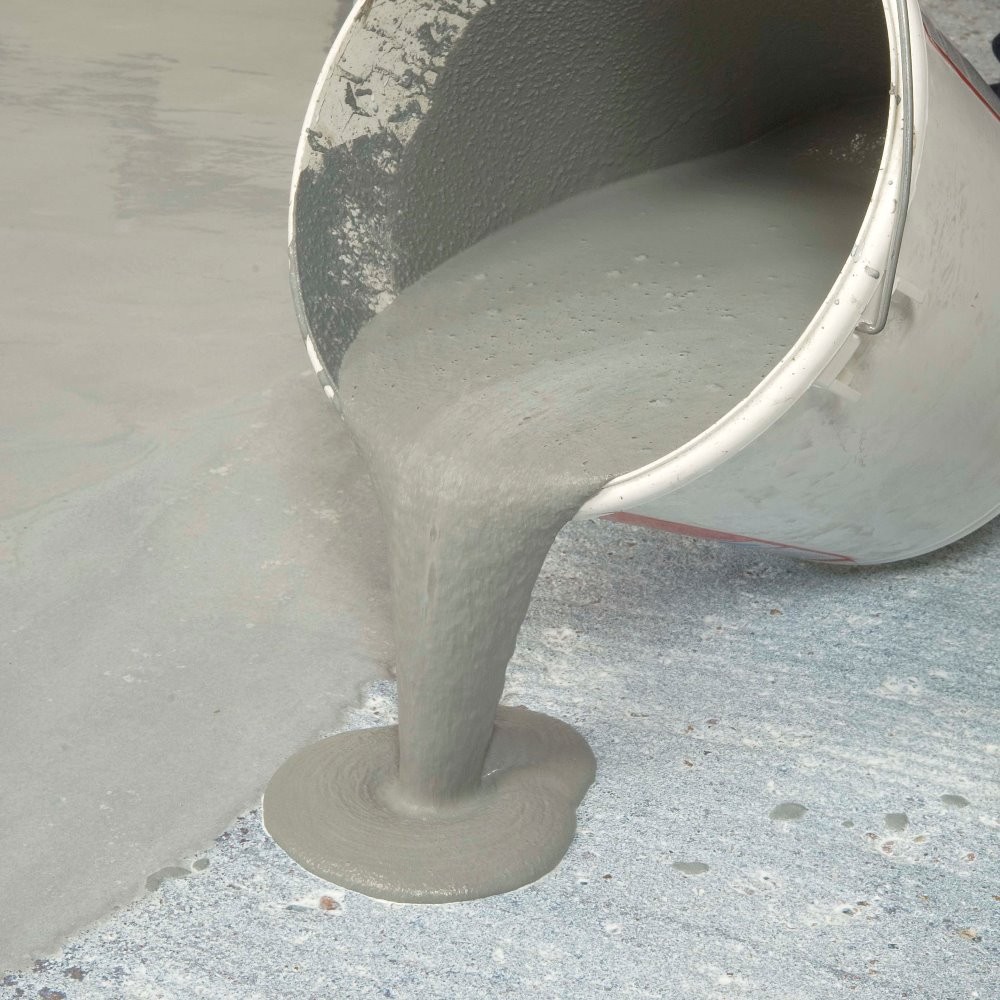
Manufacturers themselves indicate that on average 1.5 kg of a mixture should be prepared per 1 m 2 , provided that the thickness is 1 mm. As the height of the coating increases, consumption will increase in the same proportions. In the case of coarse equalizers, from which they form a quick-hardening solid base for decorative surfaces, the volume can increase. On the same 1 m 2 you need to stock already 2-2.5 kg. Much will depend on the quality of calculating the optimal layer thickness. The height is determined not only by the type of coating, but also by the requirements for finishing a particular area on which a self-leveling floor is laid. Consumption can be saved in the normative indicators of 20 kg per 10 m 2 in the conditions of height differences of up to 80 mm, if in advance deep-hole excavation is completed. In this case, the need for excessive volume will disappear by itself. In addition, you can save on the mixture by adding sand. This method is appropriate if it is planned to lay the material over a large area.
Floor filling
Contrary to the widespread belief that at the first stage the prepared solution is simply poured into the center of the target site, initially a small fraction of the mass should be scattered by hand and smeared. This is necessary so that the primary layer provides sufficient adhesion to cope with the rough surface. The latter, by the way, will not be amiss to pre-degrease and clean. Then the main volume of the mixture is applied once to a plot of 1.5 m 2 . From this point, in the future, you need to smooth the self-leveling floor with your own hands, using a spatula and a needle roller. But before that you should wait 10-15 minutes until the poured solution disperses over the entire limited surface.
Floor leveling
This is the most critical stage of work activities, since the strength characteristics of the coating structure and the preservation of its optimal shape will depend on it. Sometimes after arbitrary smoothing, differences in heights remain - they need to be fought with a spatula, maintaining the accuracy of mass redistribution. As for the needle roller, they should go through the entire flooded area, releasing air bubbles at different depths. As a result of this study, self-leveling floors become denser and more uniform. In some cases, auxiliary modifiers with plasticizers are added at this stage. They can improve the individual performance of the coating, including fire resistance, adhesion, monolithicity, etc.
General workflow guidelines
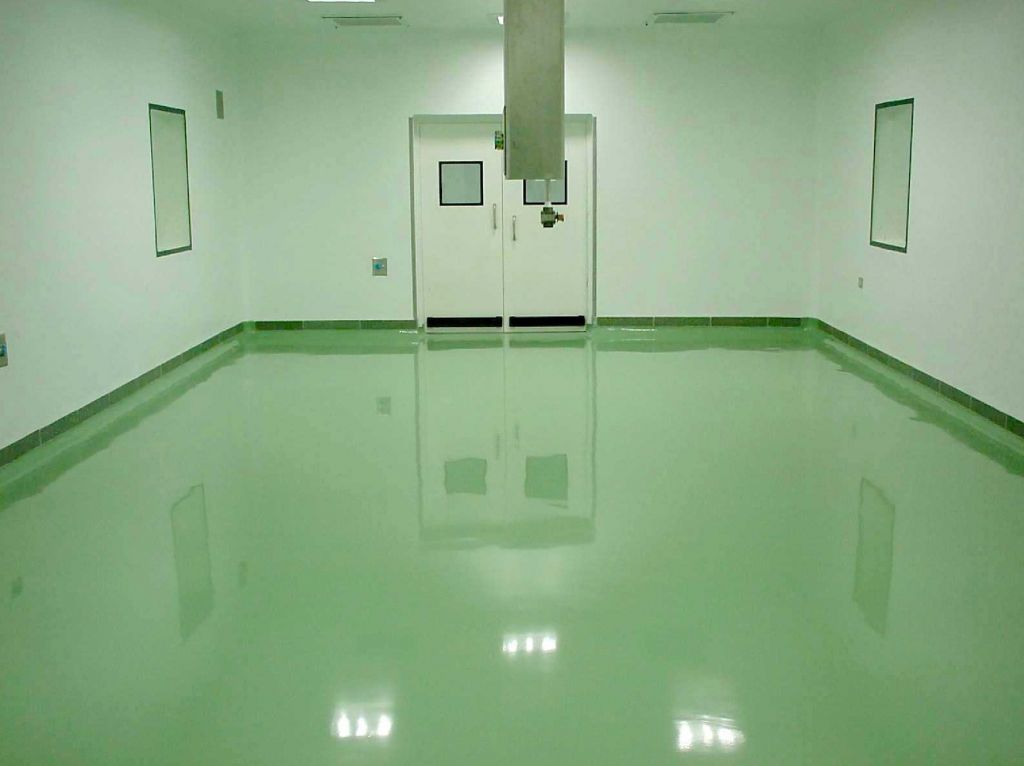
The quality of the new coating will depend on how correctly the rough floor has been processed. Particular attention is also paid to coating conditions. If the room is characterized by high humidity, then the corresponding insulator is laid on the laying surface. Membrane hydro-vapor isolators, for example, do not increase the height level of the coating, but reliably protect the polymer composition from the negative effects of moisture. In the question of how to fill a self-leveling floor without errors at the stage of primary distribution, it is important to consider the time factor. As already noted, the curing time for some compositions can be up to 30 minutes. Therefore, you need to act promptly, so that there is a margin and high-quality comprehensive alignment with passes with a needle roller. You also need to calculate the possibility of preliminary distribution of the mixture on the rough surface before pouring. The lower and main layers should not have different periods of solidification, otherwise this difference will adversely affect the strength properties of the coating structure.
Conclusion
An important place in the design of flooring with building mortar for screed is also the origin of the material. This segment on the market is represented by many well-known manufacturers. For example, preference should be given to Knauf and Ceresit. Although a self-leveling bulk floor on such a basis will cost more (300-350 rubles per 20 kg), the service life will also be significantly higher. Budget series are represented by Axton, Volma and Bolars. In this case, the cost of a small bag of 20 kg will be 200-250 rubles. And again, do not forget about additional modifiers that will improve the technical and physical qualities of the coating. Supplements for various purposes are produced under the same brands.