From the article you will learn what welding machines are. It is quite simple to make them with your own hands, if you have elementary knowledge in electrical engineering and the necessary tools. As a basis for a welding machine, either a ready-made transformer or a home-made one can be taken.
Of course, such designs consume more power, therefore, a strong voltage drop will be observed in the network. This may affect the functioning of household electrical appliances. It is for this reason that structures based on semiconductor elements are much more efficient. Simply put, these are invertor welding machines.
The simplest welding machine
So, the first thing to consider is the simplest designs that anyone can repeat. Of course, these are the devices based on transformers. The design discussed below allows you to work on voltages of 220 and 380 volts. The maximum electrode diameter used in welding is 4 millimeters. The thickness of the welded metal elements ranges from 1 to 20 millimeters. You will now learn fully about how to make a welding machine with your own hands . And you can move from simple to complex.
Despite such excellent characteristics, the manufacture of the welding machine is made from readily available materials. You will need a three-phase voltage step-down transformer for assembly. Moreover, its power should be about 2 kilowatts. It is also worth noting that you will not need all the windings. Therefore, in the event that one of them fails, there will be no problems with further construction.
Transformer alteration
The bottom line is that you need to make changes only in the secondary winding. To facilitate the task, the article below shows a diagram of the welding machine, its connection to the network is also described.
So, you do not need to touch the primary winding, it has all the characteristics necessary for working from an alternating current network of 220 Volts. It is not necessary to disassemble the core, it is enough to disassemble the secondary winding directly on it, and instead of it wind a new one.
There are several windings on the transformer you must choose. Three primary, as many secondary. But there are also middle windings. There are also three of them. It is instead of the middle one that it is necessary to wind the same wire that was used to make the primary one. Moreover, it is necessary to make bends from every thirty turn. About 300 turns in total, each winding should have. Thanks to the correct winding of the wire, you can increase the power of the welding machine.
A secondary winding is wound on both extreme coils. It is difficult to indicate the exact number of turns, since the more there are, the better. The wire is used with a cross section of 6-8 square millimeters. Together with it, a thin wire is wound simultaneously. As a power cable, you need to use stranded in reliable insulation. This is how do-it-yourself welding machines are made.
If we analyze all the structures made by this technology, it turns out that the approximate amount of wire is about 25 meters. If there is no wire with a large cross section, you can use a cable with an area of ββ3-4 square millimeters. But in this case, it must be doubled when winding.
Transformer connection
The design has a simple welding machine. A semiautomatic device can be made on its basis, if one more winding is made to power the electric drive for supplying electrodes. Please note that there will be a very large current at the transformer output. Therefore, all switching connectors must be made as durable as possible.
To make the terminals for connecting to the terminals of the secondary winding, you need a copper tube. It should have a diameter of 10 millimeters, and a length of 3-4 cm. From one end it needs to be riveted. The result should be a plate in which you need to make a hole. Its diameter should be about one centimeter. From the other end, wires are inserted. Regardless of whether the welding machine is direct current or alternating, switching is made as rigid and reliable as possible.

It is advisable to perfectly clean them, if necessary, treat them in acid and neutralize it. To improve contact, the second edge of the tube should be slightly flattened with a hammer. The conclusions of the primary winding are best attached to the PCB. Its thickness should be about three millimeters, as much as possible. It is rigidly attached to the transformer. In addition, in this board you need to make 10 holes, each with a diameter of about 6 millimeters. Look at the diagram of the welding machine, how it is connected to the 220 and 380 Volt network.
Screws, nuts and washers must be installed in them. The terminals of all primary windings are connected to them. In the event that it is required that the welding work from a 220 V household network, the extreme windings of the transformer are connected in parallel. In series with them, the middle winding is turned on. Welding will work ideally when powered by 380 volts.
To connect the primary windings to the mains, you need to use a different circuit. Both extreme windings are connected in series. Only after this the middle winding is switched on sequentially with them. The reason for this lies in the following: the middle winding is an additional inductive resistance, with its help there is a decrease in voltage and current in the secondary circuit. Thanks to this, welding machines made in accordance with the given technology work in normal mode.
Electrode holder manufacturing
Of course, an integral part of any welding machine is the electrode holder. There is no need to buy ready-made if you can make it from improvised materials. You need a three-quarter pipe, its total length should be about 25 centimeters. At both ends, small recesses must be made, approximately 1/2 diameter. A welding machine will work normally with such a holder. For plastic structural elements, a separate requirement is that they should be located as far as possible from the transformer and holder.
You need to do them in three to four centimeters from the edge. Then take a piece of steel wire, the diameter of which is 6 millimeters, weld it to the pipe opposite the larger recess. On the other hand, you need to drill a hole, attach a wire to it that will connect to the secondary winding.
Network connection
It is worth noting that you need to connect the welding machine in accordance with all the rules. Firstly, you need to use a switch, with which you can easily disconnect the device from the network. Please note that welding machines made by oneself should not be inferior in safety to analogues produced by the industry. Secondly, the cross-section of wires for connecting to the network should be at least one and a half square millimeters. Primary current consumption is a maximum of 25 amperes. In this case, in the secondary circuit, the current can be changed in the range of 60..120 amperes. Please note that this design is relatively simple, therefore it is suitable only for domestic use.
Try to give a short break from time to time, regardless of whether the welding machine is semi-automatic or manual. Used a dozen electrodes - turn off the welding, let it cool down a bit. But this is only if electrodes with a diameter of more than 3 millimeters are used. If you use smaller ones, for example 2 millimeters, then the temperature of the transformer windings does not rise more than 80 degrees. Therefore, you can work without turning off the welding machine. During operation, be sure to observe safety precautions. Familiarize yourself with the fire safety rules for the operation of the welding machine. Do not be lazy and read about the rules of electrical safety.
Spot welding machine
A point-type welding machine will also be useful. The designs of such devices are no less simple than the previous ones. True, the output current is very large. But it is possible to perform contact welding of metals up to three millimeters thick. Most designs do not have an output current adjustment. But you can do it if you wish. True, all home-made is complicated. There is no need to control the output current, since it is possible to control the welding process visually. Of course, welding invertors will be much more efficient. But the point can do what does not allow any other design.
For manufacturing, you will need a transformer with a capacity of about 1 kilowatt. The primary winding remains unchanged. It will only be necessary to redo the secondary. And if a transformer from a household microwave is used, then you need to knock out the secondary winding, instead of it, wind several turns of a large cross-section wire. If possible, it is better to use a copper bus. The output should be about five volts, but this will be enough for the full operation of the device.
Electrode holder design
Here it is slightly different from the one discussed above. For manufacturing you will need small duralumin blanks. Suitable rods with a diameter of 3 centimeters. The bottom should be fixed, completely isolated from the contacts. As an insulating material, you can use textolite washers, as well as varnish. Any, even the simplest spot welding machine needs a reliable electrode holder, so pay maximum attention to its design.
The electrodes are made of copper, their diameter is 10-12 millimeters. They are firmly fixed in the holder using rectangular brass inserts. The initial position of the holder electrode - its half is divorced. To give elasticity, springs can be used. Ideal from old cots.
Resistance welding work
It is necessary to connect such welding to the electric network using a circuit breaker. It should have a rated current of 20 amperes. Please note that at the entrance (where you have a counter), the machine must be either the same in parameters or large. To turn on the transformer, a simple magnetic starter is used. The operation of a contact type welding machine is slightly different from that which was discussed above. And you will now recognize these features.
To turn on the magnetic starter, you must provide a special pedal that you will press with your foot to generate current in the secondary circuit. Please note that contact welding is switched on and off only if the electrodes are completely flattened. If you neglect this rule, then a lot of sparks will appear, as a result, this will lead to burning of the electrodes, their failure. Try to pay attention to the temperature of the welding machine as often as possible. Take small breaks from time to time. Do not overheat the unit.
Inverter welding machine
It is the most modern, but more difficult to design. It uses a pulse transformer and high power semiconductor transistors. Perhaps these are the most expensive and scarce parts. First of all, the power supply is made. It is pulsed, so it is necessary to manufacture a special transformer. And now in more detail about what such a welding machine consists of. Characteristics of its components see below.
Of course, the transformer used in the inverter is much smaller in size than the ones discussed above. You will also need to make a throttle. So, you should get a ferrite core, a frame for the manufacture of a transformer, copper tires, special brackets to fix two halves of the ferrite core, electrical tape. The latter must be selected based on the data of its thermal stability. Follow these tips when making inverter welding machines.
Winding transformer
A transformer is wound over the entire width of the frame. Only under such a condition will he be able to withstand any voltage drop. For winding, either a copper bus or wires assembled in a bundle are used. Please note that aluminum wire must not be used! He can not withstand such a high density of electric current, which is available in the inverter. Such a welding machine for the garden can help you out, and its weight is extremely small. The turns are wound as tightly as possible. The secondary winding is two wires with a thickness of the order of two millimeters twisted together.
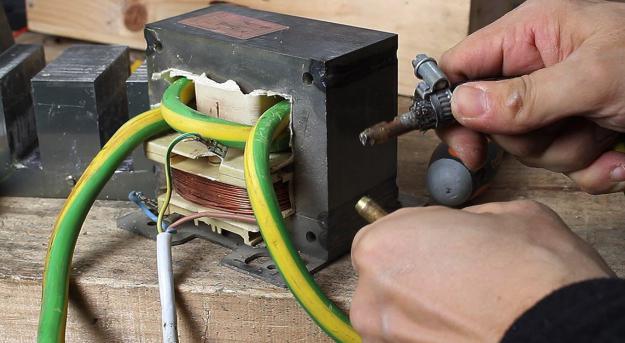
They should be as isolated as possible from each other. If you have large stocks of line transformers from old televisions, you can use them in the design. 5 pieces are required, and one common magnetic circuit needs to be made of them. For the device to work with maximum efficiency, you need to pay attention to every detail. In particular, the thickness of the wire of the output winding of the transformer affects its continuity.
Inverter design
To make a welding machine 200, you need to pay maximum attention to all the little things. In particular, power transistors must be mounted on a radiator. Moreover, the use of thermal grease is welcomed to transfer heat from the transistor to the radiator. And it is recommended to change it from time to time, since it has the property of drying out. In this case, heat transfer is deteriorating, it is likely that semiconductors will fail. In addition, you need to do forced cooling. For this purpose, exhaust coolers are used. The diodes used to rectify the alternating current must be mounted on an aluminum plate. Its thickness should be 6 millimeters.
The connection of the terminals is carried out using bare wire. Its cross section should be 4 millimeters. Pay attention to the maximum distance between the connection wires. They should not touch each other, no matter what impact the body of the welding machine experiences. The choke must be fixed to the base of the welding machine using a metal plate.
Moreover, the latter should completely repeat the shape of the throttle itself. To reduce vibration, it is necessary to install a rubber seal between the body and the throttle. Power wires inside the device are routed in different directions. Otherwise, there is a possibility that a short circuit will occur. It is necessary to install the fan so that it blows all the radiators at a time. Otherwise, if you canβt use one fan, you will have to install several.
But it is better to fully calculate the installation location of all elements of the system in advance. Please note that the secondary winding must be cooled as efficiently as possible. As you can see, not only radiators need efficient airflow. On this basis, an argon welding machine can be made without cost. But its design will require the use of other materials.
Conclusion
Now you know how to make several types of welding machines. If you have skills in the design of electronic equipment, then it is better, of course, to dwell on an inverter welding machine. You will spend time, but at the exit you will get a wonderful device that is not inferior even to expensive Japanese counterparts. Moreover, its manufacture will cost a mere penny.
But if there is a need to make a welding machine, as they say, in a hurry, it will be easier to connect two transformers from microwave ovens with modified secondary windings. Subsequently, the entire unit can be improved by adding to it an electric drive for feeding electrodes. It is also possible to install a cylinder filled with carbon dioxide in order to weld metals in its environment.