Currently, zinc dust (zinc powder) is widely used in various fields of industrial activity, as well as in pyrotechnics to give fireworks and firecrackers a blue hue. Let us consider in more detail for what purposes this substance is used, its composition and useful properties.
Areas of use
Widespread use of zinc powder has received:
- in the chemical industry in the production of polymers, as well as as a filler for lubricants;
- in hydroelectrometallurgy and powder metallurgy;
- in the extraction of gold and silver (for the displacement of precious metals from cyanide solutions);
- in hydrogen energy;
- in the production of chemical current sources;
- in the pharmaceutical industry;
- in wastewater treatment;
- for the synthesis of organic compounds.
Zinc powder is widely used for the manufacture of various anti-corrosion compounds that are used in various fields of engineering. In addition, it is part of paints and primers, with the help of which bridges, ships and various structures protect against the aggressive conditions in which they are operated.
Types and composition
Currently, the industry produces various grades and modifications of zinc powder, which vary both in chemical composition and in size, particle shape. There are powder particles of spherical, elliptical shape, as well as in the form of flakes.
According to GOST, zinc powder is classified as follows:
- class A includes grades of powder with a fine-grained structure, made by rectification;
- Class B combines the coarse product obtained by spraying.
The composition of zinc powders includes from ninety-five to ninety-eight percent of zinc, as well as a small amount of impurities in the form of some other metals.
Storage Conditions and Precautions
Zinc powder drums should be stored in closed storage rooms that do not contain aggressive chemicals.
Moisture should not be allowed to enter the powder container during packaging, transportation and storage, since zinc oxide generates hydrogen, slowly reacting with moisture from the environment.
When working with zinc powder, smoking and using open flames are prohibited. In order to ensure safe conditions, it is necessary to clean the premises at the places of sifting and packing powder, at least once a month, and to wall the walls and equipment.
The use of zinc powder in the manufacture of paints
The property of zinc to resist corrosive effects has long been used by manufacturers of paints designed to coat metal surfaces. Such coatings using zinc dust and flakes increase the resistance of metal products to mechanical stress and protect them from corrosion.
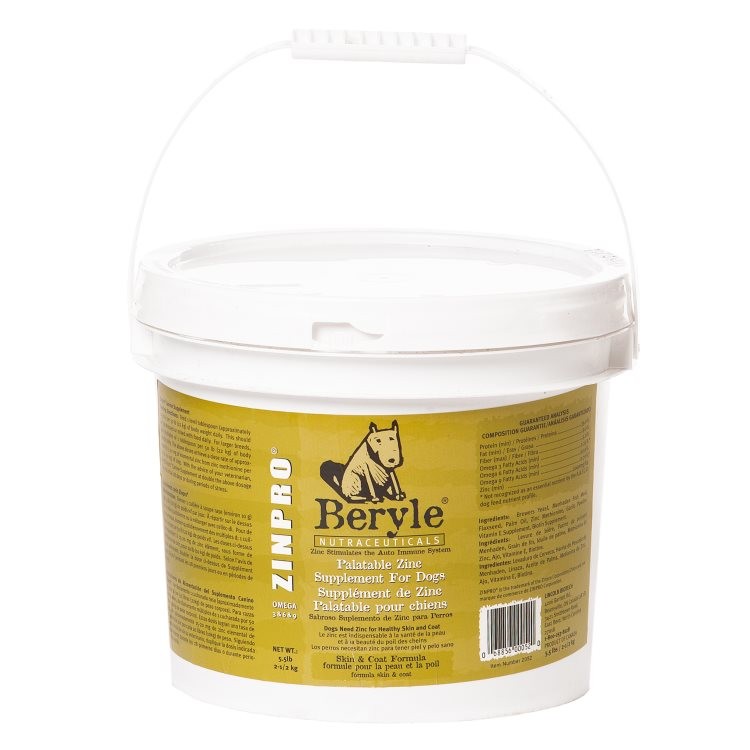
A large amount of zinc filler in the coating composition increases the protective properties of the paint, but reduces the strength of the coating, which eventually begins to crack and peel off. To solve this problem, it was necessary to reduce the filler content to 25 g of zinc powder per hundred grams of the composition, as well as change the structure of the filler and add auxiliary substances to the paint - various organic resins and water glass. To improve the beneficial properties of such coatings, various additives in the form of hardeners, aqueous phosphates, inhibitors, silicates and chromic acid salts can be added. In fact, zinc paint is a special type of primer, since it is used for the primary coating of metal structures and products.
Properties of Zinc Paint
The paint, which contains filler in the form of zinc powder, is resistant to moisture, as well as petroleum products and organic solvents.
Zinc paint can be applied directly to rust, without prior metal treatment. This paint has high abrasion resistance and increased resistance to mechanical stress.
The use of zinc paint allows you to protect metal structures from the effects of adverse atmospheric factors for up to twenty-five years.
Application of zinc paint
Before applying zinc paint, the surface should be prepared, that is, rid it of loose rust and various contaminants. To do this, it is cleaned with white spirit or solvent.
Immediately before use, the paint should be thoroughly mixed until a uniform consistency of medium density. If it becomes thick, you can dilute it with toluene. The optimum temperature for staining is in the range of five to forty degrees above zero.
To apply the composition to the surface, use the fly or middle brush. You can also use the roller. To paint large surfaces, you can use a spray gun. When the first layer is dry, after an hour and a half, a second coating layer is applied. A week after painting, the product is completely ready for use in the usual mode.