The scope of the adhesive is diverse, it is used in industrial production, construction, repair and modeling. Glue joints are used in assembly processes, at the stage of installation of structures and materials. Most often, glue is used in the paper industry and in wood processing.
In its history, adhesives and mixtures have been modified. Thanks to modern technology, adhesives based on synthetic resins have appeared that are able to glue any materials and surfaces. Synthetic adhesives have increased elasticity, waterproof and seal joints, as well as ensure their long life. An example of the effective use of synthetic adhesives is the installation of PVC pipes for adhesive bonding or the use of synthetic adhesive mixtures for the repair and commissioning of machines (with the help of adhesive, the landing surfaces of beds and bodies are adjusted).
The main advantage of the adhesive is the high reliability of the connection of various surfaces and parts, achieved without undue impact on structural elements (drilling, screed, welding).
What are glue and adhesive joints?
Adhesive is a mixture or multicomponent composition used to connect various structural elements and materials. Adhesive bonding is one-piece, strong bond is formed by adhesion of surfaces to the adhesive layer. Adhesives vary in composition. The compositions are composed of organic and inorganic polymers. The basis of the adhesive composition is classified:
- hot cured polymers;
- cold cured polymers;
- heat resistant polymers;
- thermoset and thermoplastic polymers;
- polymers used in the usual temperature range.
The development of production technologies and the chemistry of polymers made it possible to create compositions that provide durable adhesive bonding of materials whose surfaces had not previously yielded to a strong bond: metal, ceramic or glass. In addition to the polymer base, the composition of the adhesive includes various additives to give the adhesive layer target properties and characteristics (heat resistance, moisture resistance, strength, ductility, etc.). Targeted additives can be: hardeners, solvents, dyes, plasticizers, as well as other fillers.
Qualitative characteristics and properties of adhesive joints depend on the choice of glue and strict adherence to gluing technology.
Glue: conditions determining the choice
In the choice of glue, the main role is played by the properties and characteristics of the materials intended for gluing, working conditions (humidity, temperature), the estimated service life of the adhesive joint and the load on it. When choosing glue, attention should be paid to cost, sanitary and hygienic parameters, and combustibility. A feature of all adhesive joints is the deterioration of the adhesion characteristics over time, therefore, adhesive bonds are destroyed during the entire period of operation.
The decrease in the strength and elasticity of the adhesive layer is due to the effects of temperature fluctuations, humidity and other conditions. So, before gluing a building structure, technological product or PVC pipe, the adhesive joint is intensively tested for strength under the influence of predicted operating conditions.
General technology for bonding surfaces
Bonding technology involves the preparation of surfaces, mixing the components of the adhesive composition (if required), applying glue with a thin layer on the surface and waiting until a rigid bond is obtained. One of the most important steps is the preparation of surfaces before gluing, which ensures optimal adhesion. When applying glue to the surface, attention should be paid to the adequacy of the film thickness. The assembly of adhesive joints ends with the curing of the adhesive composition, which should take place in the optimal technological mode.
At the preparatory stage of surface treatment, any contaminants are removed, using special solutions, the surfaces are degreased and roughened. The best option for surface preparation is one in which cohesive fracture (fracture along the knitting layer) of adhesive joints is noticeable. For processing glued surfaces using both chemical and mechanical methods to increase the strength of the connection.
The quality of the adhesive joint depends on the method of applying the adhesive layer to the surface. The glue should be evenly distributed over the surface, the film thickness should be uniform and be in the range from 0.1 to 0.2 mm. The method of applying glue depends on the viscosity of the composition.
As an example, we will consider the features of the choice of glue and the technology of gluing the water supply system consisting of PVC pipes with glue.
The choice of glue for PVC pipes
A pipe for an adhesive joint made of polyvinyl chloride is used in utilities for laying water supply systems, and is used in heating systems and sewers. There are several technologies for joining PVC pipes and fittings. Diffusion welding is most commonly used , however, the technology of gluing pipes with fittings is very popular, which also achieves high adhesive strength.
The adhesive compositions used for gluing PVC pipes contain the main component polyvinyl chloride, which is diluted with a solvent to obtain the desired consistency. The adhesive composition may additionally contain various additives and fillers that increase the waterproofing and hermetic abilities of the adhesive. The physical bonding process consists in applying the adhesive to the surface of the products, then they are reduced, over time, the solvent evaporates, and a strong adhesive bond is formed. The use of polyvinyl chloride in the adhesive provides reliable adhesion of surfaces at the molecular level.
To choose the optimal adhesive composition for PVC pipes, the following should be considered:
- clearly know for what purpose glue is acquired;
- it is important to familiarize yourself with the technology of preparing the adhesive composition, adhesives based on polyvinyl chloride can consist of two components, directly affect the strength of the adhesive joint;
- setting speed, which for most compositions does not exceed 1-2 minutes (depending on humidity and air temperature);
- adhesives for PVC pipes have a different color;
- the degree of viscosity of the ready-to-use composition.
The technology of mounting PVC pipes in an adhesive way
The adhesive solution is thoroughly mixed. If the main components need to be connected independently, it is important to observe the correct proportions. The pipe for the adhesive joint is prepared at the bonding site, the surface is cleaned and degreased. Installation begins with the application of adhesive to the surfaces to be bonded. The glue is applied with a brush with a uniform distribution on the surface, discontinuity of the film and omissions of individual sections are not allowed. Upon completion of the process of wetting the surfaces with adhesive solution, the pipe section is combined with the fitting.
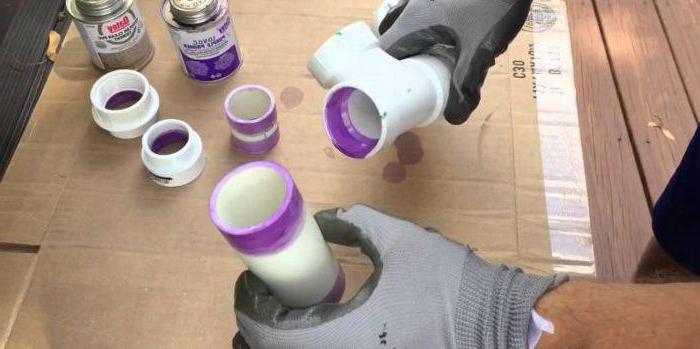
After combining the fitting and the pipe, the adhesive joint must be rigidly fixed for 15-20 seconds, after which the initial adhesive coupling is formed and the adhesive thickens. It is important to make sure that the structure is locked in the correct position even before gluing, since turning or other impact is not allowed. The adhesive should remain at rest for 15 minutes until the solvent has completely evaporated.
Sequential bonding of all sections of the water supply system, consisting of fittings and PVC pipes, is performed. The adhesive joint after 24 hours from the moment of completion of the installation is checked for tightness and strength under the load of the water pressure.
Adhesive strength
Requirements regarding the reliability of adhesive joints are made depending on the characteristics of the materials to be bonded and the operating conditions of the joint. However, there are a number of universal parameters that any connection must match.
Basic reliability characteristics for all types of adhesive joints:
- the equal strength of the material to be bonded with an adhesive joint;
- solidity of the adhesive joint with elements to be glued;
- the stability of adhesive bonds and the quality of surface treatment determine the indicators of durability and reliability.
The main sign of the reliability of the adhesive joint is to ensure bond strength equal to or greater than the strength of the monolithic part of the bonded material. Reliability criteria for adhesive bonding, based on the characteristics of operation, may be:
- water resistance: the ability of the adhesive layer to resist the destructive effects of water;
- heat resistance: the ability of the adhesive joint to maintain strength, solidity and elasticity under the influence of high temperatures;
- biostability: the ability of the adhesive layer and the entire compound to retain its original properties under the destructive effect of biological processes.
Advantages of adhesive bonding
The use of adhesive mixtures based on polymers and synthetic melts has significantly expanded the area of use of plastics. Synthetic adhesive, which is a solution (melt) of the polymer composition, is a plastic processing product. The main advantage of synthetic adhesive bonding is the preservation of the physical and aesthetic parameters of the materials to be bonded. Reliable bonding of planes over large areas is ensured by polymer adhesives. Adhesive joints from polymer compositions have been successfully used both for bonding large areas and for spot bonding of small structural elements.
9 reasons to choose bonding
- Adhesives are able to form strong joints between materials with different physical properties and sizes. Bonding technology surpasses a number of other technologies, including welding, as it is able to combine thin-sheet elements and brittle materials.
- Bonding allows you to evenly distribute stress across the entire plane, which is difficult to achieve using welded or riveted joints. The use of welded and riveted joints is characterized by a high concentration of point stresses only in the joints .
- Adhesive joints provide a high speed of assembly of structures, while being characterized by efficiency. Gluing technology is universal and can replace several ways of connecting elements.
- Developed production technology and a variety of adhesive mixtures makes it possible to use them at various stages of the production process.
- The cost of adhesive bonding and its strength often exceeds the corresponding indicators of alternative options for joining structures and elements. Joints made using glue have a lower weight compared to welded or riveted joints.
- Adhesive materials have a unique ability to absorb, distribute and transfer stresses along the entire plane between structural elements. The elasticity and deformation ability of the adhesive layer increases the reliability of the coupling.
- The glue can successfully combine heat sensitive materials and elements that can break or deform under the influence of high temperature.
- The adhesive can act as a sealing material, providing not only a reliable connection of the structure, but also effective resistance to the destructive action of moisture and chemicals. Glue joints insulate heat and sound well and are excellent dielectrics.
- There are a large number of adhesive compositions designed for difficult climatic conditions; with their help, extremely reliable adhesive compounds are obtained. The use of special compounds makes it possible to glue structures and elements without heating equipment at low temperatures and high humidity.
Disadvantages of adhesive bonding
The main disadvantages of adhesive joints, in particular those obtained using synthetic adhesives, are the impossibility of their use in harsh and especially harsh operating conditions.
Adhesion of structures with glue requires high precision and phased control of their performance. Specialists need to monitor the parameters and modes of bonding, adherence to the curing technology of the adhesive, as well as the rest of the structure during the formation of the hitch. By checking the compounds obtained, the specialist is not always able to determine possible bonding defects.
For many industrial adhesives, the curing process involves the use of heating elements. Hot bonding is often not possible when connecting dimensional complex structures.
What is important to know when considering adhesive joints?
- All bonding technologies require a thorough multioperational surface treatment, which greatly complicates the process. The curing process of the adhesive joint must take place under conditions of a certain humidity, maintaining a constant pressure and temperature conditions. In addition, a period of complete cure can take a long time. For some types of industrial adhesives, at the bonding step, the adhesive joint is heated.
- Adhesive joints are carefully designed, specialists analyze tensile and peeling loads, calculate the stresses that arise due to the difference in the coefficients of thermal expansion of the glued plane and the adhesive joint.
- Glue seams, despite their positive properties, have a significant drawback - low heat resistance. The use of glue for assembly of structures is limited in case of operation of the structure at elevated temperatures. In addition, many types of adhesive joints can be destroyed by mechanical shock.
- Features of bonding elements do not allow to fully control the quality of the connection.
- The joints obtained by gluing are non-separable, for this reason the use of glue greatly complicates the process of disassembling or dismantling structures. In conditions of intensive use in an aggressive environment or harsh operation, it is not possible to calculate the durability of the adhesive joint.