Before carrying out any repair work, a preliminary selection of finishing materials is required. This task is sometimes quite difficult. After all, every owner wants the material used for the interior to be practical and beautiful, durable and, of course, inexpensive.
Almost all the requirements for wall decoration are completely satisfied with Venetian plaster (see photo below).
It is beautiful in its similarity to natural stone, practical due to the application of wax on the surface, which allows it to be washed repeatedly, and also durable during accurate use and can be applied to any surface. Finishing with Venetian plaster has only one drawback - the finishing material, which has simply ideal characteristics, is very expensive. And one more nuance. Applying Venetian plaster is a very time-consuming process, and for the finishing of rooms with this material, many prefer to hire professionals. However, those owners of offices or housing who have independently gone through all the previous stages of repair, may well cope with this matter.
History of creation
This may seem strange to some, but the Venetian plaster, the composition of the mixture, its proportions and the method of application were known long before this building material got its name. And it happened in ancient Rome. Only after centuries, this type of plaster received its rebirth and with minor features was revived in Venice. After that, they began to call her stucco veneziano.
The reason that the composition of the Venetian plaster was developed precisely in Rome was the widespread use of such building material as marble in this country. This natural stone was used everywhere and was very affordable. In addition, after processing marble always remained a large volume of a wide variety of waste. It was spoiled slabs or blocks, crumbs and dust.
And then one day a frugal master, whose name was not preserved in history, came up with a great idea. He decided to use marble trash for good deeds. The collected small crumbs and dust began to be used to prepare a special finishing material, which was used for plastering walls erected from simple stone. The result is simply amazing. After the work, ordinary walls were practically no different from those that were built of real marble. At the same time, this technology had another significant advantage. It significantly reduced the cost of construction and relieved the craftsmen of the laborious process of processing marble blocks.
And only after the repeated revival of this material by the masters of Venice, it began to be called plaster. The latter became beloved by many artists of the Middle Ages, that is, the time when its composition was finally established.
Venetian plaster was used by Raphael and Rossellini, Michelangelo and many others, often using the walls of buildings to express their talent. After all, it was very convenient to do this on Venetian plaster.
Scope of application
Marble is a relatively soft rock with a wide range of diverse patterns and colors, the spectrum of which ranges from the snowy whiteness of the stone of the Carrara quarries to the blackness of the minerals of the Caucasus.
The extraordinary beauty of this natural building material, as well as the possibility of hand polishing it to a mirror shine made it very popular with medieval rulers. It is not surprising that kings and nobles used this stone to decorate their palaces.
However, not everyone could afford such a luxury. And here a wonderful alternative was found to natural stone - Venetian plaster, the composition of which included waste from the production of marble products, crushed to the state of flour, lime as a bonding element, as well as some, as a rule, carefully concealed additives.
The great Raphael and his contemporaries similar material served as the basis for the creation of frescoes. A similar technique, which allows for the decoration of walls under natural stone, was widely used throughout Europe during the Renaissance. White and marble plaster found in many medieval cathedrals.
The most famous examples of the use of this material are the frescoes that adorned the royal castle of Fontainebleau, Roman murals made by Giulio Romano, as well as works by Giorgio Vasari, made in Florence.
The technique of Venetian plaster was constantly evolving and reached its peak in the 17-18 centuries. She could be seen in the magnificent palaces of the rulers of Europe, made in the Baroque and Rococo styles, as well as in the houses of an influential elite.
Classic composition
What in the old days included Venetian plaster? The composition of this mixture by the ancient masters was exclusively natural. Today it may include synthetic and polymeric materials, as well as chemical dyes.
Of course, the most important component that is part of the Venetian plaster is stone dust. As a rule, it is marble. However, sometimes it is made from quartz, granite and some other types of rock. An important condition for this is that the dust grains should be as small as possible.
The second important component that is part of the Venetian plaster is a binder. In the Middle Ages, slaked lime was such an ingredient . In addition to all these components, dyes and water were present in the composition of the Venetian plaster. What gave color to this so attractive finishing material? In ancient times, plant juices, animal blood, bile, and other natural substances served as coloring components for Venetian plaster.
All necessary components were thoroughly mixed to a creamy consistency. Only after this, the plaster was considered completely ready for use.
Modern recipe
If you take into account the not very complex composition of the Venetian plaster, making yourself such a mixture will not be difficult. It is only worth considering that the modern formulation of the finishing material has somewhat changed. So, instead of lime, synthetic binders, acrylic, or other similar materials are included. And, of course, mineral dyes are no longer used today. Their place is taken by artificial compounds.
What else is included in the Venetian plaster? With your own hands, the mixture made can include gypsum, as well as other additives that will change the properties of the finishing material.
Nevertheless, according to many experts, only the classic recipe for Venetian plaster can fully recreate the play of light and the brilliance of marble. That is why those who want to make this material with their own hands, it is advisable to take natural components. Of course, the dye can be used also modern, but marble dust and hydrated lime is quite realistic today.
Ready mixes
The modern building materials market offers the Venetian stucco itself, which can be used for applying to walls. It is sold both in dry and in finished form. The volume of packaged material can be any. This is 1, as well as 5 kg or 15-20 kg. The most convenient for repairs is the packaging volume of five kilograms.
Major manufacturers
Today, you can find on sale various brands of finished Venetian plaster. These are Paladio and Trevignano, Tierrafino with a pronounced mother-of-pearl effect, Veneto, which has the texture of natural polished marble, and Stucco Veneto with silver or gold tinting.
When calculating the volume of material, you should focus on the area of โโthe surface to be treated, acquiring Venetian plaster based on 500-1200 g per square meter.
It is also worth bearing in mind that many manufacturers do not add any dyes to the composition of the Venetian plaster. Such material has only a white base. Color pigments must be purchased separately. For those who want to create a unique Venetian plaster in the apartment, the photo tones of their future interior can be selected using computer tinting. This service allows you to accurately select the desired color. Further, the dye for it will be made by mixing various pigments in a special installation.
Preparation of the dry mix to work
How to make venetian plaster? If an expensive factory mix in dry form is purchased for finishing work, then the following manipulations must be performed:
- Pour cool water into a clean bucket, the temperature of which is in the range from 10 to 15 degrees. Information on the exact volume of liquid is contained in the instructions on the packaging of the mixture.
- The dry component is added to water and mixed thoroughly.
- The composition is brought to a state of uniform texture using a drill with a mixer nozzle.
- After keeping the plaster for 10-15 minutes. kneading is repeated. This will increase the ductility of the material and protect it from delamination.
- At the last stage, the color is added. For accurate proportions it is recommended to use a large syringe.
When preparing Venetian plaster for work, it is important to remember that its composition polymerizes very slowly. But at the same time, after hardening, even partial, it cannot be diluted with water again. The fact is that the adhesive ability of the material will be significantly reduced. This will cause the finish to fall off the base.
Homemade analogue
Venetian plaster can be made at home. In this case, of course, you have to tinker a bit. First of all, it will be necessary to clarify the composition of the Venetian plaster in proportions, and then proceed to its manufacture, which will consist of the following steps:
- Preparation of the base, which is used as slaked lime (50-60% of the total weight of the mixture).
- Adding to the base of mineral milled fillers in the form of marble, quartz or granite dust.
- Mixing the composition to obtain the consistency of batter.
- Entering pigments.
- The final mixing of the product.
For those who like to experiment, you can guess the necessary proportions of the main components after the third or fourth attempt. The final version of the Venetian plaster should provide the desired result.
Application technology
How is Venetian plastering done (see interior photo below)? The main principle of work is the application of a number of thin layers of this decorative coating. They consist of spots of material that are different in configuration and size, which the master arranges in a chaotic manner.
The process of performing work has an important feature. It provides for the formation of layers alternating in thickness. This technique allows you to achieve the most smooth transitions of tones and shades over the entire surface. All this creates a visual depth of natural material and the illusion of a drawing of natural stone.
The first (preparatory) layer is made of material containing marble โflourโ. This will ensure reliable and high-quality adhesion to the wall surface.
After drying of this layer, coating layers are applied to create a patterned texture. If necessary, a whole series of additional layers having different colors can be applied to the glossy final wall surface.
Waxing
In order to create the effect of a natural, but at the same time roughly processed stone, relatively large fractions are introduced into the mixture. They allow you to give a decorative finish layer a rough surface.
However, many owners still prefer to see in their interior an imitation of polished marble, granite, malachite or jasper. Such splendor can be created with the help of Venetian plaster, in which wax will serve as the last, final layer. After applying it, the walls of the room will literally sparkle with all the natural colors.
Types of Wax
The work of applying this material is very painstaking and requires great attention from the master, because the wax layer must be very thin. It should be a kind of film that merges with the structure of the material.
To date, the construction market offers a large number of such coatings, which differ from each other in a variety of ways. Moreover, from all types of wax, the following groups can be distinguished:
- Gel wax. The type of consistency inherent in it perfectly suits a hard and dense plaster layer.
- Liquid solution. It will be good for porous surfaces, which are wonderfully covered with a protective thin layer.
- The natural composition of wax for Venetian plaster, the main component of which is a beekeeping product. Such mixtures are made on the basis of water. Their recipe includes only natural ingredients. After applying natural wax to the surface, it turns out glossy. This is very important for some types of structures.
- Synthetic option. In the composition of such wax are polymer compounds. In this regard, the protective layer of the Venetian plaster turns out to be as resistant to damage as possible. Such a coating will allow the material to last a long time. After applying a synthetic version of the protective layer, the surface of the plaster is matte.
- Transparent wax. This coating option is most often used for Venetian plaster.
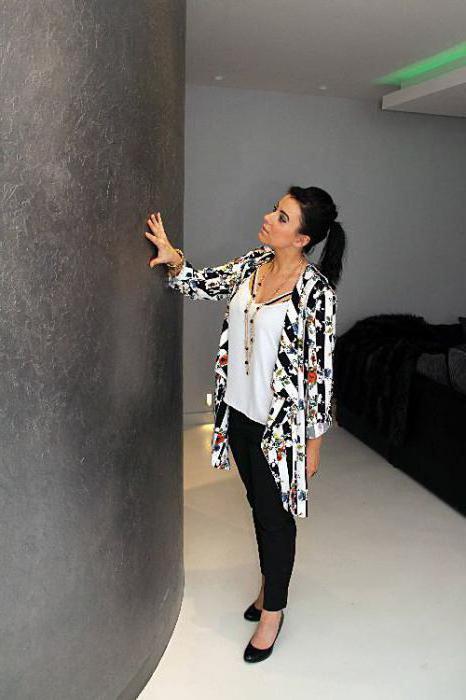
Many craftsmen have their own secrets not only to use, but also to make wax for Venetian plaster. So, Antonovโs wax is widely known. This is a specialist in Venetian plaster from Kiev, who is also the author of numerous courses.