Logistic costs are the material costs necessary to cover the costs of transporting goods with goods or material and technical values. They also include other expenses related to man-hours. The latter include the salary of personnel who manage the logistics system and directly delivers goods from one point to another. To take into account which logistics costs can be excluded and which can be reduced, special formulas were invented to calculate all the costs of the enterprise. This procedure is called accounting. It is reflected in the balance of a separate account in the accounting department of the company.
What are the costs
Costs associated with logistics activities are classified according to several criteria:
- Aspects of directions - this includes costs associated with the procurement processes, stages of production, stages of distribution of raw materials and goods.
- The place where costs arise - here a “point” is formed where the future contribution to the development of logistics activities will be concentrated. These include departments of management, supply, marketing and transport. This is the most important part of the costs, because it is the essence of the logistics of any enterprise.
- Component processes - movement and storage, warehousing and verification of goods. This includes the costs of covering information techniques.
- Logistic costs are also divided into tangible and intangible. The first include the cost of depreciation, fuel, resources. The second type includes the process of using third-party capital, payments in the form of taxes, etc.
- The economic content includes only those costs that are necessary to cover damage in production and lost profits.
The main material logistics costs are formed due to the structural units of the company. In the main connection are the costs of implementing processes for the transportation and sale (marketing) of goods.
Classification of logistics costs - a form of their formation
The main cost system is focused on the formation of current expenses. Logistic costs in the macroeconomic environment form a centralized sales and import system. This applies not only to enterprises, but also to countries. Export and import often affect such types of logistics costs, such as covering excess indicators of unplanned repair work. They are classified as variable and fixed costs at the same time.
If the company sends the goods to another country, the main problems become ways to save not the product, but the vehicle. Not always the roadway is of high quality, but vehicle maintenance can be done anywhere in the world. Do not forget about the roads in winter, which can often provoke problems. In the process of moving a vehicle from point A to point B, unforeseen situations almost always happen, so it is reasonable to calculate force majeure circumstances in advance in the framework of "unpredictability".
Outsourcing in this case is a good solution to the problem. If it is possible to save financial resources to cover damage at other stages of production activity, then logistics costs are reduced in the form of education and the prerequisites for the appearance. At the microeconomic level, all costs are considered rational when it comes to small wholesale or distribution. Here the financial spending scheme is simple:
Decor | Implementation | Sales organization |
First, we use equity, which goes to cover the costs of procurement and storage of goods. | The accompanying documentation should always be relevant, therefore its quality meets international standards. You can check the adaptation according to GOSTs, which prescribe the correct accompaniment of papers. | At the first stage, the goods should be shipped to the car. Further, documentary support is conducted - weight, dimensions, departure. |
Then comes the adaptation and sorting of commodity values. Sometimes re-purchase of missing materials is required. | Set the shelf life of the product until loading. If it exceeds the established time frame, the buyer is obliged to notify the seller about this, since the costs will be paid "out of pocket" of the company where the products are being taken from. | Do not forget about authorized tax payments. If the management of logistics costs is not carried out to the full extent, then unforeseen circumstances will arise , such as cargo weight, machine malfunction, etc. |
Next, all documents for the import or export of goods are drawn up. | If a special refrigerator with the possibility of mobile installation is required, the exporting company organizes planned transportation in advance, according to the concluded agreement with the receiving party. | At the time of transportation, the damage coverage at customs is taken into account. Cargo may be missed with a delay, which violates the delivery time. In this case, all organizational aspects are taken over by the receiving party. If the cargo is damaged, damage is recorded due to other reasons (improper storage, loading / shipment), then the sender will bear the costs. |
This creates a classification of logistics costs, taking into account external factors on both sides of the mutual agreement on the supply and acceptance of goods.
How to manage expenses
Under the management often understand the importance of reducing the cost of production of a particular product. The better this indicator, the higher the competitiveness of the company. In other words, a company that spends money on expenses cannot compete with another company, which occupies a leading position due to the fact that its efficiency indicator is higher. So, the saved money is put into circulation:
- New markets are being created instead of previous ones.
- The production technology is being improved instead of the conservative method of old billets.
- The market place is improving and gaining a foothold - it is difficult to move the leader, especially if the equipment is not able to compete quantitatively and the product is qualitative.
Management of logistics costs in the modern economy is a means of improving leadership qualities and positions in relation to other business participants. To do this, create a concept, estimate, business plan, which include:
- The purchase of new equipment - the better it is, the higher the productivity, which means that the work efficiency per hour (unit of technical work) will be better. The costs of approaches to the management of technology are reduced, heading in a different direction.
- Management accounting - this includes not only human factors, but also the training of personnel for such work. If people can perform tasks at one speed, then, having received new equipment, cost accounting will require less time and man-hours. This means that the employee will have to do more for the same cost of labor, which will bring more benefits in a short period of time.
- International market - to enter it, the company should be adapted to work in accordance with European standards. This includes quality indicators, innovation and attracted foreign capital.
If we talk about man-hours, as a component of non-machine mind, then we can give such an example. The publishing house decided to expand its customer base, but this required two new employees. One of them has experience in the field of media, but is slowly typing. The second young employee has a high printing speed, but does not know the specifics. Thus, you need to create two materials:
- The first employee is given out of a hundred sheets in total 30.
- The second - all the remaining of the hundreds, but they are with a simpler theme.
- As a result, it turns out that all the work will be done both quickly and efficiently.
This is the meaning of the reduction and cost management of any company, when several things are performed simultaneously. The same thing happens with the introduction of new equipment - keeping records is much easier when there is good equipment, programs and convenient schemes for calculating. Unlike the traditional and familiar accounting method, logistics already allows the implementation of operational accounting. This will make it easier to manage and monitor processes. Thus, an indicator of dependence is formed - how profitable it is to spend finances and investments on personnel who perform the effective work of the order.
Summing up expenses during the day, week, month or year, you can see the potential increase in profit and net income of the company. The higher it is, the better is the work of employees, the higher is labor efficiency. In economic practice, it is shown that two-thirds of the costs cover procurement transportation costs. The rest is spent on damages or stocks in case of loss.
Ways to analyze company costs
Any costs should be included in the price of the goods. This is the amount that the consumer paid in the end, and not the difference between the costs and income that the legal entity pays. There is a dependence on the personal qualities of a person, but in the transport system it is not much manifested. More attention is paid to such a factor as the analysis of logistics costs. To carry out the analysis, you need to know all the cost indicators that affect the total final amount of consumer demand. Too high prices, for example, in the production of environmental bags, dishwashing detergents, will be logical if the quality standard is really taken into account at the enterprise.
It is clear that here we are only talking about natural products and product elements - they are more expensive, since it is easier to create an artificial product. The process does not depend on time, cultivation, type of extraction. Natural products always require a thorough approach to the collection and processing of raw materials. Further, only by special technology purchased from the owner, on specialized equipment provided by tender or purchased on credit, the company begins to develop the basics and procurement of future goods. At the initial stage, the following conditions are immediately foreseen:
- Properties of goods during storage.
- The ability to combine with other components.
- Medicinal or beneficial properties.
- The best value for money.
Methods of analysis of logistics costs are adjusted in direct proportion to the scope of the company. If it operates in the product area, then the requirements are established in accordance with the current legislation on food and raw materials. If the work is related to the industrial production of raw materials, blanks for construction and further use of products in another manufacturing process, the conditions for storage and transportation are completely different. Logistic cost analysis methods help to compare the cost price and the final potential cost of the goods for the client directly. The final amounts for each analysis may differ from the prices of competitors, so it is important to calculate these criteria in advance.
Cost element optimization
Any cost optimization is associated with the selection of a favorable offer and working conditions for the company. As a rule, all large commercial and industrial enterprises try to produce large batches of products, since in this way the costs of raw materials and other expenses pay off, bring profit and high net income. As soon as supplies are reduced, companies are forced to look for new markets - the lack of outlets and subsequent sales leads the company to stagnation. In this regard, one has to look for private buyers, bypassing the tax system. Many managers are interested in how to optimize the elements of logistics costs so that for each of these items the costs are minimal.
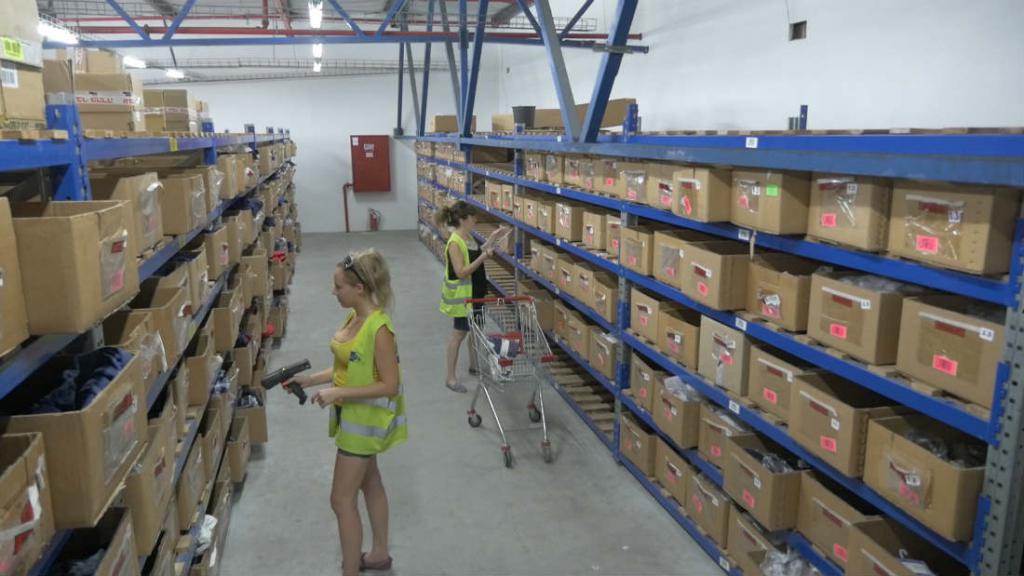
To do this, turn to mathematics and number theory - a comparison and analysis of potential risk will allow a little closer to the real amount of costs. It is necessary to compare the existing methods in business and those possible measures that could reduce costs. Preference should be given to categories of fixed and variable costs. Optimization of logistics costs begins with a series of new contracts and agreements, which specify new conditions for:
- Deliveries of goods at reduced terms without overpayment.
- Storage of goods without payment of technical costs for damage.
- Holding auctions - this saves money on a tender for direct delivery of goods in small batches.
- Use of own or borrowed vehicles.
The most important thing is delivery and proper storage - the goods did not disappear and did not deteriorate, which means that the integrity of the amount is preserved. The goods are delivered to the buyer and consumer, the money in full is saved. Also, optimization of logistics costs is not complete without calculations based on preliminary data, which may reflect the estimated cost of costs. Of course, any new equipment should be tested and pay off on time.
For example, a dental clinic decided to purchase equipment that will take x-rays without the need to purchase vests to protect against radiation. The company saves on them, because their shelf life is only 1-1.5 years. New equipment will be more expensive, respectively, the price of services will increase. The buyer’s benefit is determined, but the seller’s income will be higher if several deliveries are made along the route of consistent movement. One way is sustained, and several deliveries are made. The same thing happens in a courier private company - goods are loaded and transported, like passengers in a taxi, along a profitably adjusted route.
Calculations of costly activities
Cost indicators for each type of investment should be considered when forming the total cost of expenses. They will make a total profit by receiving money for the goods. Calculation of logistics costs is carried out according to the following criteria:
1. The size of the delivery lot. The sensitivity of costs in relation to the deviation of the weight and size of the product is determined. If transportation is carried out by trucks or trucks, the measure in tons is taken.
2. The increase in the party when deviating from the norms of delivery due to costs.
Consider this with simple calculations:
1. Let us set the deviation from the optimal lot of delivery 30% (plus / minus), and let the optimal size of supply (q0) be equal to 19.11 tons. Then the actual size of the delivery will be equal to:
q1 = 0.7 q0 = 13.4 t (in case of deviations to the lower side).
q2 = 1.3 q0 = 24.8 t (with a deviation up).
The increase in the value of logical costs can be calculated by the following formulas:
For the resulting q1 - (Czp (q1) - Czp (q0)) / Czp (q0) = 6.4%.
For the calculated q2 - (Czp (q2) - Czp (q0)) / Czp (q0) = 3.4%.
Szp - this is the amount of all costs per consignment (for q0, q1 and q2).
The size of the order for a fixed period between orders is made according to the formula:
q zak = S - q tech + T zak D days
In it:
q tech - current stock status at time of order.
S - upper level of stock volume.
T zak - lead time.
D days - the average daily demand or consumption of goods.
If we are talking about passenger transportation, then all transport and logistics costs are borne by the driver.
The costs of airlines are calculated in the same way - the principle of pricing is predetermined by the method of establishing cost.
Cost Reduction and Redistribution
At present, automated systems, hardware technologies and Internet communications are helping to reduce the company's costs. Instead of human labor, machine intelligence is used, so the number of staff is reduced. As a result, labor costs fully cover the purchase and consumption of the system, its operation and maintenance. Logistic costs can be reduced only by mutual agreement with suppliers and the party receiving the goods. Specialized accounting systems can also be introduced inside the enterprise, which will reduce staff, that is, reduce the number of staff and their salaries.
- It is worthwhile to foresee the possibility of reducing wholesale and retail costs. If the importer inflates the price, then demand will decline, there will be no sales. Cooperation in the foreign economy can lead to higher prices by adapting the production of goods for export to another country. In this regard, prerequisites for the creation of a trade bridge appear, for example, as between Russia and China.
- Personnel training and putting theory into practice. This is facilitated by business seminars that some directors neglect. Instead of a small business, a person will be able to open several points in other countries for sales. This is beneficial to him, as the host will be his representative, and not a company with other interests.
- Redistribution of costs for cheap resources. These methods have long been used in production, since natural ingredients in food products and things are a luxury that not everyone can afford.
- Establishing quality communications with suppliers, importers and other chain links in the commercial and industrial segment. If the driver is always in touch, like the buyer, things are faster than those who do not leave the office in the literal and figurative sense of the word.
- The effectiveness of labor motivation - instead of material incentives, you need to influence the psychological methods of staff motivation. For example, the prize can be replaced with vouchers, free dinners, and thanks.
- You can offset costs in one segment by lowering costs in another. Then the whole chain of "raw materials - finished goods" will be optimized for the business plan with the introduction of adjustments.
A cardinal option would be the exclusion of all types of enterprise activities and positions that the business does not need. If you need to dismiss the person who is responsible for communication with the coordinator, then part of the salary costs can be compensated by the communications and monitoring department by adding responsibilities and increasing the rate. At the same time, costs are partially reduced, as well as unscheduled expenses and other measures for the maintenance and reflection of the position in the staffing of the company.
Improving the sales and procurement system
Product sales are a key indicator of the progress of any business. The lower the cost of the logistics system, the more profitable it is for the company to carry out its activities within the framework of modernization and improvement. Purchase and sales are two components for establishing trade between firms, economic agents, enterprise services and countries. At different classroom levels, their nuances are manifested that do not allow you to create an inextricable chain without interrupting business. Just as new products should constantly leave the lines on the conveyor, so should goods be regularly sent to the buyer. High sales determine good purchasing power and product quality. Improving the two systems is not very simple, but it is enough to consider the issue of horizontal linear hierarchy. Then the opening of new outlets will improve the position of the company, and demand will necessarily increase.
However, one should take into account such nuances as the indicative principles and traditions of the people where the goods will be delivered.
Introducing innovations in the transport logistics system
Now no company can do without computer technology, which means that innovation for these enterprises is not news. Recently, the global economy has less and less established “free trade zones,” which negatively affects companies. Many transport companies “switched” to the domestic market due to high taxes and collection conditions for each transport connection. The logistics costs of the company began to be renamed over the past few years into "Lean-logistics" (lean logistics). The reason for this was the modernization of airlines. She touched almost all corporations.
Now optimization becomes the task - this is the main criterion, according to the economic and social survey conducted by the new GroozGo logistics startup. According to the majority, and their 67% of respondents, a "lean economy" for the current pace of trade is simply necessary. If necessary, they will build roads, bridges, air corridors for convenient and quick customer service. Logistic costs of the enterprise should be reduced by combining several companies, for example, flights on one chart. This will help to save on tax payments, deposits in fuel and other logistics costs.
The innovation will also appeal to customers - the waiting time will be reduced, the base rate for DHL delivery will increase. Unified monitoring systems for satellites are being introduced, which gives out communication via Internet network channels.
Save time: how to reduce logistics costs and expenses?
The question concerns not only the field of economic relations, but also the sphere of small internal capital turnover. General logistics costs can be reduced only by opening a point (store) where consumers themselves would come for the goods. Then quality and price, availability and offer should be at the highest level. But it is unlikely that someone will fly to another country to buy a thing that can be purchased through online delivery for almost the same money. Therefore, if you save, then only on the time of the client and the method of providing the goods.
Logistic costs of the enterprise can be offset by removing part of the chain in production. Large American companies use online stores, software to communicate with suppliers, customers, etc. Everything is modernized and not costly, providing full "full" to implement the delivery function to anywhere in the world. Robotic automation of all systems will soon become the main sources of calculating needs, plans, strategies and the whole business, and people will only adjust the activities of their creation in the form of machine installations.