Once upon a time, coke oven gas was considered a by-product in the process of creating coke, so it was often even released into the atmosphere (which is very in vain!). Later, gas began to be used for the heating of coke ovens, and today it is fully given to outside consumers for domestic use and for other needs. How is coke oven gas produced and what is its composition? This article discusses all aspects of the issue and provides specific examples of the use of gas.
Historical aspect
The history of coke oven gas began even in the late 19th - early 20th century. Even then, it was used for lighting, heating and, accordingly, for cooking and in other household matters. At that time, the industrial revolution and urbanization erupted. The production of by-products, coal tar and ammonia began to serve as the most important components, namely, raw materials, in the manufacture of chemical dyes and in the chemical industry as a whole. Thus, absolutely all types of artificial dyes were made from resin and coke oven gas.
In addition, coke oven gas has become widely used in furnaces for the manufacture of industrial products, in gas-powered engines, and, of course, as a raw material in the production of chemical products.
Coke oven gas production
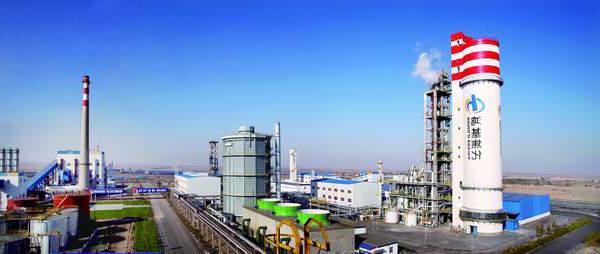
The production of coke oven gas occurs simultaneously with the production of coke at coke plants by dry distillation of coal. It is important to note that this process must necessarily proceed at a temperature of 900-1200 degrees. As noted above, at the initial stages of nucleation, gas was considered a by-product, therefore, it often escaped into the atmosphere. A little later, using coke oven gas, coke ovens began to be heated . So, gas consumption for personal needs has undergone a significant reduction (almost up to 60%), the remaining amount belonged to other categories of consumers, for example, for heating metallurgical production furnaces, the temperature of which is extremely high, or for domestic affairs. Today, absolutely all gas belongs to outside consumers. Why? The fact is that coke oven gas is very high-calorie, which means that it is possible to use cheaper gas for heating stoves. A vivid example of this is liquefied gas. By the way, its basis is a propane-butane mixture.
Coke oven gas: composition
As it turned out, of the many gases of artificial origin, the gas considered in the article and obtained in the process of coking coal is of great importance. It should be noted that from a practical point of view, its composition undergoes significant fluctuations. It depends, as a rule, on the feedstock used as fuel, on differences in the modes of activity, on the physical condition of coke ovens, and so on. Its calorific value lies in the range of 15-19 MJ / m3. If we consider the components of this gas as a percentage of volume, then the following picture is formed:
- H2: 55-60.
- CH4: 20-30.
- SO: 5-7.
- CO2: 2-3.
- N2: 4.
- unsaturated hydrocarbons: 2-3.
- O2: 0.4-0.8.
It is important to note that coke oven gas (formula: 2CH4NH3C2H4) has a density at a temperature of zero degrees from 0.45 to 0.50 kg / m3, the heat capacity is equal to 1.35 kJ / (m3 Β· K), and the temperature associated with the ignition process reaches 600-650 degrees.
Substance formula
As it turned out above, coke oven gas contains substances such as hydrogen (H2), methane (CH4), ammonia (NH3) and ethylene (C2H4). As an example, it will be advisable to give the following composition of purified coke oven gas:
Component | H2 | CH4 | With | N2 | CH | O2 |
Content% | 55.5 | 27.6 | 8.2 | 6.0 | 2.0 | 0.7 |
It is important to note that the composition of the gas in question strictly depends on the temperature regime of the coking process and its duration. The quality of the coal being processed also plays a huge role. Thus, the higher the temperature regime of the coking process, the greater the level of decomposition of hydrocarbons, and hence the higher the content of hydrogen and carbon monoxide in the gas . Accordingly, the carbon dioxide content , on the contrary, will be lower.
The need for coke oven gas purification
Today, the problem of the need for purification of coke oven gas is quite acute, because this composition adversely affects the environmental aspect of life. Thus, modern society seeks to improve relevant technologies. The purification of coke oven gases is necessary for the efficiency of factory mechanisms, because hydrogen cyanide, whose content in coke oven gas is high enough, is the main cause of corrosion of professional equipment. In addition, ammonia is necessarily released during the formation of coke oven gas. This substance is extremely detrimental not only to pipelines, but also to the environment, because ultimately it gets there. The result of the considered operations is a high level of loss of products of chemical origin for a particular plant, as well as a significant degree of emission of gases and waste of liquid origin into the atmosphere.
Coke oven gas purification process
As it turned out, the production of coke oven gas entails a number of problems, which fully justifies the need for its purification. To date, the most effective method is the invention described in this chapter, which is widely used in the coke industry. First of all, it is necessary to flush the gas with a solution of ammonium phosphates in the absorber, which must be equipped with plates. Next, it is necessary to treat coke oven gas before it enters the dish-shaped area of ββthe absorber with this solution. In this case, the specific consumption of the circulating solution should be 1.0-1.2 l / m3 of gas, then its density will be equal to 1.195-1.210 kg / l. This method of purification of coke oven gas, as noted above, is often used today in the relevant industry, because it is the most effective.
Coke oven gas: application
To date, coke oven gas is widely and safely used in society as fuel in metallurgical plants, as well as in public utilities and as a raw material for production. As it turned out, hydrogen is extracted from coke oven gas, which is simply necessary for the synthesis of ammonia by means of a known method of condensation of functioning under conditions of low temperature conditions. As a result of this operation, a fraction is formed that serves as a quality raw material for various kinds of syntheses. It should be noted that an admixture in coke oven gas of hydrogen sulfide is completely undesirable in any case (both when coke oven gas is used as fuel and when it serves as a raw material for the production of chemical products). That is why the cleaning process, fully considered in the previous chapter, is so necessary.
Gas properties
In conclusion, it would be appropriate to consider the physical properties of coke oven gas . Thus, its calorific value is from 3600 to 3700 kcal / m3, the specific gravity in the composition of the substance varies from 0.45 to 0.46 kg / m3 (which is almost three times lighter than air), the maximum temperature regime of its combustion is equal to 2060 degrees, and the process itself is accompanied by a red flame.
It is important to note that the gas in question is explosive if combined with air. Moreover, the explosive limit of the lower level in volume is 6 percent of gas (the rest is air), and the upper explosive level reaches 32 percent of gas (the rest is air). The ignition temperature is equivalent to 550 degrees, and to burn 1 cubic meter of gas, approximately 5 cubic meters of air are needed. Coke oven gas is not endowed with color and taste, however, it has a tart smell of naphthalene, rotten eggs, which can be explained by the content of hydrogen sulfide in its composition.