The principle of operation of a synchronous motor is approximately the same as that of an asynchronous motor . But there are several differences that are key when choosing a motor for a particular design. Asynchronous machines are widely used in industry - their share reaches 96% of the total number of electric motors. But this does not mean that there are no other types of electrical units.
Difference from asynchronous motor
The main difference between a synchronous machine is that the speed of rotation of the armature is the same as a similar characteristic of the magnetic flux. And if a squirrel-cage rotor is used in asynchronous motors, then in synchronous motors there is a wire winding on it, to which an alternating voltage is supplied. Some designs use permanent magnets. But this makes the engine more expensive.
If you increase the load connected to the rotor, its speed will not change. This is one of the key features of this type of machine. A prerequisite is that a moving magnetic field should have as many pairs of poles as an electromagnet on the rotor. This is what guarantees a constant angular speed of rotation of this engine element. And it will not depend on the moment applied to it.
Motor design
The device and principle of operation of synchronous motors are simple. The design includes elements such as:
- The fixed part is the stator. There are three windings on it, which are connected according to the "star" or "triangle" pattern. The stator is assembled from plates of electrical steel with a high degree of conductivity.
- The moving part is the rotor. It also has a winding. During operation, voltage is applied to it.
There is a layer of air between the rotor and the stator. It ensures the normal functioning of the engine and allows the magnetic field to freely act on the elements of the unit. The design contains bearings in which the rotor rotates, as well as a terminal box located in the upper part of the motor.
How the engine works
In short, the principle of operation of a synchronous motor, like any other, is to convert one type of energy into another. Specifically - electrical to mechanical. The motor works this way:
- An alternating voltage is applied to the stator windings. It creates a magnetic field.
- Alternating voltage is also applied to the windings of the rotor, creating a field. If permanent magnets are used, then this field is already by default available.
- Two magnetic fields intersect, oppose each other - one pushes the other. Because of this, the rotor moves. It is it that is mounted on ball bearings and is able to rotate freely, you only need to give it a push.
That's all. Now it remains only to use the obtained mechanical energy for the necessary purposes. But you need to know how to properly bring a synchronous motor into normal mode. The principle of operation is different from asynchronous. Therefore, you must adhere to certain rules.
For this, the electric motor is connected to equipment that must be set in motion. Typically, these are mechanisms that should work almost non-stop - hoods, pumps, and more.
Synchronous generators
The reverse design is synchronous generators. In them, the processes proceed a little differently. The principle of operation of a synchronous generator and a synchronous motor differ, but not significantly:
- No voltage is applied to the stator winding. It is removed from it.
- An alternating voltage is applied to the rotor winding, which is necessary to create a magnetic field. Electricity consumption is extremely small.
- The rotor of an electric generator is spun by a diesel or gasoline engine or by the power of water and wind.
- Around the rotor there is a magnetic field that moves. Therefore, EMF is induced in the stator winding, and a potential difference appears at the ends.
But in any case, it is necessary to stabilize the voltage at the output of the generator set. To do this, it is enough to power the rotor winding from a source whose voltage is constant and does not change with fluctuations in speed.
Motor winding poles
The rotor design has permanent or electric magnets. They are usually called poles. On synchronous machines (motors and generators), inductors can be of two types:
- Explicitly.
- Implicitly.
They differ among themselves only in the relative position of the poles. To reduce the resistance from the magnetic field, as well as improve the conditions for the penetration of the flux, cores made of ferromagnets are used.
These elements are located both in the rotor and in the stator. For manufacturing, only grades of electrical steel are used. It has a lot of silicon. This is a distinctive feature of this type of metal. This allows you to significantly reduce eddy currents, increase the electrical resistance of the core.
Exposure to poles
The design and principle of operation of synchronous motors is based on ensuring the influence of the pairs of poles of the rotor and stator on each other. To ensure operation, it is necessary to accelerate the inductor to a certain speed. It is equal to the one with which the stator magnetic field rotates. This is what allows for normal operation in synchronous mode. At the moment when the start occurs, the magnetic fields of the stator and rotor intersect. This is called “sync entry”. The rotor begins to rotate at a speed similar to that of a stator’s magnetic field.
Synchronous motors starting
The most difficult thing about a synchronous motor is its launch. That is why it is used extremely rarely. After all, the design is complicated by the launch system. For a long time, the operation of a synchronous motor depended on the asynchronous accelerator mechanically connected to it. What does it mean? The second type of motor (asynchronous) made it possible to accelerate the rotor of a synchronous machine to a sub-synchronous frequency. Conventional asynchronous devices do not require special devices for starting, it is enough to apply operating voltage to the stator windings.
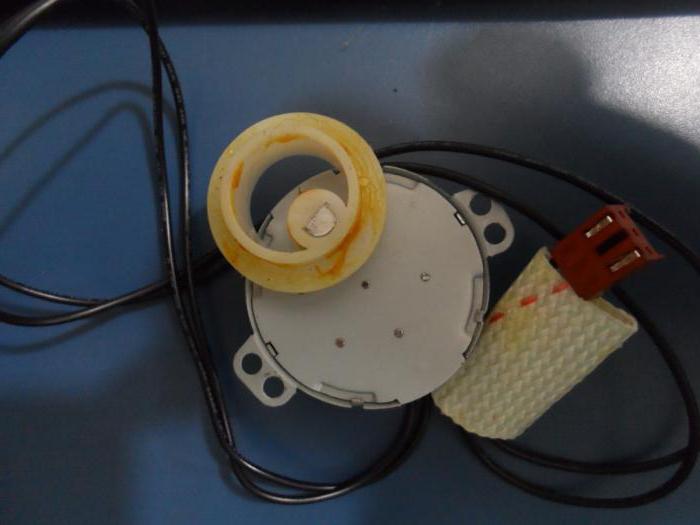
After the required speed is reached, the accelerating engine is turned off. The magnetic fields that interact in the electric motor themselves bring it to work in synchronous mode. To accelerate, you need another engine. Its power should be approximately 10-15% of the similar characteristics of a synchronous machine. If you want to put the electric motor 1 kW into mode, it will require an accelerating motor with a power of 100 watts. This is quite enough for the machine to be able to work both in idle mode and with a slight load on the shaft.
A more modern way to disperse
The cost of such a machine was much higher. Therefore, it is easier to use a conventional asynchronous motor, even if it has many shortcomings. But it was his principle of work that was used to reduce the size and cost of the entire installation. Using a rheostat, the windings are closed on the rotor. As a result, the engine becomes asynchronous. And it turns out to be much simpler to start - voltage is simply applied to the stator windings.
When the sub-synchronous speed is reached, the rotor may swing. But this does not happen due to the work of its winding. On the contrary, it acts as a sedative. As soon as the rotation speed is sufficient, a constant voltage is applied to the inductor winding. The engine is output in synchronous mode. But this method can be implemented only if motors with a winding on the rotor are used. If a permanent magnet is used there, an additional accelerating motor will have to be installed.
Advantages and disadvantages of synchronous motors
The main advantage (when compared with asynchronous machines) is that, due to the independent supply of the rotor winding, the units can operate at a high power factor. You can also highlight such advantages as:
- The current consumed by the electric motor decreases, and the efficiency increases. Compared with an asynchronous motor, these characteristics are better for a synchronous machine.
- The torque is directly proportional to the supply voltage. Therefore, even if the voltage in the network decreases, the load capacity is much higher than that of asynchronous machines. The reliability of devices of this type is significantly higher.
But there is one big drawback - the complex design. Therefore, during production and subsequent repairs, the costs will be higher. In addition, a DC source is required to power the rotor winding. And it is possible to regulate the rotor speed only with the help of converters - their cost is very high. Therefore, synchronous motors are used where there is no need to often turn the unit on and off.