Flywheel, without exaggeration, can be called the most universal device. It not only compensates for the uneven rotation of the crankshaft and transmits torque from the engine to the gearbox, but also spins the crankshaft during start-up. Smoothing of pulsations of torque occurs due to periodic short-term accumulation and subsequent transfer of kinetic energy. The energy reserve occurs during the working stroke of the piston, and the flow rate is in other cycles. At the same time, the more cylinders (and, consequently, the greater the total working time), the more uniform the torque of this engine, and therefore, the mass of the flywheel may be less.
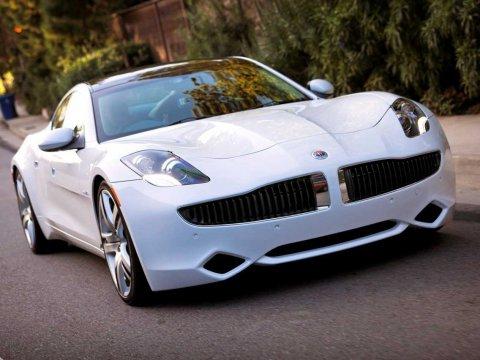
By their design, flywheels come in several forms. The most common - solid - is a massive cast-iron disk with a diameter of 30-40 mm with a steel toothed crown pressed onto its outer side, which allows the crankshaft to rotate during start-up with the help of a starter. There is also a dual-mass flywheel and lightweight. The use of a two-mass flywheel, which includes two disks, made it possible to get rid of the installation of a damping device in
the clutch disc .
A lightweight flywheel is usually used when tuning the engine. The decrease in
moment of inertia occurs due to the displacement of the flywheelโs main mass closer to the edges of the disk, as a result of which its mass decreases (up to 1.5 kg), its dynamic characteristics improve, and engine power also increases (up to 5%).
How does a dual-mass flywheel work?
This flywheel does not consist of one, but of two bodies. The first of them is connected directly to the crankshaft and is also the crown of the starter. The second housing is the basis for mounting the clutch assembly. Both cases are interconnected by means of plain bearings (radial and thrust), having an intermediate damping system. The connection device allows them to move relative to each other in the axial direction. Inside, the dual-mass flywheel is filled with
grease for efficient and proper operation of the spring packages. Packages, in turn, are separated by special plastic separators that prevent them from being blocked.
A two-mass flywheel works according to a stepwise principle. Soft springs of the first stage are responsible for starting and turning off the engine. Stiffer second stage springs provide torsional vibration damping during normal riding.
This design is made for more reliable damping of vibration, noise reduction, reduction of synchronizer wear, protection of the engine transmission from overloads, and convenient gear shifting. At the same time, there is increased wear of the spring-damper system, usually ending in a breakdown of the arc spring - the main element of a two-mass flywheel.
When do I need to change a dual-mass flywheel?
Uneven engine operation, vibrations, and idling noise can cause abnormal operation of the ignition system, plunger pairs, throttle, and other devices and assemblies, including a sign that the dual-mass flywheel is faulty. Symptoms that clearly indicate that it is time to replace it are as follows:
- formation of cracks on the surface;
- loss of lubrication in the clutch housing;
- Itโs not possible to turn it in either direction.
Repair of a two-mass flywheel in artisanal conditions is practically impossible, and therefore usually it changes entirely.
Although, in some cases, rebuilding and repairing a flywheel can be cheaper than acquiring a new one (the minimum price of which is approximately $ 500). Another option may be to replace it with a conventional all-metal one - an analog of a two-mass one.
According to experts, for a longer and more reliable operation of a two-mass flywheel, it is necessary to observe elementary operating rules, namely: for diesel engines designed to work with high torques, do not allow long-term operation at low speeds, as well as depress the clutch pedal before turning off the engine .