The operation of storage facilities requires special safety measures. This is connected not only with the possibility of storing materials unsafe from the point of view of ignition, but also with the use of special technical means. In addition, we can talk about maintaining optimal working conditions, which include sanitary and hygienic characteristics, and microclimate indicators. To take these and other factors into account, a safety manual for the warehouse is drawn up, which also prescribes the rules of conduct for the employees themselves.
General Safety Standards
All employees of the enterprise servicing the warehouse facilities must undergo appropriate training and only after checking the knowledge and skills obtained are allowed to work. Also, equipment with inventory, technical means, tools and consumables are subject to a preliminary audit. Masters, led by an engineer, check the condition of the units, compare their characteristics with the requirements of the working process, if necessary, carry out preventive repairs, etc. Depending on the tasks that the worker performs, the appropriate elements of protective clothing should be given to him. General safety standards in the warehouse indicate the mandatory use of hats, safety shoes, and in some cases gloves, aprons and dressing gowns. However, clothing for warehouse workers should not have hanging ends, and long hair is tucked under a hat.
Fire safety measures
A serious hazard in terms of fire risks is usually wrapping and wiping material. It must not be left unowned. To store such waste in warehouses, metal containers with tight refractory lids are used. In case of fire, appropriate equipment should also be provided, the elements of which are determined by specific operating conditions. If there is a structural possibility, active fire extinguishing systems are also installed. As a rule, these are ceiling sprinkler and deluge devices for spraying water and foam. As for the workers themselves, the fire safety equipment at the warehouse requires them to know the points of location of fire fighting equipment, evacuation routes and the presence of basic skills in handling tools to eliminate fires.
Preparation for work
Before the start of the workflow, each employee audits the area he serves. They may be different depending on the specialization. For example, the storekeeper clears the aisles between the racks, freeing them for the passage of forklifts. Engineers and drivers, in turn, check the condition and availability of technical equipment: cranes, loaders, manipulators, stackers, etc. In addition, safety measures in the warehouse require checking the serviceability of auxiliary devices, including hoists, hoists, hooks and other heavy devices designed to lift various loads. After that, the attendant should adjust the lighting to optimal radiation indicators, start up climate control equipment if necessary, and open the ventilation ducts.
Safety measures in the warehouse during work
Each warehouse employee must fulfill their obligations under a specific instruction. If his work is related to the operation of equipment, he must periodically check its condition, perform maintenance and, if necessary, repair measures. Tools, implements, and supplies should be kept in special rooms, on shelves, and in vertical mounting panels. Metrological instruments are stored only in special cases and boxes. For such a tool, special climatic conditions may also be required. Special attention is also paid to safety measures when working in a warehouse, which is associated with ensuring the reliability of electrical wiring. In particular, cable insulation and the absence of short circuit risks are checked. Testing transformers and safety blocks is important not only because of the safety of workers, but also from the point of view of maintaining sufficient current parameters in the circuit to power the power tool and lifting equipment.
Safety rules at the end of the workflow
After the shift is completed, the warehouse workers must bring their places and the tool in use to their original condition. The equipment must be properly stacked, and the controlled area must be cleaned of foreign objects and materials. If there is a defective tool, the employee must transfer it to the appropriate service and repair department. It is important to emphasize that safety measures at the warehouse prohibit not only correcting non-working equipment to persons who do not have access to such events, but also, in principle, carry out repairs in places not intended for this.
Accident Safety
It is almost impossible to fully insure the workflow from situations with equipment breakdowns, disruptions in the operation of utilities and other contingencies. When fixing the accident, the warehouse should be stopped, the electrical equipment should be disconnected, and the appropriate emergency service should be called depending on the nature of the incident. This may be a medical ambulance, a fire brigade or an emergency service. Along with this, safety regulations for the warehouse indicate the need to evacuate people before the arrival of specialists. This is especially true for cases of fire. If electrical equipment is covered by a fire, powder or carbon dioxide fire extinguishers should be used to minimize damage. If the accident is associated with damage to the power supply line, then first of all the current supply is cut off. That is, the main electrical installation is turned off through a special switch or control panel.
Instructions for drivers of material handling equipment
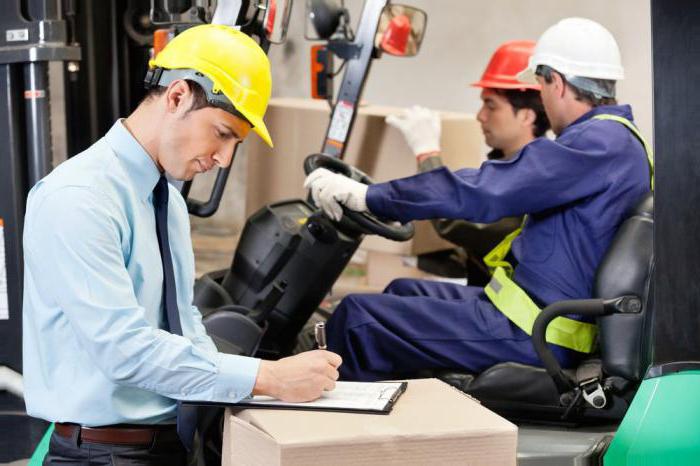
Before the start of work, the technical condition of the equipment must be checked. Further, depending on the dimensions and other parameters of the target material, the operator adjusts the functional organs of the loader accordingly. It can be forks, grabs, hooks and other devices, due to which the load is fixed and moved. It is important that the characteristics of the equipment correspond to the mass and size of the object to be moved, otherwise there will be a risk of breakdown of the same working bodies due to overload. Already in the process of moving the driver must adhere to speed standards. As required by the safety instructions in the warehouse, the ride of forklifts and stackers should not exceed 3-5 km / h, depending on the operating conditions of the vehicle. All lifting, grabbing and tempering operations must be performed smoothly and without jerking. If we are talking about bulky loads that can give a roll to the lift, then working manipulations at the points of loading and unloading should be performed with the preliminary installation of support elements that fix the extreme positions of the equipment.
Briefing for loaders
Each group of movers, which are determined by age and gender, has its own standard for carrying heavy loads. So, for male adolescents under 18 years old, the maximum will be 4 kg. For women - 10 kg, but no more than 2 sets per hour. Men over 18 can carry 50 kg at a time. But it is important to consider that these rules apply only in cases where work is performed on a flat horizontal surface without external interference. Also, regardless of the group of workers, it is not allowed to perform manual lifting to a height of more than 3 m. If several loaders carry the same object, then at least a 2-meter distance must be maintained between them. The safety of the loader in the warehouse and the use of a stretcher are allowed, but only at distances of up to 80 m. Commands for stopping and tipping over the device are given by a worker walking behind. Do not use stretchers or similar auxiliary devices for transportation on stairs. Turn over heavy piece goods and packed equipment, but only with the help of roller crowbars.
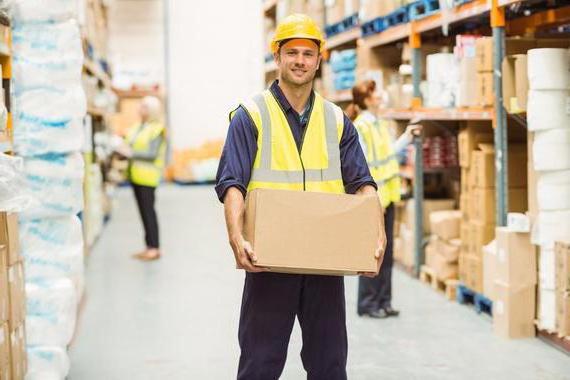
Briefing for pickers
The main tasks of workers in this profile include the selection of cargo units, their processing, sorting and stacking. It is not necessary that the picker alone carry out all these operations, but theoretically they may fall within the scope of his duties. In the process of forming the order, the worker can use devices for carrying goods, special grips on the manipulators and lifting equipment. In terms of performing manual actions, the picker is subject to the same safety training in the warehouse as in the case of the loader. In particular, the same restrictions apply to the masses of the transported weights. For staff involved in the collection of goods, special requirements are also imposed on clothing - it consists of combination gloves, jumpsuits and leather shoes. Often, pickers have to interact with workers performing related technological operations, so they need to know the basics of the same lifting process, signs and signals.
Instructions for electricians
Workers of this level carry out maintenance of hoisting equipment, electrical equipment, apparatus and some elements of engineering communications. Before starting work, the electrician receives an application in which general information about the equipment, possible causes of failure, signs of malfunction and other data that will help to carry out repairs in the shortest possible time should be indicated. After the completion of repair and restoration operations, the electrician writes the corresponding entry in his journal. With regard to working conditions, labor protection and safety measures at the warehouse in this part involve the complete removal of voltage and the implementation of responsible electrical measures with the participation of at least two people.
Conclusion
According to the regulations, each enterprise, based on general standards for maintaining security measures, can develop its own workflow instructions that focus on specific conditions. The specifics of the served cargo, the features of the technological processes of moving, the organization of storage, etc. are taken into account. For example, safety precautions at the finished goods warehouse impose increased requirements on fire safety equipment. Especially when it comes to the long-term content of flammable products. Also, a full list of rules for working with forklifts, crane manipulators and stackers applies to such objects. This is due to the fact that warehouses with finished goods are associated with different sales and production departments, requiring the use of a wide range of lifting and moving means.