Rolling machines are the most important equipment in obtaining metal in the form in which it is needed. They will be discussed in the article.
General information
Today, metal is the most common material from which a huge variety of things are made, from small household parts to large industrial facilities. However, there is a very important point that not everyone knows about. Just melting the metal, and after turning it into an ingot is not enough. After the formation of the ingot, any metal is transferred to the rolling mill. The only equipment that is available in such workshops is rolling machines. It is these devices that give the desired shape, which is suitable for the subsequent use of metal. It is worth noting that this equipment is one of the oldest to date. However, over the years of its use, the machine has proven itself on such a good side, has such good characteristics and productivity index that it is used to this day.
Machine tool
In fact, the device of the rolling machine is not complicated or difficult to maintain, assemble or repair. The sole purpose of this device is that it shapes metal ingots. In other words, large ingots arrive at the rolling mill, and while passing through the rolling mill it gives them the shape of a more familiar sheet metal. In order to achieve this effect, the design of the rolling machine has two rollers that constantly rotate towards each other. From the point of view of the technological process, this work is considered quite simple. In addition, the continuous improvement of technology has made it possible to make many improvements and modifications to the operation of this device. Thanks to these changes, currently all equipment of this type is able to work in fully automatic mode.
Rolling
A metal rolling machine has another very important function. It does not just shape the sheet. As the ingot passes through this machine, the metal becomes more uniform and more dense in structure. This is due to the fact that the rollers completely overwrite or close all cracks or empty spaces that could well have been formed on the ingot.
Another important point - the process of turning or rolling metal into a sheet form takes place in several stages and with the participation of several types of machines. Primary rolling are engaged in blooming and slabbing devices. It is worth noting that before sending the ingot for rolling to these machines, it needs to be slightly warmed up. Increasing the temperature of the metal will increase the ductility of the material during its rolling. If we talk about the performance of such machines, then it is huge. One machine can produce about 6 million tons of metal per year. This is taking into account the fact that the weight of ingots that are rolled can be in the region from 1 to 18 tons.
Blooming or slabbing
Before being rolled, the ingots are heated in special wells. The temperature that is maintained in such devices can reach 1800 degrees Celsius. After passing the well, an electric car is used, which, in fact, gives out a heated ingot for rental in blooming or slabbing. The difference between these machines is that blooming has only two rollers, while slabbing has four. It is important to understand that the passage of this stage and the processing process are only primary, since at the exit from blooming or slabing, the ingot still does not have a full form of sheet material. These units are designed to form bars. Depending on its shape and size, the resulting material is divided into blooms or slabs. An important note - the use of blooming or slabbing rolling machines is carried out only at those industrial facilities where the metal will subsequently be poured into molds.
General characteristics of the machine
Rolling mills - devices having smooth rollers through which metal is passed in order to give it a sheet shape. Currently, there is a huge range of these devices. The biggest difference between the machines is the shape of the rollers. For example, there is an aggregate that was originally made for rail production. The shape of its rollers during the manufacture of the machine was prepared specifically for this task. It is also important to understand that the machine has several pairs of rollers through which the metal passes. Constant progress has led to the fact that all types of devices are able to work in a constant automatic mode. The speed with which the stands pull the ingot through the machine can reach a record 290 km / h. The annual productivity of such a rolling mill reaches several million tons. Today, such units as foundry and rolling are gaining great popularity. The advantage is that they can act as a separate full-fledged production line, in contrast to conventional rolling mills.
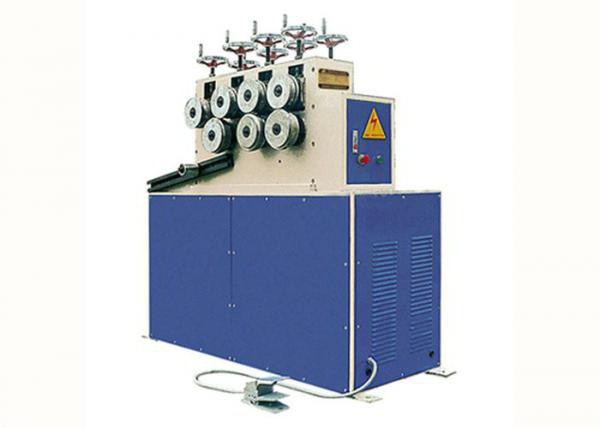
Currently, there are such types of machines as blanking, sheet, strip, high-quality, as well as some types capable of producing wire or beams.
Pipe rental
Another large category of rolling machines is designed to produce not sheet metal, but metal pipes. There are only three main types of pipe rolling mill that are currently in use. These include piercing, rolling and finishing machines.
If we talk about piercing mills, then they can have three different types of rollers used for rolling. There are barrel-shaped, mushroom-shaped and disk rollers. A device having the first type, that is, barrel-shaped, is characterized in that these machine elements have a double taper shape with a diameter of 450 to 1000 mm. Both parts are located in a horizontal plane, but on the vertical axis, you can adjust the feed angle from 5 to 18 degrees or more.
Screw rolling
A rolling machine for a profile pipe can also perform helical processing of metal. When performing this type of operation, double taper rolls in the metal create tensile and shear stresses. It is important to note that the radial stress of the workpiece can reach quite large values, which creates a cavity of small diameter, which has uneven walls. In order to get a hole with the required diameter and at the same time to avoid the presence of bumps, and to make smooth walls, it is necessary to carry out rolling on a mandrel. A mandrel is understood to mean a cone-shaped tool, which is located at the end of the shaft between the rolls along the path of movement of the metal workpiece. There is a special emphasis for fastening a rod with such a mandrel. When the metal moves forward, it is stitched with this frame, which passes through the hole, expanding and leveling it.
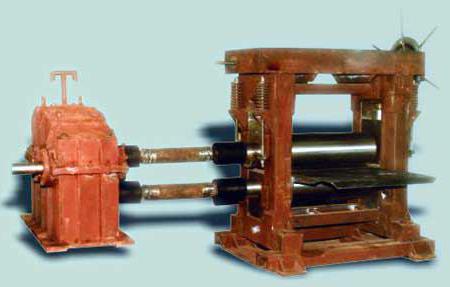
It is quite problematic to collect reviews on a rolling machine for a profile pipe, since such units are mainly used only by large enterprises. However, here the very use of these particular units already indicates that they work stably and well. In other words, conclusions can be drawn on the basis that all metal-working factories use such machines for a huge period of time. And this means that the presence of automatic mode and huge performance do their job. The disadvantages include the fact that the dimensions of such devices are quite large, and their stop and a new start is very problematic.
Thin tube rolling
It is worth noting that when passing the rental on piercing machines thick-walled sleeves are obtained. After passing through the processing on this device, the workpiece is transferred to a thin-tube rolling on such a device as:
- pilgrim;
- auto;
- continuous;
- three roll.
The name of each of these units is determined by the type of rolling mill that is used on this equipment.
Rolling and punching machine
The most famous manufacturer of this unit is Kadzama. This device is also called a roller press. The device of this thing is very simple, but it is intended for cutting cardboard, paper or plastic boxes for confectionery.
The advantages of this device include the fact that it pays off pretty quickly. The first 10,000 boxes is the approximate cost of one such machine. The cost of finished products, that is, boxes, is also very small. You have to pay only for the source material itself - cardboard. Working with this type of machine is very simple. All that is needed is just two things. First, a sheet of cardboard is put on the cutting knives, and then the feed handle turns. The dimensions of such a device are also quite small. You can even install it on a regular table.
How to make a rolling machine?
In order to make a rolling machine for the production of profiles, you will need 3 mandatory things - this is metal, bearings and a lathe. The design of the machine itself is also quite simple. The components of a one-piece rolling machine are a table to which a worm gear motor is attached. In addition, it is necessary to fix on the table another 7 additional acceptance stands. It is important to know that each cage consists of several components, and all of them are interlocked. That is, each crate is connected to the next. Another nuance concerns the rollers. In this model of the machine they are removable, and their fastening is carried out on the shafts. This type of arrangement and the type of rollers themselves opens up wide opportunities for the production of various profiles in terms of their dimensions, as well as the type of product. If there is such a desire, then you can put a new type of videos that will allow you to produce LSTK-profile. In order not to be mistaken in the manufacture, it is best to draw a drawing of the rolling machine before proceeding with its assembly.