The fuselage of a passenger plane links the wings, plumage and, in some cases, the landing gear. It is designed to accommodate equipment, crew, cargo. An airplane without a fuselage is called a flying wing. In its thickened compartment is everything that is in the body of a conventional apparatus. Let us consider in more detail what an aircraft fuselage is. A photo of this component will also be presented in the article.
General requirements
Explaining in two words what the fuselage of an aircraft is, we can say that this is the body of the device. This component of the aircraft has a number of requirements:
- Rational use of all internal volumes.
- Minimum drag.
- Providing sufficient visibility from the cockpit and crew room.
- Reliable heat and sound insulation and tightness.
- Ease of unloading / loading.
- Necessary ventilation, lighting and heating.
Outer form
The geometry of the aircraft fuselage is represented by an axisymmetric body with a smooth narrowing to the tail and nose. With this form, a minimum surface area is ensured for given dimensions. Accordingly, the mass of the casing is reduced, the resistance is reduced. Light weight gives certain advantages when exposed to overpressure in sealed cabs. However, for a number of reasons, such an ideal form is not respected. The smoothness of the contours is violated, in particular, by such elements of the fuselage of the aircraft as cabin lights, radar antennas. This, in turn, leads to an increase in resistance and an increase in mass. The same effect occurs when deviating from smooth forms in the tail compartments. In this case, the tipping angle is increased or the ramp and cargo hatch are shortened.
Loads
Explaining what the fuselage of the aircraft is (the photo presented in the article illustrates its features), it is necessary to say about the impacts it experiences. During landing and in flight, this component is affected by:
- Forces transmitted from attached components. These include, in particular, wings, landing gear, plumage, powerplant, etc.
- Massive inertial impact of equipment, cargo, units, which are located directly in it.
- Aerodynamic forces that are distributed over the surface.
- Inertial influence of own mass. It has the very design of the fuselage of the aircraft.
- Overpressure forces in equipment compartments, pressurized cabins.
All indicated loads are fully balanced. Considering what the aircraft fuselage is within the framework of structural mechanics, we can imagine it in the form of a box beam. In any section, horizontal and vertical forces, torque act on it. In sealed compartments, excessive internal pressure is added to them.
Module rationality
The most optimal is considered such a scheme of the fuselage of the aircraft, in which he will be able to absorb all of the above loads with a sufficiently small dead weight. The thin-walled shell in this case is fixed on the power frame. Rationality is ensured by the full use of the skin. In the place where the fuselage is located near the aircraft, there are local aerodynamic forces, internal overpressure, general power work. Thin-walled shell, reinforced by the inside of the frame, maximally satisfies the requirements of ease of layout, provides technological simplicity, operational characteristics. Such an aircraft fuselage device is called beam. Previously used truss modules. They significantly lost the beam in their mass. What is a truss plane fuselage? Sheathing in this case is completely excluded from power work. She perceives only local aerodynamic loads. If we talk about what the aircraft fuselage is in this case, then it can be defined as an additional module that increases the total mass of the device. Spatial farm significantly complicates the layout of the cargo. The disadvantages of this module have led to the fact that they are practically not used in modern aircraft construction. Their use is advisable only on low-speed light aircraft of small aircraft.
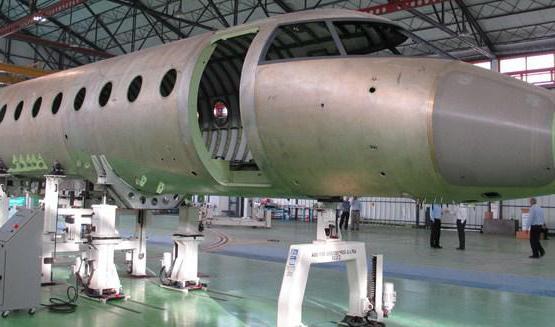
Classification
There are three types of airplane fuselages:
- Casing.
- Spar.
- Stringer.
The last two differ from each other in shape and cross-sectional area. The longitudinal set in the place where the fuselage is located on the aircraft consists of stringers and spars. The sheathing module in cross section includes frames. They ensure the preservation of a given shape during shell deformations and the transfer of concentrated and distributed loads. In the place where the aircraft has a fuselage, there are areas in which there may be a large concentration of forces. To prevent deformation in these cases, reinforced frames are installed. In beam modules, the impact of any direction is perceived completely by the skin. A tangential flow of effort arises in it. Their distribution depends on the direction of the external action and the cross-sectional shape of the module. Sheathing also fully perceives torque. In this case, the tangent flow is evenly distributed around the perimeter. The shell in this case, as a rule, has a single-closed contour in cross section. In areas where cutouts are present in the shell, force trims are installed . They provide the transfer of all efforts in these areas.
Stringers and spars
The longitudinal parts of the fuselage of an airplane usually extend along its entire length. Together with the casing, they accept normal bending forces. The manufacture of simple stringers and spars is carried out, as a rule, from bent or extruded profiles with different sections. Longitudinal elements have greater rigidity. At high loads, in some cases, composite spars can be installed. They include several profiles connected to each other. When edging large cutouts, beams are used - longitudinal elements of the box section. They are made of extruded profiles, which are interconnected by sheathing and walls.
Frames
They can be reinforced or regular. The latter ensure the preservation of the cross-sectional shape of the module. Reinforced frames are used in areas with large loads on the hull. There are nodes on them, joining aggregates, securing cargo, large equipment, engines, etc. Reinforcement is also installed along the boundaries of large cutouts in the body. Conventional frames have, as a rule, a frame structure. They are made of stamped or flexible sheet. Reinforced elements are performed in the form of a closed frame of a channel or I-section. The tangent flow acts as a supporting reaction. The frame distributes the external impact along the entire perimeter. She herself acts on a bend. He determines its cross section. The design of such a frame is monolithic or prefabricated. In areas of the installation of partitions, the reinforced frame is completely sewn up with the wall. It is supported by horizontal and vertical profiles. Sheathing of the frame can also be carried out with a spherical shell. The reinforcing elements are arranged radially.
Sheathing
It is made of metal sheets. They are formed along the profile of the surface of the body and fixed. The joints of the sheets are located on the transverse and longitudinal parts of the module. For cladding frames, monolithic rib panels are used. Recently, the use of composite materials has been quite common.
Component connection
Sheathing can be attached to frames or stringers or at the same time to both. The first option is used in cladding modules. When fixing only to stringers, rivet longitudinal seams are used. There is no transverse connection. This improves the aerodynamic properties of the module. But in this case, at lower loads, the skin loses its stability. This leads to an increase in the weight of the structure. To prevent this, the shell is often associated with a frame compensator - an additional pad.
Joints
When the beam-spar fuselage scheme, they are performed using nodes that are located exclusively on the longitudinal parts. Such joints are called point joints. Contour joints are used in beam-stringer fuselages. Joints are placed around the entire perimeter of the frame with obligatory enhanced binding of the skin and stringers. Connections in such fuselages are usually made using flanges. Such a joint provides power communication with parts in contact along the contour.
Attachment Mounting
Connection nodes are installed on reinforced frames. They act as a hard drive. Due to them, the distribution of concentrated longitudinal loads is carried out. Butt joints must communicate with the power side members. To reduce the weight of the entire fuselage structure, it is advisable to reduce the number of reinforced frames. On each such element several nodes of fastening of units can be located.
Wings
A specific feature of the fastening of these parts is the balancing of bending moments at this junction of the wing consoles. Balancing the right and left elements on the center wing passing through the fuselage will be considered rational. For the spar type of the module, it is enough to skip the longitudinal elements - they will be used to balance the bend. To connect monoblock and caisson wings, all power panels must pass through the body. If, for some reason, the passage of elements through the fuselage cannot be carried out, bending moments on the right and left should be locked on the power frames. Such a solution, however, can be applied to the side members of the wings, since the number of parts in them is small. Monoblock and caisson components will require more reinforced frames. It is quite difficult to perform on the design. In such cases, it is advisable to use the spar scheme.
Keel
Its fastening requires the mandatory transfer of bending moment to the fuselage. To do this, each longitudinal element of the keel is connected to a reinforced frame. If possible, you can use the mast type of the spar bookmark at two points. They are positioned along the height of the frame. The arrow-shaped longitudinal element has a kink at the intersection with it. This requires the installation of additional gain. It can be abandoned if the frame is positioned obliquely relative to the axis of the fuselage so that the plane becomes an extension of the side member wall. But the embodiment of this option will be accompanied by certain difficulties.
Cutouts
The central part of the fuselage of the aircraft includes openings for windows, doors, hatches, lights, landing gear niches. All these cuts violate the closed contour of the skin. Accordingly, the stability and strength of the frame is significantly reduced. To compensate for losses along the contours of the holes, a rigid frame edging is passed. With small cutouts, it is a monolithic design. It is made of a sheet made by stamping or otherwise. Large holes are edged at the ends with reinforced frames. Beams are installed in the longitudinal direction. However, they do not end within the notch, but go beyond the reinforced frames. This ensures a rigid laying of the longitudinal parts. The chassis niches are fixed on reinforced frames and spars in the lower part of the body.
Hermetic cabins
When flying at high altitude, excessive pressure is maintained in them. To ensure the minimum weight of pressurized cabins, they are made in the form of a sphere or cylinder with spherical bottoms. In this case, it is necessary to strengthen the frame located at the junction of the segments. This is required because it accepts a rather large compressive load. In pressurized cabs, the casing does not experience bending deformations when loaded with excessive pressure. It works exclusively in tension. In some cases, you have to retreat from the specified form. This, in turn, leads to an increase in the weight of the entire structure. Flat panels are used to provide the necessary bending stiffness. Being under the influence of excessive pressure, they are supported by transverse and longitudinal beams (ribs). To enhance the rigidity of the parts, the panels are made in the form of three-layer structures. In the cabs, reliable sealing must be ensured along all bolted and riveted joints. For this, special tapes are used. They are impregnated with sealant, coated with a non-drying mastic, coated with special formulations, followed by drying. At the joints of the sheathing sheets, rivet multi-row seams with a small pitch are used. Hatches, windows, lights, doors are especially carefully treated with sealant. Sealing is ensured through the use of special sealing means. It can be rubber bands, tapes, inflatable tubes, gaskets.
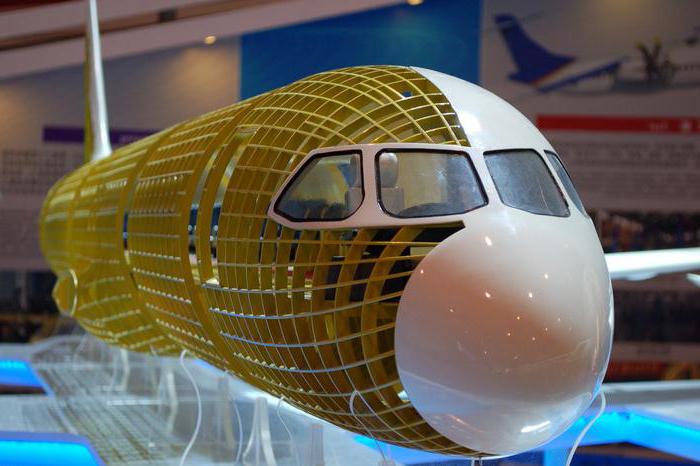
Mandatory events
To ensure compliance with the requirements for the aircraft fuselage, certain actions must be performed. These include:
- The choice of such values ββof parameters and external forms of the hull, in which the drag will be reduced to a minimum, and the net volume, respectively, will be optimal.
- The use of supporting fuselages. Due to them, a significant lifting force is created. Due to this, it is possible to reduce the weight and area of ββthe wing.
- Rational use of useful volumes. This is achieved by increasing the density of the layout, compact placement of the cargo in the region of the center of mass. In this case, mass moments of inertia will decrease and maneuverability characteristics will improve. Narrowing the range of alignment changes during fuel burnup, different loading options provides greater stability and better handling.
- Coordination of power schemes of the fuselage and units attached to it. At the same time, there should be reliable fastening, balancing and transfer of loads from the power parts of the wing, landing gear, plumage, installations to the body.
- Ensuring the convenience of entry / exit of the crew, passengers, mooring, loading / unloading of items, equipment, things intended for transportation.
- Providing a convenient approach to different units. This is mainly necessary for inspection and repair.
The necessary conditions must be created for the crew and passengers, as well as an appropriate level of comfort during the flight at high altitudes. A mandatory requirement is the provision of sound and heat insulation of the cabs, the possibility of safe and quick emergency exit from the cabin. Comfortable conditions should also be created for the crew. In particular, pilots should be provided with good visibility, flight comfort and control.