Anodizing is an electrolytic process that is used to increase the thickness of a layer of natural oxides on the surface of products. This technology got its name due to the fact that the processed material is used as an anode in the electrolyte. As a result of this operation, the resistance of the material to corrosion and wear is increased, and surface preparation for the use of a primer and paint is also provided.
The application of additional protective layers after anodizing the metal is carried out much more qualitatively in comparison with the starting material. The anodized coating itself, depending on the method of its application, can be porous, well absorbing dyes, or thin and transparent, emphasizing the structure of the starting material and reflecting light well. The formed protective film is a dielectric, that is, it does not conduct electric current.
Why is this done?
Anodized coating is used where it is required to provide protection against corrosion and to avoid increased wear in the adjoining parts of mechanisms and devices. Among other methods of surface protection of metals, this technology is one of the cheapest and most reliable. The most common use of anodizing is to protect aluminum and its alloys. As you know, this metal, having such unique properties as a combination of lightness and strength, has an increased susceptibility to corrosion. This technology has been developed for a number of other non-ferrous metals: titanium, magnesium, zinc, zirconium and tantalum.
Some features
The studied process, in addition to changing the microscopic texture on the surface, also changes the crystalline structure of the metal at the border with the protective film. However, with a large thickness of the anodized coating, the protective layer itself, as a rule, has significant porosity. Therefore, to achieve corrosion resistance of the material requires its additional sealing. At the same time, a thick layer provides increased wear resistance, much greater in comparison with paints or other coatings, for example, by spraying. Together with an increase in surface strength, it becomes more fragile, that is, more susceptible to cracking from thermal and chemical effects, as well as from shocks. Cracks in the anodized coating during stamping are by no means a rare occurrence, and the developed recommendations here do not always help.
Invention
The first documented use of anodizing occurred in 1923 in England to protect seaplane parts from corrosion. Initially, chromic acid was used. Later, oxalic acid was used in Japan, but today, in most cases, classical sulfuric acid is used to create an anodized coating in the electrolyte, which significantly reduces the cost of the process. Technology is constantly being improved and developed.
Aluminum
Anodized coating is performed to increase corrosion resistance and preparation for painting. And also, depending on the technology used - either to increase the roughness, or to create a smooth surface. Moreover, anodizing in itself is not able to significantly increase the strength of products made from this metal. Upon contact of aluminum with air or any other gas containing oxygen, the metal naturally forms an oxide layer 2-3 nm thick on its surface, and on alloys its value reaches 5-15 nm.
The thickness of the anodized coating of aluminum is 15-20 microns, that is, a difference of two orders of magnitude (1 micron is 1000 nm). Moreover, this created layer is distributed in equal shares, relatively speaking, inside and outside the surface, that is, it increases the thickness of the part by ½ of the size of the protective layer. Although anodizing produces a dense and even coating, the microscopic cracks present in it can lead to corrosion. In addition, the surface protective layer itself is subject to chemical decomposition due to exposure to high acidity conditions. To combat this phenomenon, technologies are used that reduce the number of microcracks and introduce more stable chemical elements into the oxide composition.
Application
The processed materials are used very widely. For example, in aviation, many structural elements contain the studied aluminum alloys, the same situation in shipbuilding. The dielectric properties of the anodized coating predetermined its use in electrical products. Products made from processed material can be found in various household appliances, including players, lights, cameras, smartphones. In everyday life, an anodized coating of the iron is used, more precisely - its soles, which significantly improves its consumer properties. When cooking, you can use special Teflon coatings to avoid burning foods. Usually such kitchen utensils are quite expensive. However, an uncoated aluminum frying pan is able to provide a solution to the same problem. At the same time with less money. In construction, anodized coating of profiles is used for the installation of windows and other needs. In addition, multi-colored details attract the attention of designers and artists, they are used in various cultural and art objects around the world, as well as in the manufacture of jewelry.
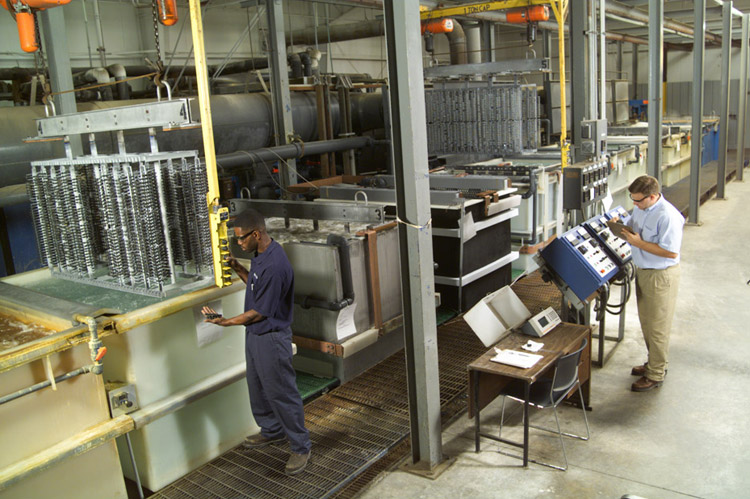
Technology
To carry out work on an industrial scale, special galvanic workshops and manufactures are created that are considered "dirty" and harmful to human health. Therefore, recommendations for conducting the process at home, advertised in some sources, should be taken with extreme caution, despite the apparent simplicity of the described technologies.
Anodized coating can be created in several ways, but the general principle and sequence of work remains classic. In this case, the strength and mechanical properties of the obtained material depend on, in fact, the starting metal itself, on the characteristics of the cathode, current strength and composition of the used electrolyte. It must be emphasized that as a result of the procedure, no additional substances are applied to the surface, and a protective layer is formed by converting the starting material itself. The essence of electroplating is the effect of electric current on chemical reactions. The whole process is divided into three main stages.
Stage One - Preparation
At this stage, the product is thoroughly cleaned. The surface is degreased and sanded. Then the so-called etching occurs. It is carried out by placing the product in an alkaline solution followed by transfer to an acid solution. Flushing completes these procedures, during which it is extremely important to remove all residual chemicals, including hard-to-reach areas. The final result largely depends on the quality of the first stage.
The second stage - electrochemistry
At this stage, anodized aluminum coating is actually created. A carefully prepared blank is hung on brackets and lowered into a bath with electrolyte, located between two cathodes. For aluminum and its alloys, cathodes made of lead are used. Typically, the composition of the electrolyte includes sulfuric acid, but other acids can be used, for example, oxalic, chromic, depending on the future use of the machined part. Oxalic acid is used to create insulating coatings of different colors, chrome acid - for the processing of parts having a complex geometric shape with holes of small diameter.
The time required to create a protective coating depends on the temperature of the electrolyte and on the strength of the current. The higher the temperature and the lower the current, the faster the process. However, in this case, the surface film is quite porous and soft. To obtain a solid and dense surface, low temperatures and high current density are required. For sulfate electrolyte, the temperature range is from 0 to 50 degrees, and the specific current strength is from 1 to 3 Amperes per square decimeter. All parameters for this procedure have been worked out for years and are contained in the relevant instructions and standards.
The third stage - consolidation
After completion of the electrolysis, the product having an anodized coating is fixed, that is, the pores in the protective film are closed. This can be done by placing the treated surface in water or in a special solution. Before this stage, effective painting of the part is possible, since the presence of pores will ensure good absorption of the dye.
The development of anodizing technology
To obtain a heavy-duty oxide film on the surface of aluminum, a method was developed for using a complex composition of various electrolytes in a certain proportion in combination with a gradual increase in the electric current density. A peculiar “cocktail” of sulfuric, tartaric, oxalic, citric and boric acids is used, and the current strength in the process gradually increases by five times. Due to this effect, the structure of the porous cell of the protective oxide layer changes.
Separately, mention should be made of the technology for changing the color of the anodized object, which can be done in different ways. The simplest is to place the part in a solution with hot dye immediately after the anodizing procedure, that is, before the third stage of the process. The staining process using additives directly into the electrolyte is somewhat more complicated. Additives are usually salts of various metals or organic acids, allowing you to get the most diverse range of colors - from absolutely black to almost any color from the palette.