Steel products, even against the background of the active distribution of high-strength plastics, retain their market position. Carbon alloys with different characteristics are used in instrument and automotive manufacturing, construction and manufacturing. The unique combination of elasticity and strength makes the material profitable from the point of view of long-term operation. Accordingly, the products last longer and cost less to maintain. But this is not all the advantages that steel has. The production of steel using modern technology allows you to give the metal structure and additional properties.
General information on production technologies
The main task of the technologist is to provide a process in which the content of carbon and all kinds of impurities, such as sulfur and phosphorus, are reduced in the workpiece. The basis for the workpiece is cast iron. It is worth noting that furnaces for the production of cast iron appeared in the Middle Ages, while the first production of steel was realized only in 1885, and to this day alloy production methods are developed and improved. The differences in the approaches to the process are mainly due to the method of carbon oxidation.
Cast iron is used as the starting material. It can be applied in solid or molten form. Iron-containing products, the preparation of which was carried out by direct reduction, can also be used. Almost all methods for producing steel in one form or another also involve the process of refining from impurities. For example, converter technology provides oxygen blowing.
Converter method
With this method, molten cast iron, as well as impurities and waste in the form of ore, scrap metal and flux, can be used as the basis. Compressed air is supplied through the technological holes to the prepared base, contributing to the implementation of chemical reactions. Also involved in the process is the thermal effect, in which oxidation of oxygen and impurities occurs. Of particular importance are the characteristics of the furnace structure in which steel is processed. Steel production can occur in units with different lining - the most common methods of protecting structures with refractory bricks and dolomite mass. According to the type of lining, the converter method is also subdivided into two other methods: Thomas and Bessemer.
Thomasovsky way
A feature of this method is the careful processing of cast iron containing up to 2% phosphorus impurities. As for the lining technique, it is implemented using calcium and magnesium oxides . Thanks to this solution, slag-forming elements are endowed with an excess of oxides. The phosphorus combustion process is one of the key sources of thermal energy in this case. By the way, the combustion of 1% phosphorus filling increases the temperature of the furnace by 150 ° C. Thomas alloys are characterized by a low carbon content and are most often used as technical iron. Subsequently, wire, roofing iron , etc. are made from it. In addition, the production of steel (cast iron) can be used to produce phosphorous slag for the purpose of further use as fertilizer on soils with high acidity.
Bessemerian way
This method involves processing the basics, which contain a small amount of sulfur and phosphorus. But at the same time, a high silicon content is also noted - about 2%. In the process of blowing, oxidation of silicon first of all occurs, which contributes to intensive heat generation. As a result, the temperature in the furnace rises to 1600 ° C. Iron oxidation also occurs intensively as carbon and silicon are burned. In the Bessemer method, the process for producing steel involves the complete transition of phosphorus to steel. All reactions in the furnace go quickly - on average 15 minutes. This is due to the fact that oxygen, blown through a cast-iron base, reacts with the corresponding substances throughout the volume. Finished steel may contain a high concentration of iron monoxide in dissolved form. This feature relates to the disadvantages of the process, as the overall quality of the metal decreases. For this reason, technologists recommend deoxidizing the alloys before casting using special components in the form of ferromanganese, ferrosilicon or aluminum.
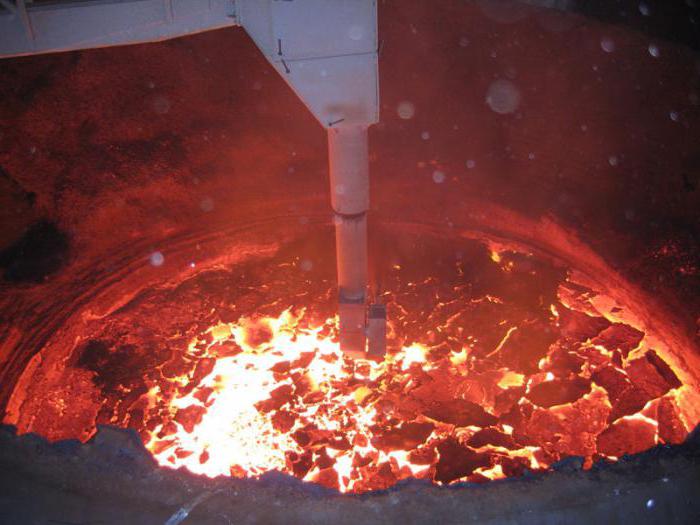
Getting in open-hearth furnaces
If in the case of the converter method of manufacturing metal, it is envisaged to provide burning with air oxygen, then the open-hearth method requires the inclusion of iron ore and rust scrap in the technological process. Iron oxide oxygen is formed from these materials, which also contributes to carbon burnout. The furnace itself includes a melting bath, which is closed by a heat-resistant brick wall, as the basis of the design. Several chambers of regenerators are also provided, providing preliminary heating of the air mass and gas. The regenerating blocks are equipped with special nozzles made of fire-resistant bricks.
Like converters, open-hearth furnaces operate periodically. As the laying of new batches of the mixture, that is, the cast-iron base, steel is phased in. Steel production is slow, since the processing of cast iron takes about 7 hours. But then the martens allow you to adjust the chemical properties of the alloy by adding iron additives in different proportions - ore and scrap are used for this. At the final stage of metal formation, the furnace stops working, the slag is drained, and then a deoxidizer is added. By the way, alloyed steels can also be obtained in such a furnace .
Electrothermal method
To date, the electrothermal production of steels is considered the most effective. So, in comparison with open-hearth furnaces and a converter, this technique provides the possibility of more precise control of the quality of steel - including through regulation of the chemical composition. Of particular note is the interaction of the furnace chambers with the air. The electrothermal technology for producing steel provides minimal access to air, causing other advantages. For example, this allows to minimize the accumulation of iron monoxide and foreign particles in the alloy, as well as to provide more efficient burnout of phosphorus and sulfur.
High temperature conditions at the level of 1650 ° C make it possible to melt problematic slags that require thermal treatment at increased capacities. Also in electric furnaces, it is possible to alloy steel using refractory metals, including tungsten and molybdenum. However, there is a serious drawback of this method of obtaining steels. Used furnaces require large amounts of energy, which makes this process the most expensive.
Dependence of metal properties on elemental base
The performance of steel is determined by the set of chemical elements that the alloy was endowed with during the manufacture. One of the key components due to which this metal acquires its basic properties in the form of hardness and strength is carbon. The higher it is, the more reliable the steel. Manganese and silicon do not have a special effect on the quality of the material, but their use is necessary in the manufacture of certain steel grades to perform the deoxidation process. Sulfur and phosphorus have a negative effect on the formation of the product. Depending on the technique used to obtain the composition of the steel may have different concentrations of these elements. In any case, sulfur increases the fragility of the metal, and also reduces the properties of strength and ductility. Phosphorus, in turn, gives the steel cold-brittleness, which during operation can be expressed by brittleness.
Steel Processing Techniques
Not always the process of the final formation of the metal structure is completed after the main receipt. In the future, in order to improve the characteristics of the product, additional processing means can be used. These include deformation methods in the form of forging, stamping and rolling. This helps, even at the production stage, to form a set of necessary technical properties that finished steel will possess. The production of steel at the exit gives a plastic structure, and therefore the technologies of primary processing are quite diverse. So, in addition to deformation, methods of hardening, annealing and normalization can be applied.
Conclusion
Steel is associated with reliability and durability. In the case of quality products of this kind, such characteristics are justified. For example, individual brands provide fairly high qualities of strength and elasticity. Depending on the technology by which the preparation was carried out, the use of steel can be oriented towards maintaining hardness, the ability to withstand dynamic loads, etc. The most favorable metal from the point of view of technical and operational properties makes it possible to obtain an electrothermal method. But at the same time, it is also the most expensive, therefore, they resort to this technique only in special cases - to create special steels.