The liquefaction of natural gas is called its conversion into a liquid state under the influence of temperatures that are lower than critical. This process makes it possible to reserve and save it for future use, as well as for organizing transportation by any means of transport. The substance is often used in the form of alternative fuels in motor vehicles, in metal processing, in mobile power plants and so on. In addition, in many private homes you can find a boiler for liquefied gas. The costs of creating facilities for its production depend on the location of the development, as well as the type and composition of the extracted raw materials. Now the most promising of them are considered floating, since transportation through the construction of underwater gas pipelines is often unrealistic.
Preparation and start of liquefaction
The technological schemes of those plants used for liquefaction differ from one another, primarily, in the refrigeration cycle. His choice is primarily affected by the composition and pressure of the gas that comes here. These parameters, in turn, are influenced by several factors, including: time of year, place of production, and even the term for its development. Before you begin to liquefy gases and send to the installation, it is necessary to clean them from acidic impurities and drain. At the initial phase of the process, hydrocarbons are massively released from the raw materials, including high-boiling naphthenic, aromatic and paraffinic. Otherwise, clogging of the fittings and equipment of the plants may occur. In order to efficiently and efficiently liquefy gases, it must be remembered that a large amount of heavy hydrocarbons in their composition leads to a high liquefaction temperature and low energy costs. If nitrogen is present in their composition, then this leads to an increase in evaporation and energy consumption.
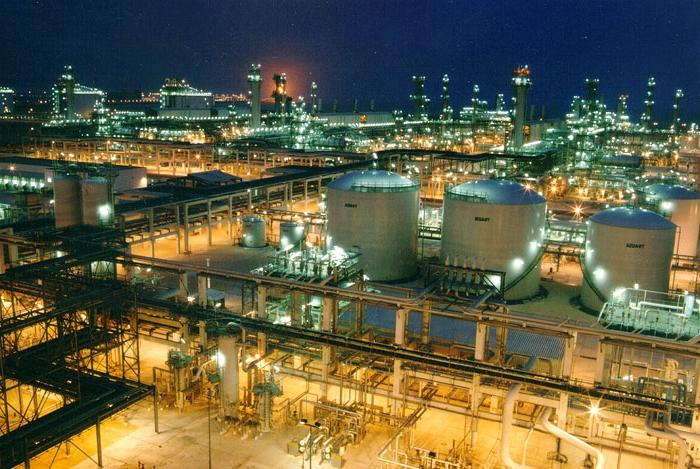
Cascade method and refrigeration cycles
Industrial liquefaction methods are based on the principle of liquid evaporation, the adiabatic gas expansion process , and the Joule-Thomson effect. Liquefied natural gas is produced through the use of several refrigeration units (hence media). In this case, the medium, which is characterized by a lower boiling point, condenses under pressure due to the evaporation of a more boiling neighboring one. This method is the most common and is known as cascade liquefaction. In most cases, propane (sometimes ammonia) acts as a refrigerant in the first stage, and ethylene in the second. Thus, the liquefaction of natural gas is carried out in this case under the influence of evaporated ethylene. As for the refrigeration cycles, which are based on the Joule-Thomson effect mentioned above, among them they are distinguished with both single and double throttling, as well as with preliminary cooling due to a special flow and an extraneous agent.
Large unit liquefaction
Gases can also be liquefied by using a single-threaded cascade cycle. Here, the refrigerant is a multicomponent mixture, which includes nitrogen with hydrocarbons. This method, together with its modifications, is most often used in large plants, the productivity of which is from two to five million cubic meters of the finished product per day. Liquefying gases in this way is beneficial in terms of relatively low energy costs. On the other hand, a single-threaded cascade cycle requires a large amount of metal-intensive equipment.