Man has always sought to decorate his home and make it practical. For these purposes, he uses various materials, many of which remain relevant for millennia. So, the first prototypes of ceramic tiles were found at the excavations of the Euphrates and the Interfluve of the Tiger. In ancient times, this material was used to decorate the walls of temples and houses of nobility. Over time, its popularity grew, and manufacturing methods improved. Let's get to know the modern technology of ceramic tile production and find out how it has earned such an impeccable reputation.
Structure
The first step is to figure out what ceramic tiles are made of. The main raw materials used in the manufacture of ceramics are represented by the following materials:
- Clay materials. They give the wet mass the plasticity necessary for forming blanks.
- Quartz materials (mainly sand). Perform a structural function, that is, create a "skeleton" of the product. They allow you to limit and control the change in product dimensions, which inevitably accompanies the firing process.
- Materials containing feldspars (aluminosilicates or carbonates of potassium, sodium, calcium, and so on). With their help, when firing the product, its structure remains dense and glassy.
The process of manufacturing ceramic tiles consists of the following stages:
- Mixing materials.
- Molding.
- Drying.
- Glaze application.
- Burning.
- Sorting.
At each stage we will dwell separately.
Mixing materials
It all starts with the extraction of materials, but we will not consider it, since we are interested in the process of manufacturing ceramic tiles. First of all, clay is mixed with other components in strictly calculated proportions. The finished mixture goes to the preliminary grinding, where it is subjected to grinding and moistening.
The method of preparation of the ceramic mass depends on the properties of the feedstock and the desired product. There are such ways:
- Semi-dry. The components are first crushed, then slightly dried, crushed, mixed and sent to molding. This method is called semi-dry because the components themselves have a certain degree of humidity.
- Plastic. Clay is crushed and sent to a mixer, where it is mixed with additives and takes the form of a homogeneous plastic mass.
- Wet. The materials are ground and mixed with the addition of water (up to 60%). A homogeneous liquid mixture is fed into special tanks.
Regardless of which ceramic tile production line is used, to obtain a good product, it is necessary that all materials are carefully crushed and mixed.
Molding
Forming is carried out in two ways: pressing and extrusion. In the first case, special presses compress the powder mass in two directions. Under high pressure, the granules are densified and partially deformed. Due to this, the tile acquires the appropriate density and strength.
When using the extrusion method, the tile is made from a pasty mass, which is molded by forcing through the holes of the extruder. This method differs from dry pressing by the presence of a liquid phase in the production process. Due to the fact that the viscous mass is squeezed out of the apparatus and cut off, it is possible to produce products of various shapes. Ceramic tiles made by extrusion may be convex or concave. When pressing, only the size of the products can be varied.
Drying
An obligatory stage in the technology of ceramic tile production is drying. At this stage, moisture that was necessary for comfortable molding is removed from the finished molds. Drying conditions play a crucial role in ensuring the integrity and strength of the future product, so they are strictly controlled. In modern tile manufacturing enterprises, drying plants are used that douse raw (molded wet product) with hot air. Heating leads to the formation of moisture on the surface of the semi-finished product, which quickly evaporates and is removed by the ventilation system.
Good heat transfer, efficient ventilation and high air temperature ensure the speed of the installation. If the raw is fired, bypassing the drying stage, then it will crack. At the final stages of drying and during the firing process, the tile shrinks, that is, a proportional decrease in its linear dimensions. This explains the need for calibration of finished products. The higher the level of the enterprise, the greater the likelihood that its products will have the same size. Therefore, it is better to choose mid-range options (for example, from the Shakhty Ceramic Tiles, Euroceramics, Sokol, etc.) companies than to get an uneven wall.
Glaze application
Glaze (enamel) - a vitreous coating that is applied to the front side of the tile and fixed in the firing process. Glazing is performed to decorate and strengthen the product. The composition of the glaze may include various materials and compounds (sand, oxides, frits, coloring pigments, etc.). It can be glossy and matte, color and plain, and sometimes even transparent. Coloring is achieved by adding metal oxides and salts to the composition (iron red, chromium green, cobalt blue, etc.). The enamel has a glassy structure and differs from the base of the ceramic not only in appearance but also in characteristics, the most important of which is water resistance.
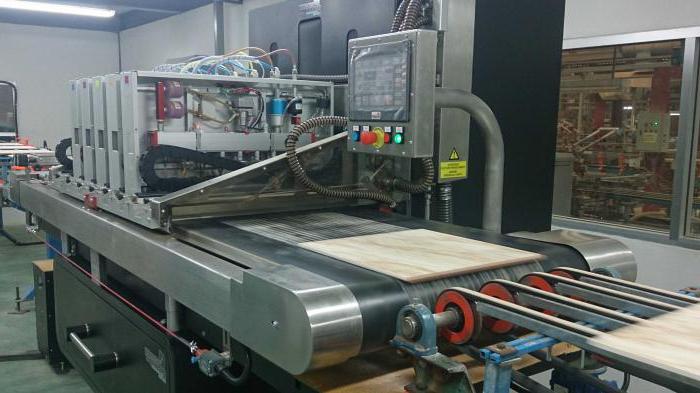
Today, a ceramic tile factory can use dozens of methods for applying glazes to its products. Enamel can be used in the form of a sprayed suspension, paste or granules. In the basic version, it is applied to molded workpieces using a large round drum, which, making one circle, processes several tiles at once. Application can be made before or after firing, and in some cases, even during firing.
In order for the product to have a more aesthetic appearance, the enameling process can be accompanied by the application of an image. Ceramic tiles with a pattern are much more popular than plain. So that each tile has a unique image, but retains the style of the series, the drum is simply shifted along the axis of rotation. Of course, this applies to models with abstract pictures.
Burning
Ceramic tiles are fired in order to make them sufficiently solid and durable. This happens due to chemical and physical changes in the composition of the material and glaze, which pass under the influence of high temperatures. Typically, ceramic tile manufacturers use continuous furnaces for this purpose. In fact, such a furnace is a tunnel, moving along which with the help of a special conveyor, the tile lends itself to preliminary heating (allows you to get rid of residual moisture), and then firing.
A characteristic property of clay is its ability to transform during firing into a strong stone-like mass. Depending on the type of product, the firing temperature ranges from 900 to 1300 ° C. After spending a certain time in the furnace, the tile is subsequently cooled to a temperature at which, without compromising quality, it can be unloaded from the furnace.
Sorting
Before entering the packaging line and warehouse, the finished tile is carefully sorted. This procedure allows you to solve three problems:
- Discard products with defects.
- Separate first grade tile from lower grade tile.
- Group batches by grade and color.
Typically, manufacturers of ceramic tiles sort as follows - after leaving the oven, it passes through three sections: flaw detection, calibration, and visual inspection. To identify defects, each product is fed to the rails and rolled with a roller. Due to the fact that the rails are located at the edges of the tile, and the roller presses into the center, the defective samples break, unable to withstand the load. Paint defects are checked visually, together with the definition of tonality. It remains only to sort the products in batches and send them to the warehouse.
As you can see, the technology for the production of ceramic tiles is quite simple. However, in order to obtain a high-quality product, it is necessary to approach each stage with full responsibility and compliance with all technological rules. That is why many aspiring entrepreneurs who have opened a ceramic tile factory cannot achieve the proper quality of their products. Now we will briefly find out what properties ceramic tile should have.
Wear resistance
Of course, this is one of the most important qualities of floor tiles, as it characterizes its resistance to abrasion and the ability to maintain an attractive appearance after prolonged use. Despite the fact that the material as a whole is quite durable, its type should be selected depending on the operating conditions. So, designed for a simple bathroom, floor ceramic tiles with a pattern, laid in a public toilet, will quickly wipe off and lose their appearance.
Water absorption
Water absorption is the ratio of the mass of water absorbed by a tile when it is completely submerged under water to the mass of a dry product, expressed as a percentage. For glazed floor tiles , it should not be higher than 3%. For wall brands, this figure rises to 10%. In this regard, for facing pools, for example, far from any tile. Large manufacturers, for example, the Shakhtinskaya Ceramic Tile enterprise, can produce various types of specialized products at their facilities, from tile for bathtubs to ceramic for pools.
Frost resistance
As well as water absorption, this property depends on the porosity of the product. Regardless of production technology, pores remain in the ceramic tile into which moisture can penetrate. As you know, when freezing, water increases in volume. The ability of tiles to withstand moisture, withstand frequent alternate freezing, is called frost resistance. This indicator is important when choosing an external finishing material. The smaller the pores in ceramics, the lower the rate of its water absorption, and the higher the rate of frost resistance.
Slip resistance
As you might guess, this property determines the ability of tile enamel to prevent the sliding of objects on it. This requirement is important for flooring residential and industrial premises, especially those in which it is always humid. In pools and saunas, ribbed tiles are most often used, which have increased resistance to slipping.
Chemical resistance
This is the name for the characteristic of tile enamel, which reflects its ability to tolerate contact with chemicals (acids, bases, household chemicals, additives for disinfecting water in swimming pools, etc.). Tiles should not undergo external changes under the aggressive influence of these substances. By the way, considering the resistance of ceramics to various influences, one should not forget that the joints between the tiles can also be subject to destructive effects. To avoid this, they are covered with protective compounds.
Strength limit
This indicator expresses the level of permissible load that ceramic tiles can withstand. Usually it is directly proportional to the thickness of the product. The ability to withstand the load is important mainly for floor tiles.
Surface hardness
This characteristic illustrates the surface's resistance to damage and scratches. It is especially important for floor tiles. Surface hardness is determined by the quality and composition of the glaze. It is noteworthy that on a shiny surface, mechanical damage is much more noticeable than on a matte surface.