Metals and alloys have entered our lives so closely that sometimes we don’t even think about them. As early as 4-3 millennia BC, the first acquaintance of a person with nuggets occurred. A lot of time has passed since then, and every year metal processing has only improved.
A large role was played by such a metal as zinc. Alloys based on it are used in many industries. In this article we will consider zinc alloys and their role in our lives.
Transition metal
Zinc is known to be a bluish-white brittle transition metal. It is extracted from semimetal ores. The process of obtaining pure zinc is quite complex and time-consuming. First of all, ore containing from 1-4% zinc is enriched with selective flotation. Through this process, concentrates (55% Zn) are obtained. Next, you need to get zinc oxide. For this, the concentrates obtained are fired in fluidized bed furnaces. Only from zinc oxide can this metal be obtained in its pure form, and there are two methods for this.
Zinc production
The first is electrolytic, based on the treatment of zinc oxide with sulfuric acid. As a result of this reaction, a sulfate solution is formed, which is purified from impurities and subjected to electrolysis. Zinc is deposited on aluminum cathodes, which are then melted in induction furnaces. The purity of zinc thus obtained is about 99.95%.
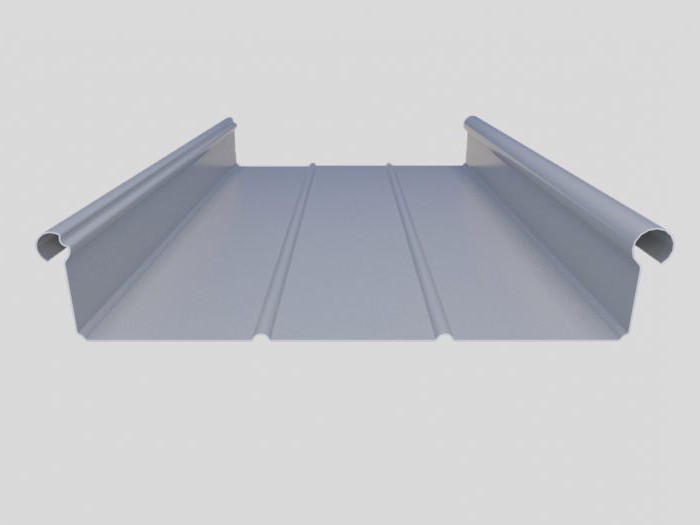
The second way, the oldest - distillation. The concentrates are heated to a very high temperature (about 1000 ° C), zinc vapors are released, which are deposited on clay vessels by condensation. But this method does not give such purity as the first. The resulting vapors contain about 3% of various impurities, including such a valuable element as cadmium. Therefore, Zn is further purified by segregation. At a temperature of 500 ° C, it is defended for some time and a purity of 98% is obtained. For the further manufacture of alloys, this is enough, because then zinc is still alloyed with the same elements. If this is not enough, rectification is applied and zinc is obtained with a purity of 99.995%. Thus, both methods provide highly pure zinc.
Inseparable metal pair
As a rule, lead is present in the composition of zinc alloys as an impurity. In nature, this inseparable metal pair is found quite often. But in fact, the high content of lead in the zinc alloy impairs its physical properties, creating a tendency to intergranular corrosion if its content exceeds 0.007%. Most often, lead and zinc are found together in tin bronzes and brass.
If we talk about the eutectic of these two elements, it is important to note that up to a temperature of 800 ° C they do not mix with each other and represent two different liquids. With rapid cooling, a uniform distribution of Pb occurs in the form of rounded inclusions along the grain boundaries. Zinc-lead alloy is used for the manufacture of printing cliches due to the fact that it dissolves very quickly in acid. Lead impurities are most often removed from zinc using a distillation method.
Copper alloy with zinc
Brass is an alloy known even before our era. In those days, zinc was not yet discovered, but ore was used quite widely. Previously, brass was obtained by alloying smithsonite (zinc ore) and copper. Only in the XVIII century, this alloy was first made using zinc metal.
Nowadays, there are several varieties of brass: single-phase and two-phase. The former contain about 35% zinc, and the latter 50% and 4% lead. Single-phase brass is very ductile, while the second variety is characterized by fragility and hardness. Having examined the state diagram of these two elements, we can conclude that they form a number of phases of an electronic form: β, γ, ε. An interesting variety of brass is tompak. It contains only up to 10% zinc and, due to this, has a very high ductility. Tompak is successfully used for cladding steel and obtaining bimetals. It used to be used to make coins and imitate gold.
Zinc and Steel
In almost every house you can find galvanized things: buckets, pans, boiling out, etc. All of them are reliably protected from rust precisely thanks to zinc. Figuratively speaking, of course, this metal is deposited on steel, and by the logic of things we are not talking about alloy. On the other hand, knowing how galvanizing occurs, the opposite can be argued. The fact is that zinc melts at a very low temperature (about 400 ° C), and when it falls on the surface of the steel in a liquid state, it diffuses into it.
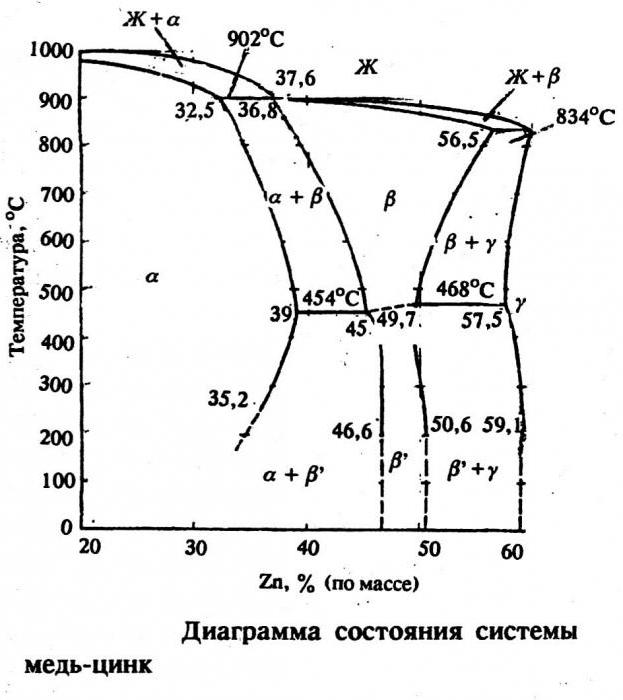
The atoms of both substances are very tightly bound together, forming an iron-zinc alloy. For this reason, we can safely say that Zn is not “laid” on the product, but “embedded” in it. This can be observed in ordinary household situations. For example, a scratch appears on a galvanized bucket. Does it begin to rust in this place? The answer is unequivocal - no. This is because, when moisture enters, zinc compounds begin to break down, but at the same time they form a kind of protection for steel. So, in most cases, such zinc alloys are designed to protect products from corrosion. Of course, other substances, such as chromium or nickel, can be used for these purposes, but the cost of these products will be many times greater.
Tin and Zinc
This alloy is no less popular than others already reviewed by us earlier. In the years 1917-1918 in Bulgaria it was widely used for the manufacture of special vessels that kept a warm liquid for a long time (analogues of modern thermoses). Nowadays, zinc-tin alloy is very widely used in the radio and electric industries. This is due to the fact that a composition with a Zn content of 20% is very well soldered, and polishing of the sediment persists for a long time.
Of course, as an anti-corrosion coating, this alloy can also be used. In its characteristics, it is very similar to a cadmium coating, but at the same time less expensive.
Properties of Zinc Alloys
Of course, all compounds with this metal differ in their percentage. In general, zinc alloys have good casting and mechanical properties. The first and most important thing is corrosion resistance. Most of all, it manifests itself in an atmosphere of dry clean air. Possible manifestations of corrosion can be seen in industrial cities. This is due to the presence in the air of vapors of hydrochloric acid, chlorine and sulfur oxides, which, condensing with moisture, impede the formation of a protective film. Copper-tin-zinc is an alloy that is characterized by high protective properties. It is this composition that is the least susceptible to corrosion, especially in an industrial atmosphere. If we talk about the casting properties of zinc, then, of course, they depend on the alloying elements in its alloys.
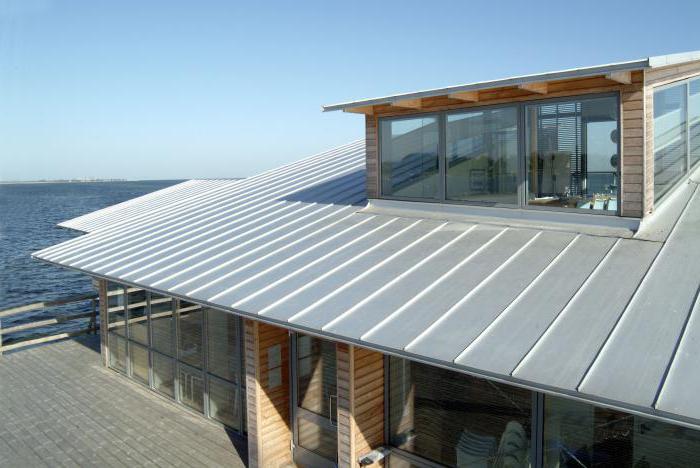
So, for example, aluminum makes their structure homogeneous, fine-grained, ennobles it, reduces the negative effect of iron. Another important alloying element is copper. It increases strength characteristics and reduces intergranular corrosion. Copper-zinc alloy has a high impact strength, but at the same time partially loses its casting properties.
Scopes of zinc and its alloys
In fact, parts made of zinc alloys are quite common in our time. Despite the fact that plastic displaces metal products, in some cases you can not do without them. For example, the automotive industry is an industry that can not do without zinc alloys. Filters, sedimentation tanks, carburetor and gasoline pump housings, wheel casings, silencers - all this and much more is made using compounds of this chemical element.
Due to the fact that zinc alloys have good casting properties, complex parts of various shapes are cast from them with a minimum wall thickness. Construction is another area in which these alloys cannot be dispensed with. Zinc rolling is used for roofing, the manufacture of pipes and gutters. Despite the fact that there is a tendency to reduce the production of zinc alloys, it is not possible to abandon their manufacture due to the relative cheapness and mechanical properties of the material.