The current level of development of radio engineering devices and their widespread use sharply put on the agenda the issues of electromagnetic protection and safety. Until recently, this layer of problems remained in the background, because the technological level did not allow them to be examined in detail. But today there is a whole direction in the development of radar absorbing materials (RPM), which have a variety of purposes.
Applications for RPM
The need to use this kind of materials arises in the military-defense complex, in the civilian industry, in solving typical problems in the development of electronic devices, etc. But protective systems and safety equipment are still the most relevant from the point of view of a request for RPM. Moreover, this is not necessarily a military-technical complex. Modern radar absorbing materials are successfully mastered in the niche of computer systems that process information with the connection of protection against unauthorized access. Objects of biological origin are thus protected from electromagnetic effects, and reducing radar vulnerability is a necessity for a wide range of civilian and military units. Another thing is that the nature of use and the properties of specific RPMs in each case can differ markedly.
What is RPM?
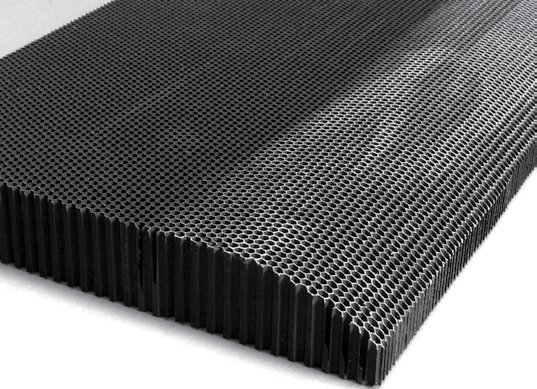
This class of materials can be determined through the ability of the composition and structure of the product to provide absorption of electromagnetic energy in a particular frequency range. New generations of RPMs are more modifiable in terms of their ability to convert absorbed waves into certain types of energy. In this process, in addition to absorption, phenomena such as interference, scattering, and diffraction are also observed. As for the production of radar absorbing materials, they are based on particles of a ferromagnet. They are used as wide-range absorbing materials, forming an insulating layer on the surface of the target product with respect to electromagnetic waves. In this case, the presence of a nonmagnetic dielectric must be a prerequisite for the structural basis of the insulator. On this basis various modifications of RPM are developed. For example, in addition to the structure of ferromagnets, soot or graphite elements can also be included, which act as absorbers. In the manufacture of narrow-band RPMs, emphasis is also placed on the use of rubber or plastics.
The difference between radar absorbing materials and coatings
There is no strict demarcation, from the point of view of operational qualities, between materials and coatings for this purpose, but the mechanics of manufacturing and further handling make it necessary to distinguish these means of isolation. In particular, if the materials can be included in the structural and even elemental base of the target product, then the coatings act only as an auxiliary layer on the surface, without performing any tasks of another property. Partly, there are differences in absorbing abilities, but this factor is more likely conditional. Depending on the structure, the radar absorbing material may show some success as a device for absorbing microwaves, but in any case, this ability will be characteristic only for a limited range. For example, today there are radiation spectra of radar stations, which in principle are not available for the “processing” of RPMs.
Technical and operational characteristics of RPM
The materials are quite diverse in their structure and structure, and yet there are average performance indicators for the most established RPM groups. The basic characteristics reflecting these values include:
- The length of the working waves is from 0.3 to 25 cm.
- The range of operating frequencies is from 300 to 37 500 MHz.
- Magnetic permeability - from 1.26 to 10-6 GN / m.
- Operating temperature range - from -40 to 60 ° .
- Mass - about 200-300 g per 1 sq. M.
It should be borne in mind that not every material can maintain the above performance characteristics in harsh external conditions of use. In this sense, we can distinguish the radio-absorbing material "Ternovnik" carpet type, which is widely used by Russian enterprises in various industries. For him, there are practically no restrictions on operation in harsh climatic conditions. In addition, this material is resistant to mechanical abrasion and retains the ability to isolate objects regardless of their shape and area.
Varieties of RPM
Although there is no clear distinction in the RPM segment at the moment, we can conditionally distinguish the following categories of this material:
- Resonant. Also called frequency-tuned - they are able to provide complete or partial neutralization of the absorbed wave. Efficiency is directly determined by the thickness of the protective product.
- Non-resonant magnetic. They have ferrite in their structure, the particles of which are distributed in the epoxy layer. Magnetic radar absorbing material is able to dissipate radiated energy over a large surface, which allows to achieve neutralization in a wide frequency range.
- Non-resonant volumetric. As a rule, they are thick layers of insulators that absorb the bulk of the input radiation before it is reflected from the rear metal plate.
Features RPM on ferromagnetic powders
A type of coating with a radio-absorbing ability, which contains dispersed microspheres with particles of ferrite or carbonyl iron. In the process of absorption of high-frequency radiation, molecular vibrations occur in the powder, which provoke heat generation. The same derivative energy that is dissipated or transferred to an adjacent storage structure. A similar principle of action is noted in the sheets of neoprene rubber. This material works on the principle of magnetic losses, but contains in its structure a more solid filler of ferrite and graphite.
Foamy RPM
A special group of RPMs that are used for long-term masking of important objects. The basis of materials of this type is polyurethane foam. Its use is justified by the fact that the final product receives a small size and modest mass with a fairly wide range of absorbing activity up to the decimeter spectrum. Although the feedstock in this case is more expensive, radar absorbing materials and masking foam coatings on a polyurethane basis have significant operational advantages:
- High strength characteristics in comparison with similar water-polymer materials.
- Maintaining masking qualities for unlimited time.
- Less stringent storage requirements for components.
- Foam masking coatings, in principle, are characterized by high adhesion, which expands the possibilities of their application to a wide variety of surfaces.
Domestic developments RPM
Russian specialists work in several directions of creating RPMs, but materials based on nanostructures are among the most promising areas. This concept, in particular, is being developed by the Ferrit-Domen Scientific Research Institute, which has developed a whole line of thin radio-absorbing films of hydrogenated carbon with nanoelements. The advantages of Russian-made radar absorbing materials based on nanostructured particles include the increased absorption capacity operating in the ultra-wide frequency spectrum of 7-300 GHz. Also, along with heat resistance and mechanical strength, the developers note the environmental cleanliness and non-waste technology of manufacturing such materials.
Conclusion
Despite the expansion of the general segment of RPM, it is still too early to talk about established and standardized standards for the development of this class of materials. This is largely due to secrecy, in the conditions of which researchers have to work in this area, but there are also problems associated with the technological complexity of development. Obtaining new promising radar absorbing materials today is impossible without the use of innovative feedstock. Technologists are also actively working on more accurate and effective methods for evaluating the absorption capacity, which expands the possibilities for identifying new RPMs. And against this background, radically absorbing agents based on the same ferrites that have already become traditional are logically losing relevance.