Heat-resistant steel, the brands and types of which we will consider below, is designed for long-term use, taking into account the effects of high thermal and electrical loads. A method of manufacturing this material provides for its subsequent operation for a long period without deformation. Features of this type of steel: high strength and creep. The considered metals are mainly used for the construction of structures of unloaded type, operated under the influence of a gas oxidizing environment and temperatures in the range from 500 to 2000 degrees Celsius.
Characteristics
Grades of heat-resistant and heat-resistant steels are characterized by long-term strength. This indicator implies the possibility of opposition of the material to negative external factors for a long time. High creep is the effect on the ongoing deformation of steel in conditions of increased difficulty in terms of operation and maintenance.
The possibility of using the material in a particular field depends on these factors. Creep characterizes the limiting percentage of deformation, which in the case under consideration is from 5 percent per 100 hours to 1% per 100 thousand hours. According to GOST 5632-72, any grade of heat-resistant steel should not include additives of antimony, lead, tin, arsenic and bismuth. This is due to the fact that these materials have a low melting point, and this negatively affects the characteristics of the final product. When heated, some elements emit vapors negative for human health, which also affects their unsuitability for inclusion in this kind of steel. As a result, the optimal composition for the manufacture of the material is an iron base with an admixture of chromium, nickel and other metals that are resistant to high temperatures and oxidative processes of various kinds.
Heat resistant steel: grades
Below are the main brands of the material in question:
- Grade P-193 contains not more than one percent carbon, 0.6% manganese and silicon, as well as about 30% nickel and chromium, 2% titanium.
- Tinidur: carbon - up to 0.13%, manganese and silicon - not more than 1%, chromium - 16%, aluminum - up to 0.2%, nickel - 30-31%.
- Heat-resistant steel grade A-286 includes a percentage of 0.05% carbon, 1.35% manganese, 25% nickel, 0.55% silicon, 1.25% molybdenum, 2% titanium.
- Type DVL42: 0.1% carbon, not more than one percent manganese, 33% nickel, 23% cobalt, up to 1% silicon, 5% molybdenum, 1.7% titanium.
- DVL52 has a similar composition with the above brand, but instead of titanium, up to 4.5 percent tantalum is included.
- Chromadur: 0.11% carbon, 0.6% silicon, 1.18% manganese, 0.65% vanadium, 0.75% molybdenum.
All of these types of heat-resistant steel are produced according to similar technology, only the composition is different. The remainder is iron. It is the basis for any type of material in question.
Production
Grades of heat-resistant steels for furnaces, as well as their analogues, require certain conditions to be met during smelting. Unlike the production of conventional steels, the minimum inclusion of carbon should be integrated into the composition of the alloy, which is aimed at ensuring the required degree of strength. In this regard, coke is not suitable for furnace furnaces. Instead, gaseous oxygen is used. It makes it possible to achieve a fast melting temperature of the metal in a short time.
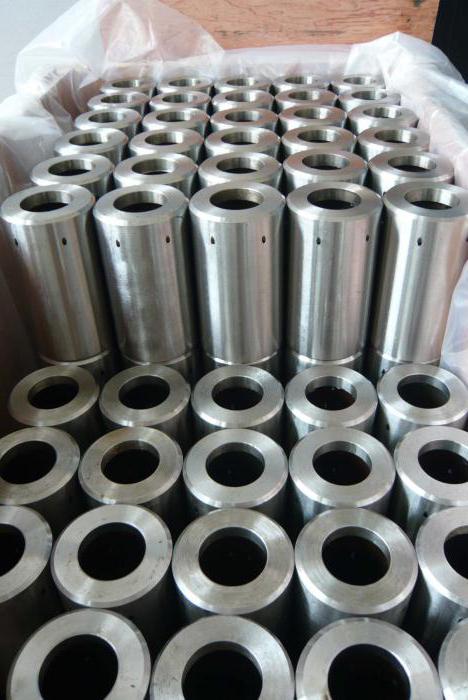
As a rule, the material in question is produced primarily from recycled materials. Chrome and steel are placed simultaneously in the furnace, and the oxygen burned heats the metal to the degree of melting. In the process, the emitted carbon is oxidized, which according to technology needs to be removed from the alloy. Silicon in small quantities makes it possible to protect chromium from oxidation; nickel is also added at the beginning of melting. The remaining additives are mixed with the main raw material at the end of the process. The temperature of the procedure is about 1800 degrees Celsius.
Treatment
Processing of any grade of stainless heat-resistant steel is carried out using prepared hard tools. They are made of metals containing cobalt and tungsten alloys. The rest of the technological process is almost identical to the processing of standard grades. It is carried out on standard screw - cutting lathes using standard lubricants and coolants. Safety measures are also no different.
Welding work on the material in question is performed by the arc or argon method. Before welding, both connected parts must undergo hardening, which consists in heating the element to 1000 degrees and subsequent instant cooling. This method makes it possible to avoid the appearance of cracks in the welding process. It is important at the same time to maintain the degree of quality of the seam at the level of the base material, otherwise serious malfunctions may occur during operation.
Application
The material in question is used in conditions where a constant thermal load on the part is implied. For example, assign a grade of heat-resistant steel silchrome for valves or similar products, and make sure its effectiveness. Also, this composition is often used for special furnaces with a high heating temperature. Features of steel can withstand up to several tens of thousands of work cycles, which significantly reduces the cost of production.
Austenitic grades are used in the manufacture of rotors, turbine blades and engine valves. They have excellent resistance to high temperatures and enhanced resistance to vibration and mechanical stress. The black grade of heat-resistant steel with increased resistance to corrosion is mainly used for the production of structures that are used outdoors or in high humidity. The features of this type include high inclusion in the composition of chromium, which makes it possible to increase the efficiency of resistance to oxidation and other destructive processes.
Cast heat resistant steels: grades for chain links, pipelines and valves
Among this category of martensitic steels, the most famous are the following grades:
- X-5. Pipes oriented to work at a temperature of no higher than 650 degrees are produced from this steel.
- 18, 5, 5 - used to produce pipes and equipment designed for operation at a temperature of 500-600 degrees. Moreover, the period of work is limited (from one to one hundred thousand hours).
- 492, 31372 - withstand thermal stress up to 950 degrees Celsius, are used for the manufacture of valves for motor vehicles.
- 1X8VF - the brand is suitable for the production of steam turbines, can withstand a load of 500 degrees with a working life of at least 10 thousand hours.
Structural nuances
Grades of heat-resistant steel for boilers with a martensitic structure are basically perlite. It changes its state, depending on the chromium content. To obtain products with an internal index of high hard sorbitol, the material is first quenched at a temperature of at least 950 degrees, and then subjected to tempering. Such brands include: X10C2M, X6C, X7CM, X9C2. Pearlitic species belong to the chromomolybdenum and chromosilicon categories.
Steel alloys, which contain up to 33 percent chromium, are heat-resistant materials with a ferritic internal configuration. Products made of this material are annealed, which allows the formation of a fine-grained structure. When such steels are heated above 850 degrees, the granularity becomes higher, which leads to an increase in the fragility of the material. Stamps in this category: 17, 112, 25, 28, 017.
Refractory steel
For the operation of products withstanding up to two thousand degrees, refractory metals are used. The following are the elements that are used in such formulations and their melting point in degrees Celsius:
- Vanadium - 1900.
- Tantalum - 3000.
- Tungsten - 3400.
- Niobium - 2415.
- Molybdenum - 2600.
- Rhenium - 3180.
- Zirconium - 1855.
- Hafnium - 2000.
The configuration of these metals changes upon heating, since the high temperature allows them to be brought into a brittle state. The fibrous structure of the elements is achieved by recrystallization of refractory steels. Increasing the heat resistance of the material is carried out by adding special mixtures. Similarly, the compounds are protected from oxidation.
Finally
Another name for the heat-resistant steel grade (stainless steel) is scale-resistant. Such materials are endowed with such quality in the manufacturing process. As a result, they are able to function for a long period under conditions of high thermal effects without deformation, while exhibiting resistance to gas corrosion. Simply put, through alloys of various elements, optimum qualities of heat-resistant materials are achieved, depending on the expected operating conditions.
Heat-resistant steels, presented on the modern market with a wide variety of grades, as well as heat-resistant alloys of various categories, are recognized by most experts as the best material for the manufacture of parts and parts of structures and equipment, the operation of which is carried out in constant contact with high temperatures, aggressive environment or other complex influences.