The use of aluminum as a structural material began a long time ago. However, it stood out only with a low specific gravity, good ductility and high resistance to corrosion. The strength and hardness of this material were extremely low. The problem was partially eliminated by Soviet scientists who added magnesium to the composition. Thus, AMg alloys were first obtained.
general description
Today, there are several varieties of this type of alloy. All of them differ among themselves in their characteristics and scope. For example, you can consider the properties of the second and third categories, that is, AMg-2 and AMg-3. The composition of the AMg alloy in this case is supplemented by elements such as Si and Mn. Corrosion resistance also remained at a high level, good weldability appeared when using such types of welding as spot, roller, gas. In addition, these two groups of material are distinguished by good deformation in both cold and hot conditions.
The interval of hot deformation, for example, is in the region from 340 to 430 ° C. Cooling after this type of deformation is carried out outdoors. It is also worth adding that AMg alloys of this type are not hardened by heat treatment. Profiles are often made from this material. In their manufacture, two types of annealing are used: low at a temperature of 270-300 ° C and high at a temperature of 360-420 ° C.
Description AMg-6
To date, all AMg alloys belong to the category of deformable substances. It is worth adding that the number of elements that are used for alloying, as well as mechanical properties are regulated by GOST 4784-97. If you believe this document, then in addition to the alloy AMg - aluminum and manganese, other chemicals are also present in the composition.
Chemical composition
It is worth considering the chemical composition of the AMg-6, since it is considered the best among all similar materials.
- Naturally, the first element in the list is magnesium in an amount of 5.8% to 6.8%. This element is the main hardener of aluminum. If you add only 1% magnesium of the total mass of aluminum to the composition, then you can achieve an increase in strength by about 35 MPa without compromising ductility. However, it should be noted that magnesium reduces its natural resistance to corrosion. This becomes especially noticeable if its amount begins to exceed 6%, and the part from the aluminum alloy AMg-6 is under static load.
- Manganese is also added in an amount of 0.5 to 0.8%. This is necessary for grinding the graininess of aluminum, which will positively affect the mechanical properties. In addition, this element significantly reduces the risk of segregation - the uneven distribution of chemical composition on the surface of aluminum.
- 0.06% titanium is added to improve technological properties. Most of all it concerns the weldability of the material. Titanium is able to reduce the structure of the alloy to a finer-grained, as well as reduce the tendency to crack. All this leads to the fact that the strength of the welds of the material from the alloy AMg-6 is greatly increased.
- Sodium in an amount of 0.01%. It must be said here that this element is not added to the composition on purpose, since this is extremely undesirable, it appears in it due to the melting of cryolite-containing fluxes. The melting point of sodium is only 96 ° C, which is much lower than that of aluminum itself. Because of this, it can be said that the characteristics of an AMg alloy of this type are complemented by increased red breaking resistance due to sodium.
- Copper in an amount of 0.01%. This substance belongs to the category of harmful impurities for aluminum. The presence of copper significantly reduces the corrosion resistance of this material. In addition, it affects the ductility of the alloy. However, it is worth adding here that even a small amount of copper significantly increases mechanical properties, that is, strength and hardness.
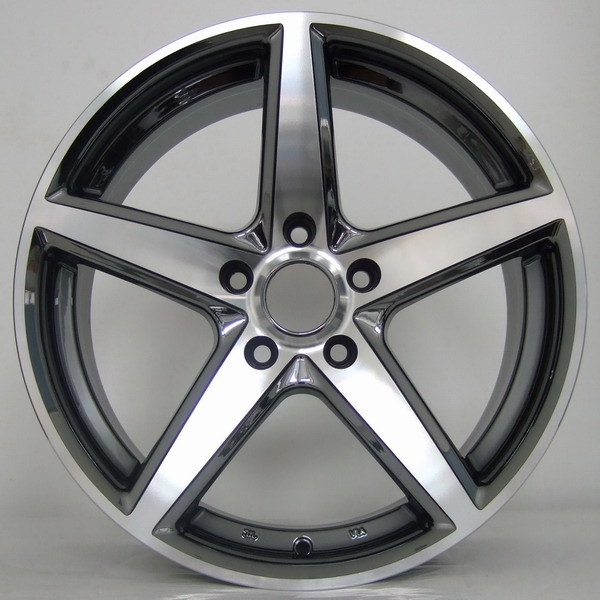
AMg-6 disadvantages
Despite all the additives, this alloy still has some disadvantages.
- The yield strength of the alloy is quite low. In order to somehow avoid or reduce the influence of this drawback, up to 0.8% zinc can be added to the composition or surface surface hardening can be carried out.
- Another significant minus is the inability to harden under the influence of heat treatment. All alloys with a magnesium content below 8% cannot be hardened.
Positive qualities of aluminum alloys
The introduction of a variety of chemical elements has led to the fact that certain characteristics still managed to significantly improve.
- The mechanical properties were brought to a satisfactory level. After annealing, the tensile strength is 340 MPa, as in conventional steels. Hardness also managed to significantly increase. The alloy AMg-6, this figure is the highest among others.
- Low specific gravity. This means that the use of elements from such an alloy is still very important, especially in those designs where there are strict requirements for the mass of the object.
- Resistance to corrosion. If earlier it was quite high, then the alloy becomes completely immune to the effects of atmospheric air, water, as well as a group of weak acids and alkalis. However, to obtain all these qualities, it is necessary to conduct annealing and only with a low temperature.
- The vibration resistance of the aluminum and magnesium alloy turned out to be quite high and amounted to 130 MPa.
- High manufacturability. This means that the weldability of the alloy belongs to the first category, that is, the density and strength of the weld are almost equal to the whole material. In addition, the ductility is very high, and the elongation to compression was 20%.
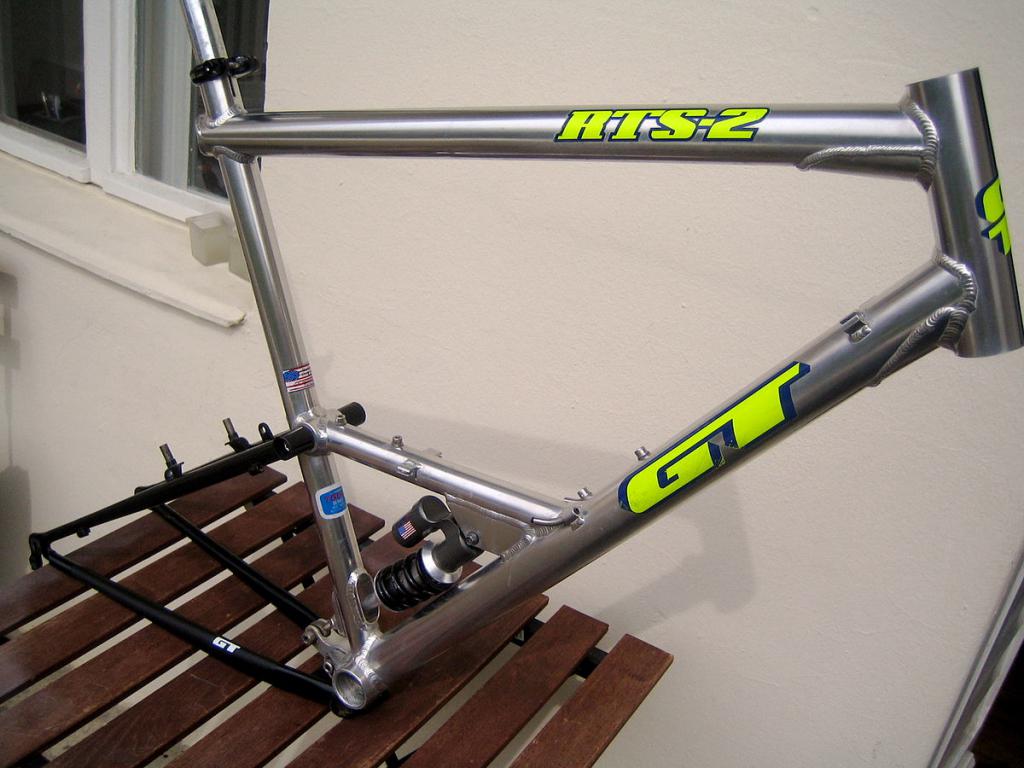
Material application
That alloy AMg-6 has become the most common. It is supplied to the building materials market in the form of bars, channels, sheets, corners with a wide variety of dimensions. These parts are most widely used when it is necessary to create a welded structure with a restriction on the mass of the object. From this material, it is also possible to successfully manufacture both inner and outer skin for a variety of automobile vehicles. In addition, tanks that are suitable for transporting oil, for example, can be made from it.