The organization of power supply networks involves the implementation of a wide range of activities, in which cable laying plays a crucial role. A variety of technologies and methods are involved in the work on the electrical infrastructure. Workers are required not only the physical installation of reference points with lines, but also the choice of optimal installation configurations, which will increase the facility's operational life. To date, the laying of cable lines is implemented in a variety of ways - from the arrangement of underground channels to fixing the contour in special structures. Each installation option requires compliance with specific standards and technical regulations.
General cable line mounting technology
Installation operations with power cables are mainly reduced to physical fastening and organization of systems that hold the lines in a given position. Ancillary technical measures are also common, including connection and termination. The wires are connected to the electrical equipment using cable sleeves, terminations and clamps. The main thing in this part of the work is to correctly compare the size of the fixing fittings and the cable itself. The quality of installation operations also depends on how carefully the initial preparation of the material for the same joints was made. Cutting and stripping the ends of the wire does not do without special tools, including strippers, wire cutters, clamping pliers, etc. In addition, the installation of a cable line may include the use of protective electrochemical compositions. These may be sealants that provide insulating barriers. The application of such materials in the process of wiring requires care and compliance with the installation technology of a particular cable.
Cable laying in a trench
This is one of the most common cable management methods, which is appropriate for use on unpaved areas where there is also a minimal risk of physical damage to the line. The laying begins with the formation of a trench in which the wire will be immersed. So that underground cable structures have a solid base in the lower part and do not freeze, the technology requires performers to create a pillow in the form of a small embankment. It may include sand, gravel or gravel - the coating height reaches an average of 10 cm.
The prepared cable is immersed in the trench, and then insulated with special windings. If necessary, separate sections are connected with the expectation of strengthening the points of information by auxiliary fittings. If conditions allow, then the connection of wires and cables during underground installation is desirable to make in advance. The same applies to insulation works, although the transportation process also does not always make possible the advance technical preparation of the cable line. The advantages of this method include a minimum of financial costs and the possibility of the most profitable use of the wire section. The disadvantages of underground laying technology include the lack of access to the line: for inspection and diagnosis, you will have to dig a trench.
Cable rolling in the ground
The technique of laying the cable in the trench involves rolling. Actually, this operation in one form or another is required with other installation technologies, but in this case, approaches to its implementation are most pronounced. There are two rolling methods. In the first case, the laying of cable lines is carried out using a special conveyor, which captures the end of the wire and, as it moves along the trench, puts it to the very bottom. Workers in the process of performing this operation monitor the correctness of rolling and the accuracy of the position of the wire at the bottom of the trench.
The second method of rolling does not involve the use of moving equipment. The drum, on which the cable was previously wound, is fixed in one place so that it remains possible to unwind the wire. For ease of rolling use special rollers with clamps. They are fixed at the end of the cable and its free laid part with one or another step, the distance of which depends on the weight of the wire. If in the future it is planned to install the cable line in the form of a connection with other segments, then this option may not be suitable because of the risk of a line break in the place of attachment. In such situations, it is better to use the same conveyor.
Laying in block constructions
Block constructions are understood as different constructions. A classic example is an asbestos-concrete pipe into which a cable is passed, the diameter of which is 1.5 times smaller than the reinforcing sheath. Another type of unit is a mesh panel, into which wire lines are also inserted. This option is suitable in cases where you need to lay several contours in a small area. Such blocks do not provide continuous insulation, but only separate the wires at certain points of the strip. The block technology for mounting cable lines is highly reliable, which is achieved thanks to effective protection against mechanical damage.
However, the durability of the line will depend on the type of protective structure used. Obviously, the most reliable solution will be the use of tubular channels, but it is also the most costly and difficult to implement. The same rolling with this scheme can only be performed manually without the use of a conveyor. On the other hand, in some installation conditions, the use of blocks becomes the only acceptable way to arrange the line. In particular, pipes for cable laying are used at the intersection of the circuit with roads and railways. Also, additional reinforcement of the wire is indispensable if it is planned to be laid in soils with an aggressive chemical composition.
Cable routing in ductwork
It has already been said that the main drawback of laying a line in a trench underground is the lack of direct access to the cable without performing land work. Combine the advantages of laying in a trench and block technology allows installation in a duct structure. With this circuit arrangement scheme, it is possible to service cable lines without excavation, that is, it is possible to access the line for repair and diagnostic measures. The channel itself is a kind of box, the walls of which are formed by concrete slabs or bricks. It turns out a closed structure in which the cable is contained.
The contour is also located in the ground, but closer to the surface than in the case of trench laying. Moreover, this scheme is applied at the enterprises directly in the premises, so the upper part of the box is literally on the surface. But if the installation is implemented outside the production facilities, then the performers immerse the structure in the ground. But this does not mean that access to communications will require the implementation of large-scale land works in the form of excavations. The internal installation of the cable line in the channel is carried out using special suspensions and clamps. In some cases, the traditional laying on the bottom using substrates.
Laying in manifolds and tunnels
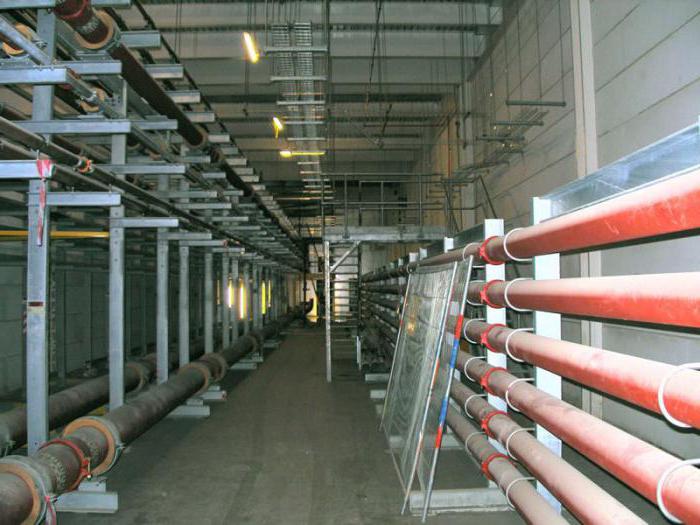
Tunnel structures are usually included in the infrastructure of industrial and industrial facilities. These are small corridor-type rooms in which communications are laid. In terms of reliability and durability, this installation option can be considered the best. The wires are fastened by means of special couplings. Initially, the project for the arrangement of tunnels provides for the possibility of integrating communication lines into special niches. Collector rooms in the sense of service are even more technological. The features of such objects include the possibility of laying a large number of wires - usually up to 20. Each line is also equipped with insulating windings, but in this case there is no need for armored protection. At the same time, the construction of cable lines is allowed only in those collectors and tunnels where water collectors and storm sewer systems are provided. Depending on the operating conditions of the wiring, the installation of ventilation systems may also be required, including artificial and natural circulation installations.
Special attention should be paid to the technique of rolling the cable in the tunnel. The use of conveyors, as well as massive drums, in this case is impossible. Unwinding is carried out manually or using a winch mechanism. If a thick cable or several wires are serviced at the same time, then roller systems are involved. The indisputable advantages of this type of cable management include a high degree of line protection and direct access for maintenance. However, such laying conditions are rare and laid as part of the technological infrastructure in industrial projects.
Laying in galleries
In this case, we are talking about ground structures that can be equipped outside of technological premises. Galleries are called flyovers, which, like a tunnel, can go through the most critical sections of the laying. If overhead communication lines are laid on poles by weight, then in the case of galleries, installation is carried out in closed buildings. However, there are different versions of the execution of flyovers. Sometimes, in order to save money, designers develop structures without side walls. Also, objects of this type differ in the possibilities of passing inside. There are designs in the niches of which you can even carry out transportation, and there are also buildings with limited access only for the implementation of technical work on repair, diagnostics and maintenance of the line itself.
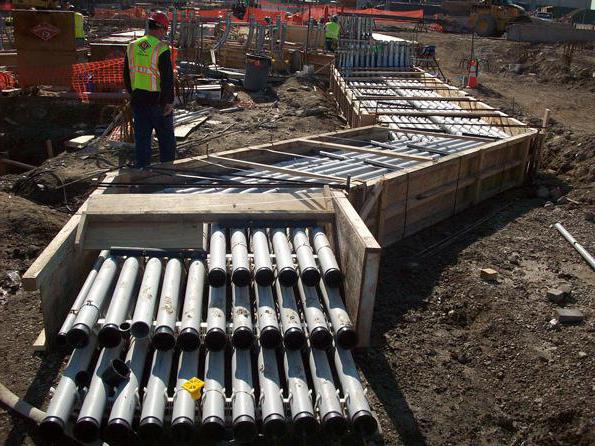
This option, despite its attractiveness, is not used often because of high financial costs. Nevertheless, it is the only possible one when it comes to laying within the framework of enterprises whose underground channels are already saturated with communications. As for line protection, ground structures provide the necessary level of safety. On difficult sections of the route, asbestos-concrete pipes for cable laying can also be used, which protect the circuits from destructive mechanical and atmospheric influences.
Cable suspension
This option involves the implementation of the classic scheme of mounting lines. This method is characterized by ease of execution, economic affordability and the ability to conveniently perform installation and repair operations. However, far from all cable communications can in principle be carried out by this method: first of all, this applies to cases where it is necessary to install a cable line, supplemented by thick layers of insulation. Do not forget that the hinged wiring is operated in open conditions with direct exposure to ultraviolet rays, high and low temperatures, precipitation, etc. Accordingly, some types of cables require effective insulation, which makes the line heavier, causing problems during installation.
It cannot be said that aerial wiring significantly outperforms underground installation, but in situations where arranging the same trenches is impossible, this method is quite worth considering. Direct installation is carried out on poles and poles of high-voltage lines. During installation, electrical cables are insulated in accordance with the brand of wire. In choosing a protective equipment, specialists take into account such characteristics as dynamic resistance, strength, frost resistance, ability to withstand and not deform before short-term loads, etc. Further, during maintenance at certain intervals, the insulation shell can be replaced, as, indeed, itself cable.
What is a heating cable for?
As part of sets of communication lines, technological wires and materials are often found that are not the main conductors, but that they fulfill responsible auxiliary tasks. These include heating wire. Its function is to ensure the optimal temperature regime in which power communications should be operated. Thus, cable lines are protected against freezing, in which the wires lose their operational properties. An electric charge is supplied to the heating circuit, which, thanks to a special alloy of the inner core, is converted into thermal energy heating the nearby wires.
Directly in cable wiring, heating conductors are rare. Typically, the main insulation function is heat storage. Most often, heating lines are used as an adjunct in technological equipment. By this technique, tanks, pipelines, individual parts of transformers and industrial equipment are insulated. The features that a heating cable possesses include a protective sheath made of polymeric materials. Also, depending on the brand, manufacturers use different means of electrical shielding. For example, a solid aluminum or copper wire mesh can be used as such. The main shell is made of polyvinyl chloride, which protects the cores from mechanical damage. In addition to the heating function, anodized conductors can also serve as an effective electrochemical corrosion protection measure. This kind of protection is required by metal fittings, which are used for fastening and tying communications.
Conclusion
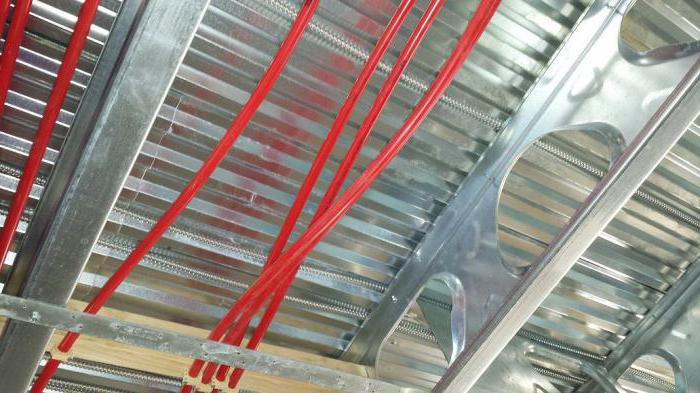
Installation operations in the work with power cables are preceded by the development of the project. The compiler of the technical plan for laying communications takes into account many operating factors that give him reason to make a choice in favor of a particular laying method. For example, overhead communication lines are organized in cases where it is not possible to use more reliable ground-based mounting schemes. Underground methods of conducting communications justify themselves in many ways, but due to the lack of direct access to the line, they are also often abandoned. If we are talking about the organization of a network adjacent to industrial enterprises, it is more likely that part of the circuit can be laid in a technological tunnel or collector room. In addition to the external laying conditions, the operational requirements for the cable itself are taken into account. Only a comprehensive analysis of the conditions for the implementation of the project assignment can give the right answer to questions about choosing the optimal cable line installation diagram.