Titanium carbide is one of the promising analogues of tungsten. It is not inferior to the latter in physical and mechanical properties, and the manufacture of this compound is more economical. It is most widely used in the manufacture of carbide cutting tools, as well as in the oil and general engineering, aviation and rocket industries.
Description and discovery history
Titanium carbide occupies a special place among compounds of transition metals of the periodic system of chemical elements. It is distinguished by its special hardness, heat resistance and strength, which determines its widespread use as the basis for tungsten-free hard alloys. The chemical formula of this substance is TiC. Outwardly, it is a light gray powder.
Its production began in the 20s of the XX century, when companies involved in the production of incandescent bulbs were looking for an alternative to the expensive technology for manufacturing tungsten filaments. As a result, a method for producing cemented carbide was invented. This technology was less expensive, since the raw materials - titanium dioxide, were more affordable.
In 1970, the use of titanium nitrite began, which made it possible to increase the viscosity of cemented compounds, and the addition of chromium and nickel made it possible to increase the corrosion resistance of titanium carbide. In 1980, a powder sintering process was developed under the influence of uniform compression (pressing). This has improved the quality of the material. Sintered carbide powders are currently used in those fields of technology where high resistance to temperatures, wear and oxidation is required.
Chemical characteristics
The chemical properties of titanium carbide determine its practical importance in technology. This compound has the following characteristic features:
- resistance to HCl, HSO 4 , H 3 PO 4 , alkalis;
- high corrosion resistance in alkaline and acidic solutions;
- lack of interaction with zinc melts, the main types of metallurgical slag;
- active oxidation only at temperatures above 1100 ° C;
- wettability by melts of steel, cast iron, nickel, cobalt, silicon;
- the formation of TiCl 4 in chlorine at t> 40 ° C.
Physical and mechanical properties
The main physical and mechanical characteristics of this substance are:
- Thermophysical: melting point - 3260 ± 150 ° C; boiling point - 4300 ° C; heat capacity - 50.57 J / (K ∙ mol); thermal conductivity at 20 ° C (depending on carbon content) - 6.5-7.1 W / (m ∙ K).
- Strength (at 20 ° C): ultimate compressive strength - 1380 MPa; tensile strength (hot-pressed carbide) - 500 MPa; microhardness - 15,000–31,500 MPa; impact strength - 9.5 ∙ 10 4 kJ / m 2 ; Mohs hardness is 8–9 units.
- Technological: wear rate (depending on carbon content) - 0.2-2 microns / h; coefficient of friction - 0.4-0.5; weldability is bad.
Getting
The production of titanium carbide is carried out by several methods:
- Using a carbon thermal method from titanium dioxide and solid carburizing materials (68 and 32% in a mixture, respectively). As the most commonly used soot. The raw materials are first compressed into briquettes, which are then placed in a crucible. Carbon saturation occurs at a temperature of 2000 ° C in a protective atmosphere of hydrogen.
- Direct carbidization of titanium powder at a temperature of 1600 ° C.
- Pseudo-melting - heating a metal powder with soot briquettes in a two-stage scheme up to 2050 ° C. Soot is dissolved in a titanium melt, and carbide grains up to 1 thousand microns in size are obtained.
- Ignition in a vacuum of a mixture of titanium powder and carbon black (pre-briquetted). The combustion reaction lasts several seconds, then the composition is cooled.
- Plasma-chemical method of halides. This method allows to obtain not only carbide powder, but also coatings, fibers, single crystals. The most common mixture is titanium chloride, methane and hydrogen. The process is conducted at a temperature of 1200-1500 ° C. Plasma flow is created using an arc discharge or in high-frequency generators.
- From shavings of titanium alloys (hydrogenation, grinding, dehydrogenation, carbon saturation or carbidization with soot).

A product made by one of these methods is processed in grinding units. Powder grinding is carried out to a particle size of 1-5 microns.
Fibers and crystals
Obtaining titanium carbide in the form of single crystals is carried out in several ways:
- By melting method. There are several varieties of this technology: the Verneuil process; drawing from a liquid bath formed by melting the sintered rods; electrothermal method in arc furnaces. These techniques are not widely used, as they require high energy costs.
- The solution method. A mixture of titanium and carbon compounds, as well as metals playing the role of a solvent (iron, nickel, cobalt, aluminum or magnesium), is heated in a graphite crucible to 2000 ° C in vacuum. The metal melt is kept for several hours, then it is treated with hydrochloric acid solutions and hydrogen fluoride, washed and dried, flotation is carried out in a mixture of trichlorethylene and acetone to remove graphite. This technology allows to obtain crystals of high purity.
- Plasma-chemical synthesis in a reactor during the interaction of a plasma jet with titanium halides TiCl 4 , TiI 4 . As a carbon source, methane, ethylene, benzene, toluene and other hydrocarbons are used. The main disadvantages of this method are the technological complexity and toxicity of raw materials.
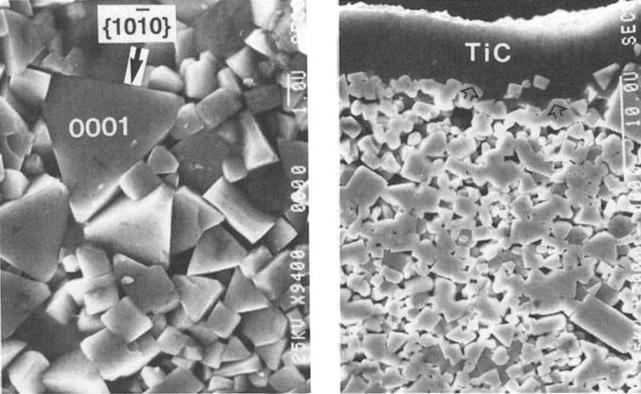
Fibers are obtained by precipitation of titanium chloride in a gaseous medium (propane, carbon tetrachloride mixed with hydrogen) at a temperature of 1250-1350 ° C.
The use of titanium carbide
This compound is used as a component in the manufacture of heat-resistant, heat-resistant and hard tungsten-free alloys, wear-resistant coatings, abrasive materials.
Carbide systems with titanium carbide are used to manufacture the following products:
- tools for metal cutting;
- details of rolling machines;
- heat resistant crucibles, thermocouple parts;
- furnace lining;
- jet engine parts;
- non-consumable welding electrodes;
- elements of equipment designed for pumping aggressive materials;
- abrasive pastes for polishing and finishing surfaces.
Parts are made by powder metallurgy methods:
- sintering and hot pressing;
- slip casting in plaster molds and sintering in graphite furnaces;
- pressing and sintering.
Coverings
Titanium carbide coatings can increase the performance of parts and at the same time save on expensive materials. They are characterized by the following properties:
- high wear resistance and hardness;
- chemical stability;
- low coefficient of friction;
- low tendency to cold welding;
- scale resistance.
A layer of titanium carbide is applied to the base material in several ways:
- The vapor deposition.
- Plasma or detonation spraying.
- Laser surfacing.
- Ion plasma spraying.
- Electrospark alloying.
- Diffusion saturation.
On the basis of titanium carbide and heat-resistant nickel alloys, cermet is also made - a composite material that can increase the wear resistance of parts in liquid media by 10 times. The use of this composite is promising for increasing the service life of pumping equipment and other equipment, which include injection fittings to maintain reservoir pressure, torch burners, drill bits, shutoff valves.
Carbide steel
Tungsten and titanium carbides are used for the manufacture of carbide steels, which by their properties occupy an intermediate position between hard alloys and high-speed steels. Refractory metals provide them with high hardness, strength and wear resistance, and the steel matrix provides viscosity and ductility. Mass fraction of titanium carbide and tungsten can be 20-70%. Such materials are obtained by the powder metallurgy methods described above.
Carbide steels are used for the production of cutting tools, as well as parts of machines operating in conditions of strong mechanical and corrosive wear (bearings, gears, bushings, shafts and others).