You may notice that over the past decade, products have gained popularity, the name of which is added the prefix "bio". It is intended to inform that the product is safe for humans and nature. It is actively promoted by the media. It even came to a ridiculous point - when choosing a drink, biokefir is considered the best, and biofuel is no longer an alternative to oil, but an environmentally friendly product. And about bioextracts that make cosmetics work “miracles”, do not forget.
general information
Now let's talk about the serious. Often, moving on roads, you can see natural dumps. In addition, there are full-fledged landfills where people’s waste products are stored. It seems to be not bad, but there is one drawback - the decomposition period is too long. There are a large number of ways to fix this - this is the recycling of garbage, and the use of less harmful materials that quickly destroy reducers. Here we are talking about the second case.
There are many points here. Packaging, tires, glass, derivatives of the chemical industry. All of them require attention. However, there is no definite universal recipe. Therefore, it is necessary to know specifically what and how to ensure the prevention of environmental pollution.
Biodegradable polymers have been developed as an answer to the problem of recycling plastic waste. It is no secret that their volume is growing every year. For their abbreviated designation, the word biopolymers is also used. What is their feature? They can decompose in the environment due to the action of physical factors and microorganisms - fungi or bacteria. A polymer is considered to be such if its entire mass is absorbed in water or soil in six months. This allows you to partially solve the problem of waste. In this case, decay products are obtained - water and carbon dioxide. If there is anything else, then it must be examined for safety and the presence of toxic substances. They can also be processed by most standard plastic manufacturing technologies, such as extrusion, blow molding, hot molding and injection molding.
What are the directions of work?
Obtaining biodegradable polymers is a rather time-consuming task. The development of technologies to produce safe materials is actively carried out in the USA, on the European continent, in Japan, Korea and China. Unfortunately, it should be noted that in Russia the results are unsatisfactory. The creation of biodegradation technology for plastics and their preparation from renewable raw materials is an expensive pleasure. In addition, there is still enough oil in the country for the production of polymers. But still, three main areas can be distinguished:
- Hydroxycarboxylic acid production of biodegradable polyesters.
- Creation of plastics based on reproducible natural components.
- Acquisition of biodegradability properties by industrial polymers.
But what in practice? Let's take a closer look at how biodegradable polymers are produced.
Bacteria polyhydroxyalkanoates
Microorganisms often grow in environments where carbon nutrients are present. In this case, there is a deficiency of phosphorus or nitrogen. In such cases, microorganisms synthesize and accumulate polyhydroxyalkanoates. They serve as a reserve of carbon (food reserves) and energy. If necessary, they can decompose polyhydroxyalkanoates. This property is used for industrial production of materials of this group. The most important for us is polyhydroxy butyrate and polyhydroxy valerate. Thus, these plastics are biodegradable. At the same time, they are aliphatic polyesters resistant to ultraviolet radiation.
It should be noted that although they have sufficient stability in the aquatic environment, the sea, soil, and the composting and waste treatment environment contribute to their biological decomposition. And this happens pretty quickly. For example, if compost has a humidity of 85% and 20-60 degrees Celsius, then decomposition into carbon dioxide and water will take 7-10 weeks. Where are polyhydroxyalkanoates used?
They are used for the manufacture of biodegradable packaging and non-woven materials, disposable wipes, fibers and films, personal care products, water-repellent coatings for cardboard and paper. As a rule, they can pass oxygen, are resistant to aggressive chemicals, have relative thermal stability, and have a strength comparable to polypropylene.
Speaking about the disadvantages of biodegradable polymers, it should be noted that they are very expensive. An example is Biopol. It costs 8-10 times more expensive than traditional plastic. Therefore, it is used only in medicine, for packaging some perfumes and personal care products. More popular among polyhydroxyalkanoates is mirel obtained from saccharified corn starch. Its advantage is its relatively low cost. But, nevertheless, its price is still double the price of traditional low-pressure polyethylene. At the same time, raw materials account for 60% of the cost. And the main efforts are aimed at finding its cheap analogues. The prospect under consideration is cereal starch, such as wheat, rye, and barley.
Polylactic acid
The production of biodegradable polymers for packaging is also carried out using polylactide. He is polylactic acid. What is he like? It is a linear aliphatic polyester, a condensate of lactic acid. It is a monomer from which polylactide is artificially synthesized using bacteria. It should be noted that its production using bacteria is easier than the traditional method. After all, polylactides are created by bacteria from available sugars as part of a technologically simple process. The polymer itself is a mixture of two optical isomers having the same composition.
The resulting substance has a fairly high thermal stability. So, glass transition occurs at a temperature of 90 degrees Celsius, while melting occurs at 210-220 Celsius. Also, polylactide is resistant to ultraviolet, slightly flammable, and if it burns, then with a little smoke. It can be recycled using all methods that are suitable for thermoplastics. Products obtained from polylactide have high rigidity, gloss, and transparency. They make plates, trays, film, fiber, implants (this is how biodegradable polymers are used in medicine), packaging for cosmetics and food products, bottles for water, juice, milk (but not carbonated drinks, because the material passes carbon dioxide). As well as fabrics, toys, cases for cell phones and computer mice. As you can see, the use of biodegradable polymers is very extensive. And this is only for one of their group!
Production and biodegradation of polylactic acid
For the first time, a patent for its production was issued back in 1954. But the commercialization of this bioplastics began only at the beginning of the 21st century - in 2002. Despite this, there are already a large number of companies that are engaged in its manufacture - in Europe alone there are over 30 of them. An important advantage of polylactic acid is its relatively low cost - it competes almost equally with polypropylene and polyethylene. It is assumed that already in 2020 polylactides will be able to begin to squeeze them on the world market. To increase its biodegradability, starch is often added to it. It also has a positive effect on the price of the product. True, the resulting mixtures are rather fragile, and plasticizers, such as sorbitol or glycerin, have to be added to them, so that the final product is more elastic. An alternative solution to the problem is to create an alloy with other degradable polyesters.
Polylactic acid decomposes in two stages. First, the ether groups are hydrolyzed with water, resulting in the formation of lactic acid and a few other molecules. Then they decompose in a specific environment with the help of microbes. Polylactides this process take 20-90 days, after which only carbon dioxide and water remain.
Starch Modification
When using natural raw materials, this is good, because the resources for it are constantly being renewed, so they are practically unlimited. The most widespread in this regard is starch. But it has a drawback - it has an increased ability to absorb moisture. But this can be avoided if you notice some of the hydroxyl groups on the ester.
Carrying out chemical treatment allows you to create additional bonds between the parts of the polymer, which contributes to an increase in heat resistance, resistance to acids and shear force. The result - modified starch - is used as biodegradable plastic. It decomposes at 30 degrees Celsius in two months, making it highly environmentally friendly.
To reduce the cost of the material, use raw starch, which is mixed with talc and polyvinyl alcohol. It can be produced using the same equipment as for ordinary plastic. Also, modified starch can be dyed and printed using conventional technologies.
Please note that this material is antistatic in nature. The disadvantage of starch is that its physical properties, in general, are inferior to resins obtained by the petrochemical method. That is, polypropylene, as well as high and low pressure polyethylene . Nevertheless, it is applied and marketed. So, from it make pallets for food products, agricultural films, packaging materials, cutlery, as well as nets for fruits and vegetables.
Use of other natural polymers
This is a relatively new topic - biodegradable polymers. Rational environmental management contributes to new discoveries in this area. So in the production of biodegradable plastics, many other natural polysaccharides are used: chitin, chitosan, cellulose. And not only individually, but also in combination. For example, a film with increased strength is obtained from chitosan, microcellulose fiber and gelatin. And if it is buried in the ground, then it will quickly be decomposed by microorganisms. It can be used for packaging, trays and the like.
In addition, combinations of cellulose with dicarboxylic acid anhydrides and epoxy compounds are quite common. Their strength is that they decompose in four weeks. Bottle, films for mulching, disposable tableware are made from the obtained material. Their creation and production is growing rapidly every year.
Biodegradability of industrial polymers
This problem is quite relevant. Biodegradable polymers, examples of reactions with the environment of which were given above, will not last in the environment for a year. Whereas industrial materials can pollute it for decades and even centuries. All this applies to polyethylene, polypropylene, polyvinyl chloride, polystyrene, polyethylene terephthalate. Therefore, reducing the timing of their degradation is an important task.
To achieve this result, there are several possible solutions. One of the most common methods is the introduction of special additives into the polymer molecule. And in warmth or in the light, the process of their decomposition is accelerated. It is suitable for disposable tableware, bottles, packaging and agricultural films, bags. But, alas, there are problems.
The first one is that additives should be used in the framework of traditional methods - forming, casting, extrusion. In this case, the polymers should not decompose, although they are subjected to heat treatment. In addition, additives should not accelerate the decomposition of polymers in the light, as well as allow the possibility of prolonged use with it. That is, it is necessary to make the degradation process start at a certain moment. It is very difficult. The technological process involves the addition of 1-8% of additives (for example, the starch considered earlier is introduced) as part of a small typical processing method, when the heating of the raw material does not exceed 12 minutes. But it is necessary to ensure that they are evenly distributed throughout the polymer mass. All this allows you to keep the period of degradation in the range from nine months to five years.
Development prospects
Although the use of biodegradable polymers is gaining momentum, they now make up pathetic percentages of the total market. But, nevertheless, they are still quite widely used and are becoming increasingly popular. Already now they are pretty well established in the niche of food packaging. In addition, biodegradable polymers are widely used for disposable bottles, cups, plates, bowls and pallets. They also gained a foothold in the market in the form of bags for the collection and subsequent composting of food waste, bags for supermarkets, agricultural films and cosmetics. In this case, standard equipment for the production of biodegradable polymers can be used. Due to their advantages (resistance to degradation under ordinary conditions, low barrier to the transmission of water vapor and oxygen, the absence of problems with waste disposal, independence from petrochemical raw materials), they continue to conquer the market.
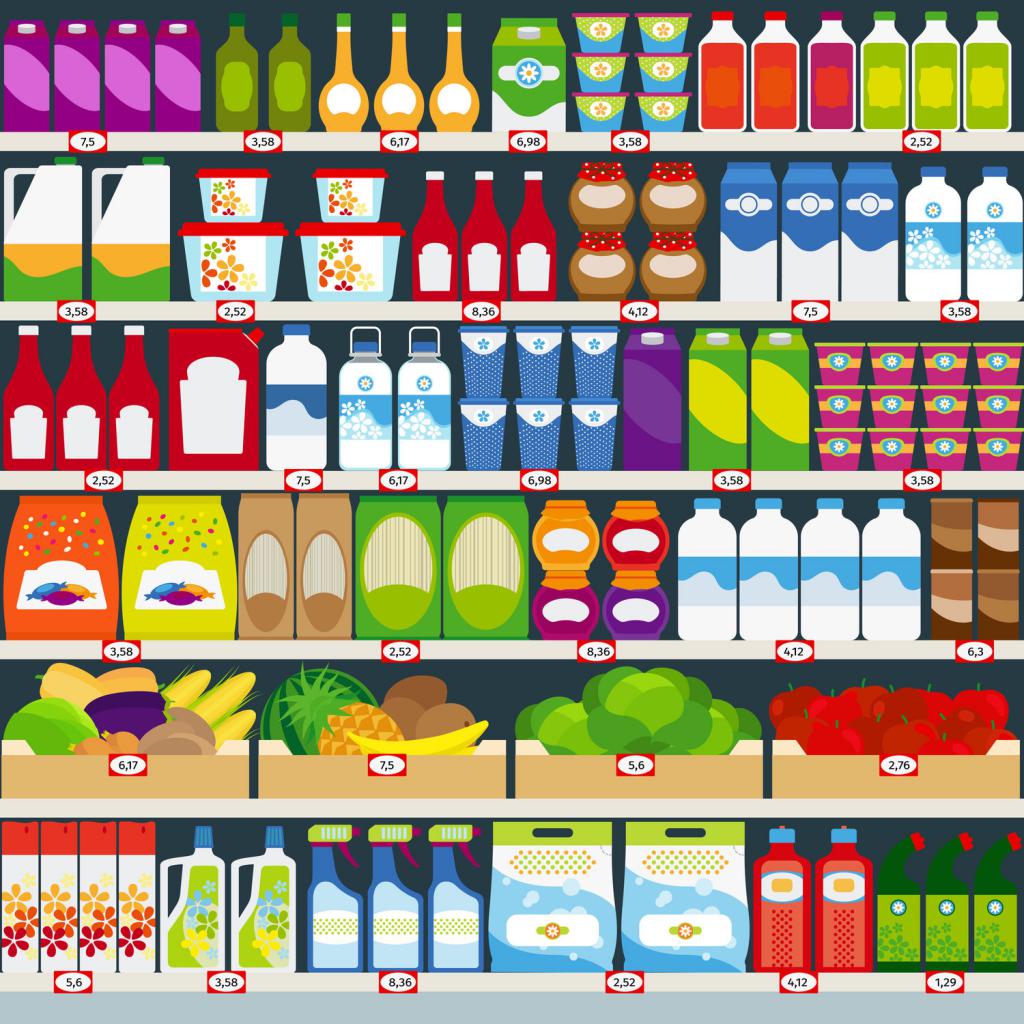
Of the main disadvantages, it is worth recalling the difficulties of large-capacity production and the relatively high cost. To a certain extent, this problem can be solved by large-scale production systems. Improving the technology allows you to get more durable and wear-resistant materials. In addition, it is necessary to note a persistent tendency to focus on products with the prefix "eco". This is facilitated by both the media and national and international support programs.
Gradually, measures to protect nature are tightened, which leads to the fact that some products from traditional plastic are prohibited in certain countries. For example, packages. They are banned in Bangladesh (after it was revealed that they clogged the drainage systems and caused large floods twice) and Italy. Gradually comes the realization of the real price that you have to pay for wrong decisions. And an understanding of the need to ensure the preservation of the environment will lead to more and more limitations of traditional plastic. Fortunately, there is a demand for the transition to even more expensive, but environmentally friendly materials. In addition, research centers in many countries and large private companies are looking for new and cheaper technologies, which is good news.
Conclusion
So we examined what biodegradable polymers are, methods of preparation, and the field of application of these materials. Continuous improvement and improvement of technology is observed. So let's hope that in the coming years the cost of biodegradable polymers will really be equal to the materials obtained by traditional methods. After that, the transition to safer and more environmentally friendly developments will only be a matter of time.