Beet harvesters - agricultural machines for harvesting sugar and fodder beets for its subsequent processing in production. This equipment is equipped with high-precision attachments and functional processing systems. Due to the presence of built-in units, the beet harvester is able to independently process the harvested crops and send the prepared raw materials to enterprises for further processing. These are machines with a pneumatic-wheel supporting frame and sophisticated attachments that allow collecting, cleaning and primary processing of beets.
Types of Beet Harvesting Machines
Beet harvesting can be carried out according to two different schemes, depending on the type of beet harvester:
- Top-lifting type. In this process, the roots are extracted from the soil with tops of grass by the top-lifting method. Then the tops are trimmed already in the car. In modern agriculture, this type of beet harvesting machines is gradually being abandoned.
- Beet harvesters with a preliminary cut of tops. The operation scheme of such machines is as follows: first, with knives, it is cut to the top of the tops, and the root crops themselves are extracted with special digging. According to this scheme of beet harvesting , most modern machines work.
Beet harvesters can be self-propelled or trailed type. The latter option, cheaper and less productive, does not have complex systems, it is mainly used in small areas of sowing. In modern agriculture, self-propelled machinery is increasingly preferred. These machines are more productive, do not require the involvement of large personnel, additional equipment and are capable of performing a whole range of work.
Specifications
Modern beet harvesters, trailed or self-propelled, have different technical characteristics depending on the model and modification, which are adapted to certain conditions. When choosing a model, characteristics are selected in accordance with the volume of the crop, the nature of the soil, and the harvesting conditions. High-performance diesel engines with a capacity of at least 7 liters and more than 250 liters are installed on an agricultural combine. with. The power of the installed power unit depends on the operating conditions, from ordinary to complex, in addition, it must provide optimal traction characteristics. To work in difficult conditions using large trailed mechanisms, special versions of combines with an increased wheel chassis and engines with a capacity of more than 500 liters are used. with. On modern models, automatic systems for controlling the engine speed are installed depending on the load on the working bodies. The average weight of beet harvesters varies within 12,000 kg. Attachment specifications may vary by type and ability to upgrade. The amount of fuel consumed individually depends on the manufacturer and model. The transmission and gearbox is selected taking into account the operating conditions and load standards.
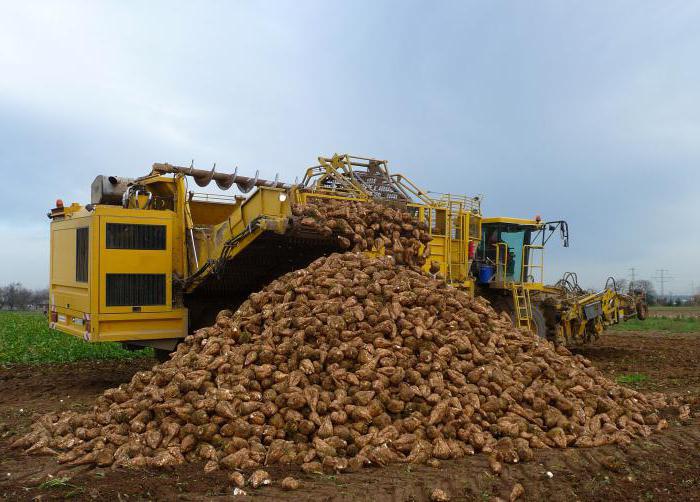
Design features of beet harvesting machinery
According to the classification, the beet harvesting machine belongs to the heavy all-wheel drive equipment on the pneumatic stroke and a hydraulic gearbox. Each unit is equipped with a conveyor belt, a receiving hopper, a processing unit with special knives for trimming surpluses. Depending on the size, lifting ladders can be equipped on the combine frame to facilitate operation and ease of maintenance. Industrial beet harvesters are made on the basis of a powerful supporting frame to which drive axles are attached. The operator’s cab is located on a high platform in front of the machine, which significantly increases visibility during operation. A constructive feature of special equipment is the fastening of the front working body with a system of knives, grabs and rollers directly to the frame with rigid fixation.
Additional devices
Harvesting beets with a combine can be done with the installation of various types of mounted and trailed devices. This equipment is complementary to the main worker and is aimed at increasing the overall productivity of beet harvesting equipment at a particular work site and reducing harvest time. As additional devices, additional receiving hoppers or bunkers of increased volume, trailers for transporting beets are used. The installation of reinforced wide knives allows you to cover a large area in one pass. In the winter season, additional starting devices are used.
Management Features
Multifunctional beet harvesters are equipped with modern adaptive control systems that greatly facilitate the work of the operator-driver. Monitoring devices allow you to track any changes in the operation of the equipment, the state of the main components and, if necessary, change the operating mode or conduct timely maintenance. To control the equipment, enough skills and training on other machines of this class. In the management of modern beet-harvesting machines, a number of key features can be distinguished: simplicity and informativeness of control, high engine life, ease of maintenance, multifunctionality, a large selection of additional equipment.
Leading manufacturers
A large number of various agricultural machinery is presented on the world market, including for harvesting beets. Beet harvesters of different brands and manufacturers have individual features and are adapted for various working conditions and for a specific consumer. Among the most popular manufacturers can be identified: Ropa, Kleine, Holmer, Caterpillar, Agrifac, Beetliner. Universal combines with mounting mechanisms for additional attachments are in greatest demand. This multifunctional technique makes it possible to save money for the agricultural producer and reduce the cost of production.
Features of the Ropa technique
German manufacturers of agricultural machinery Ropa annually present new design solutions. Beet harvester "Ropa" is economical in terms of fuel consumption with the active collection of root crops. The functionality of these machines even has a special economical mode of operation. Reducing fuel consumption, in turn, allows the farmer to reduce the cost of production. For work on large sown areas and difficult conditions, the Ropa combine can be equipped with additional units of impressive dimensions. To increase the efficiency of harvesting, agricultural machines of this German manufacturer are equipped with uproots with the possibility of operation in rows of different widths and the function of controlled cutting of tops. In addition, a special trolley has been developed for Ropa combines for transporting wide-mounted attachments on highways. This device is easily controlled on corners and descents. The trolley is equipped with a brake system.
Features of the Kleine technique
The German Klein beet harvester stands out for its advanced technical features. The entire line of beet-harvesting equipment of this manufacturer is characterized by a large capacity of the receiving hopper, multifunctional attachments. Thanks to the successful placement of wheeled bridges, Kleine combines are distinguished by a short base, which significantly increased the machine's cross-country ability in the field. Most models of this brand are equipped with wider front tires. The driver's cab is located in the center of the supporting frame, which provides better visibility and a sense of overall dimensions.
Combine maintenance and breakdowns
Almost all beet harvesting machines have design weaknesses that can cause malfunctions. The content of harvesters mainly depends on its type and model. Modern imported samples, due to the presence of complex electronic, pneumatic and hydraulic systems, are quite demanding in maintenance and maintenance. For such a technique, a maintenance schedule is mandatory. Domestic cars are less whimsical. Their minor repair and replacement of consumables is successfully carried out in garages. One of the common mistakes in the maintenance and repair of both domestic and foreign equipment is the use of non-original consumables and spare parts. All technical work should be carried out in specialized garages using high-precision equipment by qualified specialists.