The organization of a quality control service is a hot topic for almost any more or less large enterprise. The future of the workshop, enterprise, industry, and even the whole country largely depends on its effectiveness and quality of performance of duties. Is it too much? Unfortunately no.
Introductory information
Quality control bodies and services are more focused on logistical aspects. So, if we talk about enterprises, then this aspect is given priority attention. But there is still state supervision, industry supervision, quality control of services and much more. In addition, often the results of the services are questionable (often justified). The greatest accuracy can be obtained using instrumentation, tooling, test equipment. All this allows a qualified and comprehensive assessment of the subject of interest. If we talk about maintenance, then this is somewhat more complicated. Indeed, the demanding and objectivity of the controllers plays a big role here. A very common situation is when one or two parameters are at a very low level. Sometimes it is even possible to observe a situation when due to losses from claims they lose more than from marriage in the production process. That is, it is necessary to put the whole process in mind. This will save resources, reduce costs and increase competitiveness. If consumers of services or goods find defects, then this indicates that the quality of work of the controlling sector is unsatisfactory. When working, it is necessary to focus not only on technical and technological aspects, but also on organizational, economic and informational ones. This approach will remove many of the issues of quality control service.
What problems do you have to deal with?
Even the best plan is worth little if there is no solid basis for its implementation. And to get it, you need to deal with such points:
- Low bandwidth control services.
- Lack of staff.
- Failure to perform certain works aimed at quality control.
- The appearance of unregulated sites.
- Unreliability of control results.
- Imperfection of measurement methods, which is manifested in parallelism and duplication in the assessment of quality.
- Subjectivity and low demands.
- Lack of technical equipment and gaps in metrological support.
- Low wages, giving rise to neglect of duties.
- Inconsistency of the qualifications of employees with the complexity of the activities carried out (low educational level).
- Deficiencies in bonus systems, which does not contribute to the interest in the full and timely identification of a marriage.
As you can see, a large role in the process is played by an employee of the quality control service, his level of education and training, as well as the tools and techniques available and used by him. Given that losses, as a rule, exceed the cost of a decent payment for his work, it is better not to skimp on a penny. It is especially necessary to pay attention to the head of the quality control service. After all, do not forget the old adage that the fish rots from the head.
What is the process itself?
It is difficult to give a definite answer to this question. For ease of understanding, let's look at how the quality control service in an enterprise works. The goal pursued by her is the elimination of shortcomings, which impede a positive impact on the processes in the organization. For this, reliable and objective checks are used:
- Technical control that prevents the imbalance of production processes, as well as deviations from established requirements (especially applies to product quality). Properly built, it will contribute to the prevention of marriage, as well as its detection in the early stages. And this, in turn, allows you to quickly and cost-effectively fix problems. The end result is an increase in the quality of the products being created and an increase in production efficiency.
- Objective and strict control over the performance by employees of their duties. This allows you to prevent the marriage from entering the market, reduces the volume of unsatisfactory products for sale, reduces the likelihood of unproductive costs that need to be spent on the identification, elimination, storage, shipping and transportation of defective goods.
- If the quality control service at the enterprise shows reliable results, then the prerequisites are created for eliminating duplication and parallelism functions. That positively affects the workload of other organizational structures in the form of the release of qualified specialists, lowering the volume of processed information, reduces the number of disagreements. Additionally - control costs are reduced and the effectiveness of its implementation is increased.
What results can be obtained by improving supervisory structures?
First of all, it is necessary to mention the following tasks:
- Development and subsequent implementation of measures for the prevention and prevention of marriage. Minimizing the number of deviations from the approved processes and preventing failures in them allows to improve the results of operations.
- The development and implementation of advanced monitoring tools and methods allows increasing the productivity of inspectors, increasing the volume of inspections, as well as facilitating the work of responsible personnel.
- The preparation of the data and their subsequent processing for the actual state of affairs and changes in the basic conditions allows obtaining reliable data.
- Objective accounting, coupled with a comprehensive differentiated assessment of the quality of labor, can improve the reliability of the results.
- Implementation of work on the implementation of self-control among employees. A person who does not need to be forced to do something (especially correctly) provides higher performance than the one that requires a boss over his head.
- Coordination of the work of different departments.
- Planning and implementation of a feasibility study of various aspects of activity.
- Periodic search for the absolute value, as well as the dynamics of costs for the implementation of quality control.
- Observation of new developments and issuance of assessments of their seamlessness.
- Monitoring compliance with technological discipline.
All these tasks can be considered simultaneously as functions of the quality control service.
What about small enterprises?
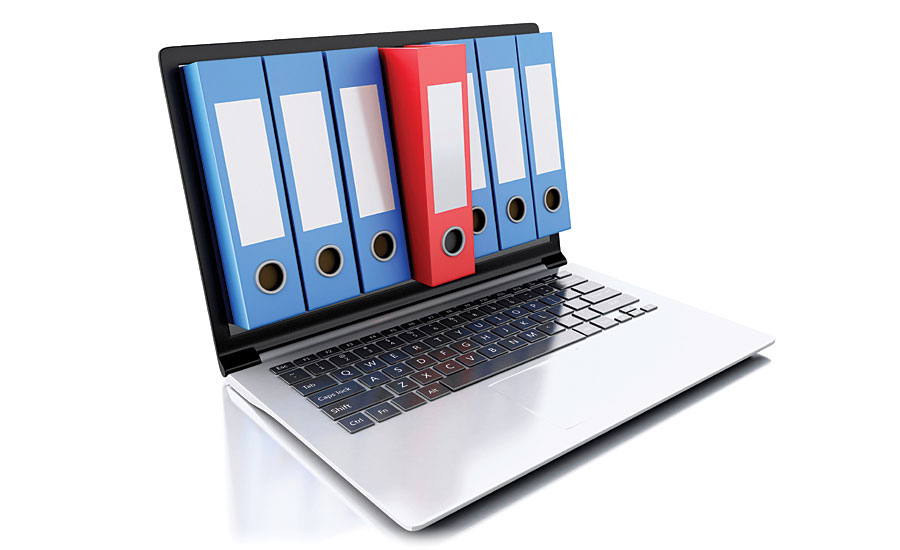
If the commercial structure provides jobs for several thousand people, then the creation of a supervisory authority is not a particularly big problem, funds will be found. But speaking of small enterprises? Due to a number of objective reasons for them, the creation of new units is not always possible. As a way out of this situation, a scheme is used when the above functions are transferred to individual specialists, which are part of the structural units of the enterprise system. It should be noted that this is not as difficult as it might seem at first glance. After all, very often it turns out that it is possible to quickly and effectively increase control only by changing the wrong system of evaluation and incentives. It is necessary to think over the creation of a scheme within which workers themselves will be interested in improving the quality of their work. But we should not forget about the concentration of efforts on ensuring priority elimination of the most pressing existing problems. And first of all, it is always necessary to keep marriage prevention in mind. The organization of the quality control service should be based on the interconnection of various elements, creating a synergistic effect from each person involved. In short, it is desirable to divide the whole process into two stages:
- Obtaining information about the current state of a particular object, its indicators and features.
- Comparison of primary data with pre-established criteria, norms, requirements. In this case, a search is made for the discrepancy between the actual information and the expected one.
It should be noted that in some cases the two stages do not have a clear boundary. An example of such a situation is the size control using a caliber, when actual and acceptable values are compared.
About the prevention system
The best problem is one that is not allowed. Each employee of the quality control service should work on this. To do this, pay attention to:
- At the stage of product development, services, solutions.
- The standards for the control of technological, design and other documentation (affecting raw materials, materials, semi-finished products, components and so on).
- Supervision of labor discipline by the direct executors.
- Self-control of workers, brigades, workshops and other units.
How to achieve this? Alas, a universal recipe does not exist. As general measures, we can advise you to work on the creation of a system for the timely detection of emerging deviations and eliminate the reasons for reducing the quality of the result, as well as preventing similar development scenarios in the future. It is desirable that the resulting system is a combination of interconnected subjects and objects of control, as well as covering all stages of the control process. An effective prevention system allows you to have a timely and targeted impact on the quality of products created, prevents possible failures and shortcomings, allows them to quickly identify and eliminate with minimal resources. Moreover, opportunities, as a rule, can be found at all stages: development, production, circulation, consumption and restoration. In market conditions, it is necessary to concentrate on conducting objective and reliable work, preventing the transfer of low-quality labor results to consumers. In this case, GOST 16504-81 can be used as a legislative and regulatory basis. It discusses how tests should be conducted and product quality control carried out. Of course, it does not consider all possible options, but as a basis it will fit perfectly.
What to do with production?
If we talk about the public sector, then everything is relatively simple. The enterprises have the corresponding services; externally, it is controlled by the prosecutor's office and branch departments. The state quality control service is responsible for making high-quality products. Although it can go to the private sector. For example, as a special case - the construction control service. The quality of the buildings being created is invaluable, so it was decided that supervision of it should remain in the hands of the state. Although, to be honest, private enterprises operating in the market should themselves be interested in showing the best results. Otherwise, they will not survive in the competition between different structures. To think that it is possible to reach a certain level, and then relax and rest is extremely dangerous. It is necessary to constantly improve and work on the quality of the result. And the quality control service should provide all possible assistance in this.
What to do with the service sector?
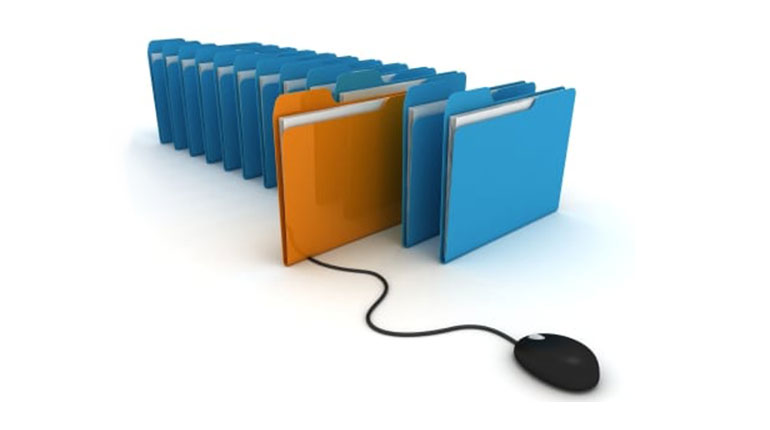
In the modern world there has been a clear trend in the economy. Its essence is the transfer of emphasis from the sphere of production to services. One can argue a lot about the appropriateness of real benefits, more promising areas (for example, concentration on scientific research and implementation of their results). Nevertheless, there is a fact - the service sector is in bloom and developing. Therefore, issues of supervision of employees and their level of work become relevant. Here the service of quality control services comes to the rescue. What is its feature? First of all, it is necessary to note the fact that a service, unlike a material good, is very difficult to evaluate with exact characteristics. So, for example, the metal has a carbonate number, thickness, compliance with the established scheme. But for pizza delivery services such approaches are not applicable. Here it is necessary to take into account completely different points, such as the speed of acceptance of the order, its processing and arrival. For a hairdresser, these criteria are also not suitable. That is, there is a lack of unified and universal indicators of assessment. Therefore, when a service quality control service is created, it is necessary to take into account not only generalizing recommendations, but also the specific needs and challenges that the organization faces.
Example
It is good to consider theoretical positions alone. But it will be useful to pay attention to a practical example of how the process of the control service looks in reality. Introductory information: object - processes of creation, application, transportation, storage, maintenance and repair of material goods (products). In addition, do not forget about the accompanying documentation. More specifically, the control object can be divided into three groups:
- Items of labor. Products of auxiliary and main production (products, materials and so on).
- Means of labor. For example, equipment and tools.
- Technological processes.
What does it look like in practice? To consider the example better, we should turn to the steps already mentioned above:
- At the development stage, the compliance of the prototype / created technical documentation with the existing assignment and design rules is checked.
- At the manufacturing stage, attention is paid to quality, comprehensiveness, packaging, labeling, quantity of products, as well as the course of production processes.
- The operation stage is to verify compliance with the requirements for supporting documentation (for use, repair).
When creating any material good, an integral part of the process is technical control. Its execution time depends on the standards used, specifications, facility, materials, regulatory documentation. Moreover, in order to minimize possible losses, it is always necessary to strive for new frontiers, not to stop there, but also to know the measure. For excessive expenses exceeding the cost of production are unlikely to allow them to stay afloat for a long time.
Conclusion
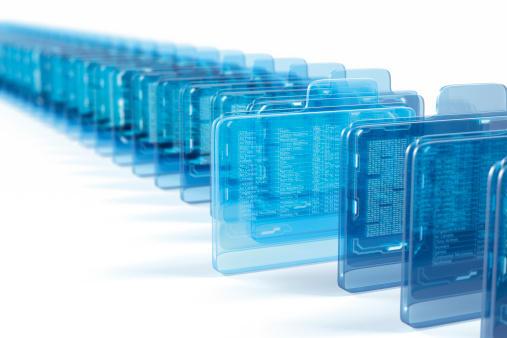
So the main subject of the article is considered. Of course, such a small volume is not enough for a full study of the topic. Take, for example, quality control of a security service or audit. On the one hand, this is a service. On the other hand, how to evaluate effectiveness? In the case of the security service, this may be the absence of incidents, losses, thefts. For auditors - timely identification of problem chains in the organization. But here's how to find out that responsible professionals are doing their job well? After all, until a crisis takes on an unprecedented scale, they may not even be aware of it. Alas, a similar situation is quite common. To avoid unpleasant surprises, the organization’s management must constantly keep abreast of events and not only rely on reports and final data, but also delve into everything that happens. If at least one fact appears that gets out of the optimal picture, it is necessary not to turn a blind eye to it, but to react, to understand the reasons for its existence. After all, it may turn out that a small manifestation will be a harbinger of a significant crisis. For example, if the number of defects created on a machine increases, then you should stop its work, understand the reasons and eliminate them so that new losses do not occur. And in order to respond as quickly as possible to these problems, it is necessary to create a situation in which the first employee who meets with the marriage will be interested in informing about them.