Although aluminum is a non-ferrous metal and, in comparison with ordinary steel, is relatively expensive, it is used by man quite widely. This durable and lightweight material can be used in everyday life, in construction, in production. The chemical formula of aluminum in the periodic table looks like this: Al.
Is corroded
Aluminum rusts, as you know, very slowly. At least, iron and steel cannot be compared with it in this regard. The corrosion resistance of aluminum is explained primarily with the fact that under normal conditions a thin oxide protective film forms on its surface. As a result, the chemical activity of aluminum is sharply reduced.
Factors Affecting Rust Resistance
Aluminum is resistant to corrosion, but in some cases it can still begin to deteriorate rather quickly due to oxidation. This usually happens when the film is damaged for some reason or its formation is impossible.
Most often, the external thin protection aluminum loses under the influence of acids or alkalis. Also, the cause of the destruction of the film can be ordinary mechanical damage.
Types of corrosion
After the destruction of the film, Al and its alloys begin to rust, that is, self-destruct, like many other metals. In this case, aluminum and corrosion can be exposed:
Chemical. In this case, rusting occurs in a gaseous medium without water. In this case, the surface of the aluminum product is destroyed evenly over the entire area.
Electrochemical. Corrosion of aluminum in this case occurs in a humid environment.
Gas. This type of corrosion occurs then aluminum is in direct contact with some chemically aggressive gas.
The equation of aluminum corrosion (oxygen oxidation) in air is as follows: 4AI + 3O 2 = 2AL 2 O 3 .
The chemical formula of the oxide protective film is AL 2 O 3 .
Alloys
The most corrosion resistant variety is technical aluminum. That is, almost pure 90% metal. Unfortunately, aluminum alloys are much more susceptible to rust. It is believed that the least corrosion resistance of this metal is reduced by impurities of magnesium, and most of all - by copper.
Mg-Al Alloys
Such materials are widely used in construction, food and chemical industries. They are also very often used in mechanical engineering. It is believed that such materials are well suited for the construction of structures exposed to sea water.
In the event that magnesium contains no more than 3% of the alloy, it will have almost the same anti-corrosion properties as technical aluminum. Magnesium in such an alloy is in solid solution and in the form of Al8Mg5 particles uniformly distributed throughout the matrix.
If this metal contains more than 3% of the alloy, Al8Mg5 particles begin to precipitate, to a large extent, not inside the grains, but along their boundaries. And this, in turn, has an extremely negative effect on the anticorrosive properties of the material. That is, the product becomes much less resistant to rust.
Alloys with magnesium and silicon
Such materials are most often used in engineering and construction. Mg2Si makes alloys of this variety very strong. Sometimes copper is also a component of such elements. It is also introduced into the alloy for hardening. However, copper is added to such materials in very small quantities. Otherwise, the anticorrosion properties of the aluminum alloy can be greatly reduced. Intercrystalline rusting in them begins when more than 0.5% copper is added.
Also, the tendency to corrosion in such materials can increase with an unjustified increase in the amount of silicon contained in their composition. This substance is usually added to aluminum alloys in such proportions that nothing is left after the formation of Mg2Si. Pure silicon contains only some materials of this variety.
Corrosion of aluminum and its alloys with zinc
Al, as already mentioned, rusts more slowly than its alloys. This also applies to materials from the Al-Zn group. Such alloys are very popular, for example, in aircraft construction. Some varieties may contain copper, others not. Moreover, the first type of alloys, of course, is more resistant to corrosion. In this regard, Al-Zn materials are comparable to magnesium-aluminum.
Alloys of this variety with the addition of copper show signs of some instability to rust. But at the same time they are destroyed due to corrosion, nevertheless they are slower than those made using magnesium and Cu.
The main ways to combat rust
Of course, it is possible to reduce the corrosion rate of aluminum and its alloys, including by artificial means. There are only a few ways to protect such materials from rust.
For example, it is possible to exclude the contact of this metal and its alloys with the environment by coloring the paintwork. Also, the electrochemical method is often used to protect aluminum from rust. In this case, the material is additionally coated with a layer of more active metal.
Another way to protect Al from rust is high voltage oxidation. Also, a powder coating technique can be used to prevent aluminum corrosion. Used for its protection, of course, and rust inhibitors.
How is oxidation produced?
Using this technique, aluminum and its alloys are often protected against corrosion. Oxidation is performed under a voltage of 250 V. Using this technique, a strong oxide film is formed on the surface of the metal or its alloy.
The impact on the material by current in this case is performed using water cooling. At low temperatures, due to stress, the film on the aluminum surface is very strong and dense. If the procedure is performed at high temperatures, it turns out quite loose. Aluminum treated in such an environment needs additional protection against contact with air (staining).
The product using this technology is first degreased in a solution of oxalic acid. Then aluminum or alloy is lowered into alkali. Further, the metal is exposed to current. At the final stage, if the oxidation was carried out at a sufficiently high temperature, the material is additionally stained with immersion in salt solutions, and then treated with steam.
Using LMB
This method, like oxidation, is used to protect aluminum from rusting quite often. Such material can be painted using a dry, wet technique or a powder method. In the first case, aluminum is first treated with a composition containing zinc and strontium. Further, the paint itself itself is applied to the metal.
When using the powder method, the work surface is pre-degreased by immersion in alkaline or acid solutions. Further, chromate, zirconium, phosphate or titanium compounds are applied to the product.
Use of insulators
Very often, other metals become stimulants of the onset of corrosion processes in aluminum and its alloys. This usually happens with direct contact of products or their parts. In order to prevent rusting of aluminum, special insulators are used in this case. Such gaskets can be made of rubber, paronite, bitumen. Also in this case, varnishes and paints can be used. Another way to protect aluminum from corrosion when in contact with other materials is to coat its surface with cadmium.
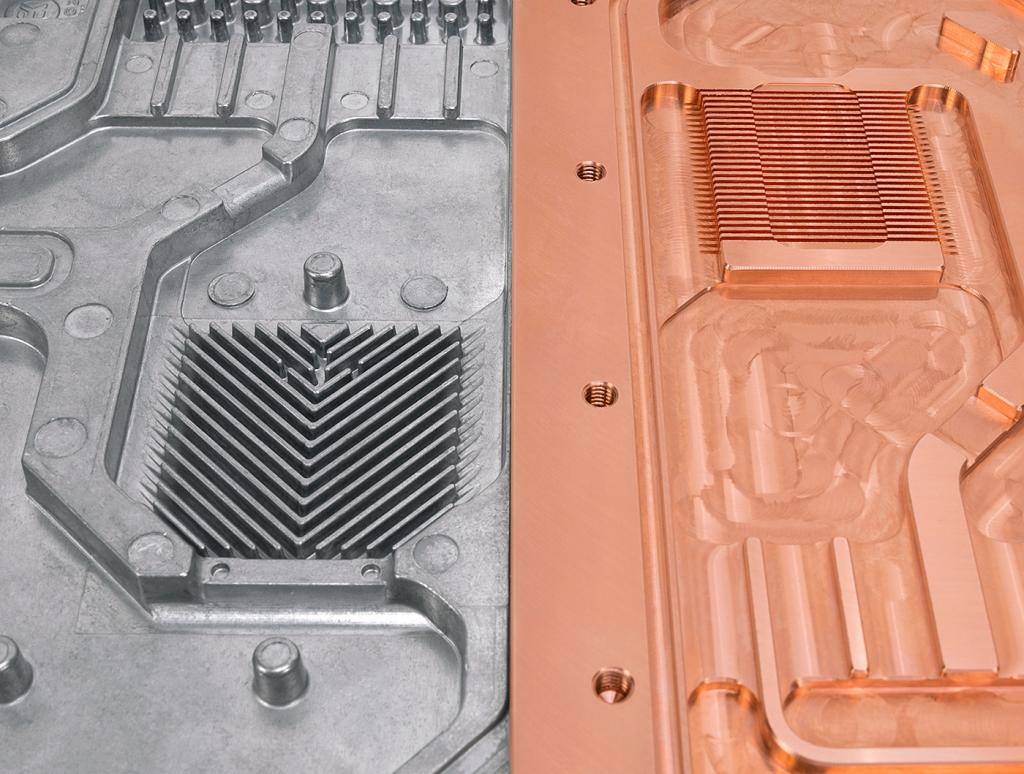
It is especially important to ensure the isolation of aluminum parts in various kinds of mechanisms and components from direct contact with copper. It is also believed that protecting from contact with other metals should not only the parts made of Al. In terms of corrosion resistance, iron and aluminum, like steel, for example, are much inferior. Therefore, such metals and some others often protect in a special way. The materials are simply coated with a protective aluminum layer. Of course, such products should be protected from contact with copper or other metals.