Modern civilization cannot imagine itself without the widespread use of steel. Iron, which only 400-500 years ago was valued almost worth its weight in gold, today tons can ineptly rust in landfills. Steel is smelted in millions of tons, being used absolutely everywhere. The main problem is often its processing, since many varieties of this material are quite solid, and modern technological standards are very stringent and do not allow torn and rough “cut lines”. To improve the quality of finished products, scientists invented water cutting of metal.
When did it begin to be put into practice?
Surprisingly, this technology was quite widely used back in the 60s of the last century. For the first time, it was used in fairly specific industries, such as aircraft and space industries. But soon, companies began to think that water cutting of metal is an excellent innovation that can provide the broadest opportunities for the entire industry with its wider introduction into production.
Since then, this metal processing method has become more and more popular. Can water cutting be used only for sheet metal, or is it subject to other metal structures? What are the advantages and disadvantages of this method? We will try to tell about all this in the framework of this article.
Areas of use
The main advantage of this cutting method is the fact that there is practically no significant mechanical impact on the surface of the material. There is completely no friction, the mechanisms do not heat up. This has a very positive effect on the quality of the cut and the entire finished part.
Processed materials
First, I want to note right away that the scope of the method is not limited to metals and their alloys alone. It is also used for materials such as:
- Granite, natural stone, other minerals.
- Ceramics and glass.
- All metals, including even titanium and its alloys.
- Reinforced concrete and concrete.
- All types of plastic and other synthetic materials.
What is even better, while it is possible to achieve an extremely low consumption of both the raw materials and components. Moreover, when working with hazardous materials, it is precisely cutting metal with water that is the only acceptable method, since there are no sparks, no harmful dust, there is completely no possibility of spontaneous ignition of the resulting production waste.
How does it work in practice?
As we said, metal rolling is not the only area of application of the method, but still 70% of the work is done in this area. The technology itself is based on the supply of water with a finely dispersed abrasive material under pressure on the surface of the material. So what exactly happens during cutting? Here are the main processes:
- Water under tremendous pressure is supplied to a particularly robust tank.
- At the same time, the abrasive is usually “tucked in”, usually represented by the smallest fraction of sand.
- After that, the resulting mixture is fed into the nozzle.
- The stream is directed to the desired area and begins to cut the material.
The quality and speed of cutting with this approach increase many times. From time to time, you only need to add an abrasive. This process is fully automated, usually no intervention by attendants is required.
It is worth considering that waterjet cutting allows you to achieve a speed that is usually achievable only with plasma processing of materials. But! The cut quality is such that it can be repeated only using a laser. The cost of these types of work, and the complexity of the equipment used for this, is difficult to compare, since these are completely different “weight categories”.
What equipment is used for this?
Even in the days of Ancient Egypt, people noticed that water is able to radically change the properties of those materials that have been exposed to it for a fairly long time. Even hard stones were rolled into a state of smooth nakedness, and visible depressions appeared relatively quickly on the surface of granite and marble.
Subsequently, the same principle was adopted by modern industry. Of course, from ancient times the order of using the capabilities of "hydrogen oxide" has changed significantly: firstly, it is necessary to provide an acceptable pressure of water, and secondly, the thickness and direction of its jet. This is achieved as follows:
- A special pump of very high pressure not only accumulates a certain supply of liquid, but also delivers it to the material being processed. It is the power of this mechanism that determines the thickness and density of steel, which can be cut. Water is supplied to the pump itself from a conventional water supply system, and (to prevent interruptions) it is desirable to carry it out from several sources at once.
- A special power regulator is responsible for the thickness of the jet. The cutting speed and thickness of the processed material depend not only on its settings, but also on the characteristics of the abrasive material used. In order to “carve out” something more viscous, one has to use a three-phase filler, for simple steel only water and a filler are enough, in the role of which, as we have already repeatedly pointed out, the most ordinary sand can be used. Of course, what can be regulated not only the composition of the mixture ... What other parameters are characterized by metal cutting with water? Pressure and fluid velocity. Keep in mind that the minimum acceptable water velocity must reach 1200 m / s at a pressure of about 4.7 t / cm!
Other equipment
Nozzles are very important. Their diameter, as well as the materials used directly depend on both the abrasive and the speed of the jet. The water pressure during metal processing is so high that only high-strength alloys can be used for this. Nozzles need to be changed, the frequency of this depends on many factors. One of the most important components of any water cutting machine is a mixer. The homogeneity of the resulting mixture depends on it, as well as the quality of the slices, the presence or absence of chips on the edges of the machined parts.
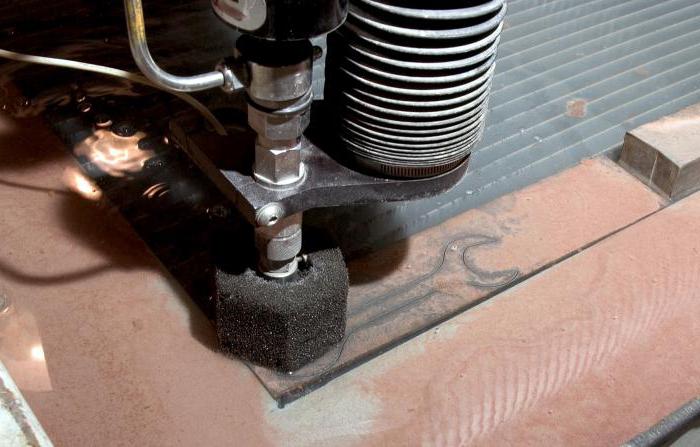
Note that waterjet cutting is impossible without the use of high-precision automation. A feature of this metal processing method is the taper of the edge, due to the properties of water under such specific conditions of its use. The higher the speed, the higher this indicator. But! With an increase in the taper, the final quality of the material processing is directly proportionally reduced. To reduce such a negative effect, the patented Flow Dynamic Waterjet technology and similar product quality management methods can be used.
What is the principle of work of smart technologies? Everything is relatively simple: the automation itself determines the type, viscosity and density of the processed material, and then independently changes the angle of inclination and the diameter of the nozzle. Only after that does the constantly corrected cutting of metal with sand and water begin.
Preparatory operations
Finally, a system of preliminary preparation of liquid for subsequent use of the latter in a metal cutting system is no less important. To maximize the life of the equipment, as well as to ensure maximum processing quality, literally crystal clear water is vital. This is achieved by filtering through "high-precision" filters, through which all relatively large impurities with a high molecular weight are removed from the liquid.
It is important to understand that different manufacturers offer different waterjet equipment, the possibility of equipping which with additional functions directly depends on the cost of the machines. So, advanced functionality will allow you to perform even complex curly cutting, if necessary, not to mention simpler operations.
Water Cutting Functionality
In many areas of art, metal cutting with water, the price of which is significantly lower than laser processing (from 15 rubles per meter) has also found wide application. The fact is that one of the advantages of this method is the complete absence of chips, as well as surface heating, which makes the resulting image or profile exactly what the designer or artist wanted them to be. Here are the key features this material processing method offers:
- Custom metal cutting. The important thing is that with any inclination of the nozzle, the cut is very high quality. The accuracy is such that the finished parts after their manufacture can be used with little or no preparation.
- Modern machines can work with minimal human intervention, or not require the presence of maintenance personnel. Using the same equipment, it is possible to cut out parts of the most complex configuration, and to do this as soon as possible, but with the highest possible quality.
- Metal processing is especially common. So, a machine for cutting metal with water can cut up to 20 centimeters of medium carbon steel. For titanium, the indicators are more modest - within 15-17 mm. Particularly strong alloys - about 12 mm. The minimum ratio is copper and is only 4-5 mm.
- Decorative elements and decorations using this method are obtained not only very high quality, but also cheap. In addition, the configuration of the finished products does not depend on the experience of the employee and not on the “hardness of the hand”, but solely on the settings. If the deviation during cutting cannot exceed 0.5%, use the machine for cutting metal with CNC water.
In recent years, pipes have been cut so often. For this, special machines are used, with which the pipe cut is initially polished and very smooth. Thus, waterjet cutting, the services of which are offered in any large city, is becoming an increasingly common and popular method of processing a wide variety of materials.
CNC Waterjet Machines
Especially expanding the scope of application of this method helped CNC machines that allow you to process a variety of materials, flexibly adjusting the quality of work, the maximum and minimum cutting thickness, as well as other parameters.
Deviations from the given parameters are minimal, which is almost impossible to achieve with standard cutting methods. The principle of operation of this class of equipment is reduced to the following actions:
- First, the appropriate software is installed, which may be different for each type of material. The program will automatically select the composition of the mixture, the type of abrasive and the required volume of water, pressure and other parameters. For curly cutting materials meet special programs.
- As a rule, additional processing of the finished part is no longer required. If the cutting parameters were chosen incorrectly or inaccurately, some roughness of the finished product may be observed. But! If you use a CNC machine that can independently select cutting parameters, this practically does not happen. In this case, the equipment automatically selects the necessary mode, focusing on the thickness, viscosity and density of the metal.
- In addition to cutting, such machines allow you to drill holes of various diameters and configurations. At the same time, we repeat the words already described above: if something special is required from the equipment, it is necessary to choose those models that have corresponding additional functions.
- Sometimes these machines can be used not only for cutting, but also for polishing finished products and parts that were made on other equipment.
Manual cutting
In some cases, machines can be controlled by a qualified operator. In this mode, all settings have to be set in manual mode, which is not always particularly convenient. But they have manual methods of cutting metal and many advantages, which include the following:
- The cost of such work costs about one and a half times cheaper.
- Strange education of the operator at the same time, oddly enough, does not matter much. The fact is that manual control of such machines is quite simple, and does not have a large number of complex functions. This equipment is used in cases where it is necessary to cut parts having a simple geometric shape.
- The functionality of the machines at the same time remains at the same level. A smooth cut, hole drilling and other simple operations - all this can be done with manual control. In addition, there is the possibility of processing not only metal, but also other materials.
We hope that you understand how metal cutting occurs with water. This method is extremely common in modern industry, with its help it is possible to produce parts of almost any shape and configuration.