The technological process is the basis of any production operation. It includes a set of procedures carried out in a certain sequence, the action of which is aimed at changing the shape, size and properties of the manufactured product. The main examples of technological processes are mechanical, thermal, compression processing. As well as assembly, equipment, pressure treatment and much more. In the conditions of factory production, the department of the chief technologist is responsible for carrying out such processes and processing technological documentation. Specialists of the department control the correctness of the operational moments. Correctly developed and competently organized technological processes in mechanical engineering and production at any other level make it possible to carry out the necessary procedures for the manufacture of appropriate products with minimal cost. Both material and power and temporary.
Mechanical engineering as a type of production
Mechanical engineering as an industry variety of production is characterized by the use of universal equipment, due to which the processing of parts of various sizes and sizes, universal devices and measuring instruments is carried out. This industry provides not only the automated operation of devices, but also the use of physical human labor - after all, a significant amount of machine-building processes is carried out precisely due to manual work and the efforts of highly qualified working personnel. In such plants, often the cost of various parts is much higher, although productivity is much lower. The representative offices of such engineering include turbine, shipbuilding, chemical plants, as well as enterprises of heavy engineering. Moreover, today, among modern engineering plants that work for mass or mass production, there are experimental research workshops where work is underway to create new machine models in a single copy - and this is the prerogative of individual machine production.
However, it is nevertheless worth emphasizing that domestic engineering is aimed at mass production of machines. At the same time, the technological process of designing and manufacturing parts is focused on the production of a large number of identical products for a long period of time. At the same time, it is aimed at the narrow specialization of workplaces, semi-automatic machines, automatic machines, modular units. And special equipment, the availability of universal tools and the wide interchangeability of parts make it possible to coordinate the technological process with automated control systems.
Elements of machine production. Nuances
As in any technological process, mechanical engineering provides for the mandatory subdivision of work procedures into specific areas of activity with the achievement of a specific result reproduction at a given site. It is important to distinguish and separate from each other fundamentally different operational moments.
What elements of the process are presented in the standard process of machine building? Consider them:
- A technological operation is an integral part of the overall process, during which processing of workpieces performed by one tool (file, cutter) at one workplace (for example, a machine tool) is performed. At the same time, work can be performed by one or several employees at once. Based on the amount of work assigned to be performed, the technological operation can be simple or complex. The latter, in turn, can be dispersed into constituent parts, which are called installations in production.
- Technological installation is an integral part of the operation performed at the workplace in a state of constant attachment of the workpiece.
- Position - an integral part of the operation, which is carried out under conditions of a constant position of the workpiece relative to the toolbox (not taking into account those movements that are caused by the working movements of the workpiece itself or the tool itself).
- Transition - an integral part of the operation, which is accompanied by constant operation of the machine or tool.
- The passage is part of the transition, which causes the removal of layers of metal (or other material, if it is not metal).
- The working technique is the completed action of an employee of the factory engineering workshop, which is accompanied by the fastening or removal of the cutting tool, the workpiece itself and beyond.
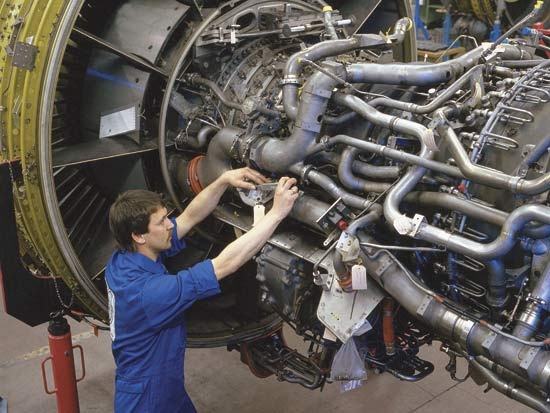
The structure of technological processes. Essence
The structure of mechanical engineering itself is represented by the passage of the finished product through several different processing phases. Often these phases are represented by the procurement phase, the processing phase and the assembly phase. But what exactly is each of the phases in the structure of mechanical engineering?
Blank stage
The procurement phase is characterized by the implementation of procedures for obtaining blanks using the following methods:
- Casting - involves filling a container, mold or cavity with material in a liquid state of aggregation.
- Stamping is a procedure of plastic deformation of materials with adjustment of their shape and size.
- Pressing - testing of objects for strength (density, tightness) of a hydraulic or pneumatic nature in the process of pressure.
- Disembarkation is an operation of a blacksmithing nature, which consists in deforming a workpiece with a partial draft in order to create a thickening of the object by reducing its length.
- Metal cutting and bending is the process of deformation or division of a metal pipe, sheet or casting into its component parts.
- Cutting of rolled or sheet material - punching, cutting, cutting and trimming of metal material, performed in order to separate complex metal structures into separate segments.
At the end of the procurement phase procedures, a transition to the second stage in the structure of mechanical engineering is carried out.
Processing stage
The processing phase involves the processes of turning various production blanks into finished parts. What processing methods determine the engineering process in the second phase of production? Consider them:
- Metalworking - a set of mechanical processes for changing the shape, size and quality of alloys and metals.
- Heat treatment is the process of heat exposure of a metal in order to give it the necessary properties (in particular, the appropriate size and shape).
- Chemical processing is the process of chemical attack on a metal through the targeted destruction of alloys by etching in solutions of alkalis and acids.
- Chemical-thermal treatment is the combined effect on the workpiece of a thermal and acid-base process, during which the surface of steel parts is saturated with carbon.
- Plasma treatment is a material processing procedure performed using low-temperature plasma generated by high-frequency or arc plasmatrons in order to change the properties of this material.
- Galvanization is the technology of coating one metal with another using an electrolytic compound.
- Paintwork - grinding, polishing and coating the material with paints or varnishes in order to give it an aesthetically complete appearance.
- Welding is the process of fixing parts in order to reliably connect them in one single design.
- Passivation - treatment of the area after welding with a special substance, which is applied evenly on the surface of the material.
At the end of the deformation of materials, cutting and bending of the metal, and also after processing the products with one of the methods specially designed to obtain a specific result, a transition to the third phase of the technological process is carried out.
Assembly stage
The last stage of the technological process of mechanical engineering provides for the implementation of collective measures and dressing of metal billets. Docking of various metal profiles can be carried out in several ways:
- Complete assembly of individual assembly units into a single whole final product.
- Adjustment and overhead assembly.
- Test connection of components in a single metal structure.
Problems of mechanical engineering in Russia
The main task remains the need for a radical reconstruction. The problem of the lag of domestic production from the world level of the economy is directly related to the low profitability of such branches of machine production as instrument making, machine tool manufacturing, computer manufacturing, electronic and electrical industries. This issue requires a speedy solution.
Depending on the nature and orientation, the fundamental problems of mechanical engineering in domestic production can be grouped into separate blocks. It:
- Deficiencies in the development of the machine-building complex - the problem is caused by the low growth rates of leading industries, a significant decline in production, disruption of technological connections, downtime of individual enterprises, and low rates of equipment renewal in relation to the level of products.
- Lack of resources for structural adjustment - insufficiently developed branching of the directions of activity of domestic engineering requires re-profiling, but there are not enough funds for this. Moreover, the industry requires a reduction in imbalances in the growth rates of individual reproduction segments: somewhere, it is necessary to optimize the structure of operational technologies, and somewhere to supplement the production process with the missing capacities.
- The disadvantages in the quality of the products are the mismatch of the manufactured machines (their overwhelming majority) with world-class machines, as well as the low reliability of the produced vehicles, which leads to the failure of their finished models a year after active use. The percentage of such production facilities is 20-30% in the total specific gravity of the produced models.
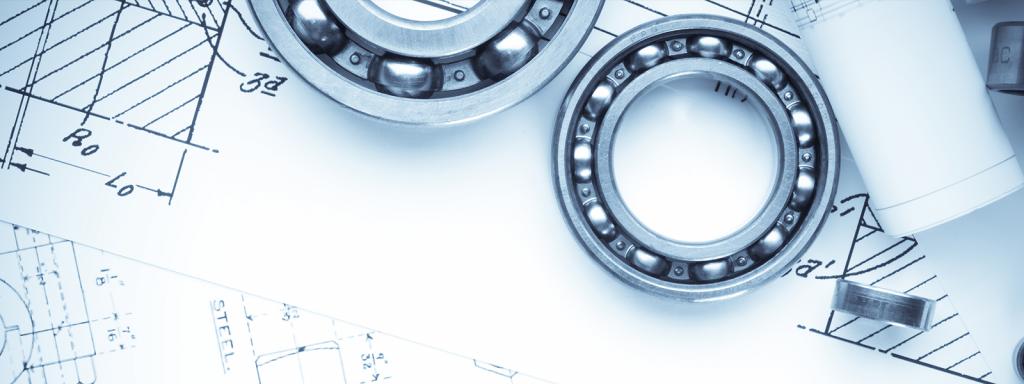
Process Automation
Automated control systems in the field of engineering are the primary source of increasing production capacity in the entire engineering segment. What does it mean?
Automation of production today plays the role of the main direction in which production moves around the world. Everything that was previously carried out due to the person’s ability to work, his physical strength and intellectual abilities, all this at the present time is reduced to technology, which independently operates technological cycles and monitors their implementation. At the same time, the role of man is minimized - he only has to observe the correctness of the implementation by automated systems of all those actions that are aimed at optimizing domestic production. Everything is simple.
Automation of technological processes in mechanical engineering is carried out due to the totality of operations involving the start, stop, maintenance or change of the process of operational work at the facility as a whole. It really plays an important role in the development of the industry as a whole. The importance of individual machines, apparatuses, aggregates, devices, machine complexes, is a significant impact on the formulation of a fundamentally new work process at the engineering plant as a whole. After all, managed objects in automation are quite diverse and incredibly effective in their intended purpose.
The replacement of human labor can be carried out in terms of partial or absolute replacement. The process of mechanical engineering is carried out either completely due to the latest automation devices, or with partial replacement of human labor. Not all plants have the ability to replace human labor completely with automated. Someone for this lacks capacity, someone has equipment, and someone has the skills to work with such an unusual, but at the same time, unusually effective method of controlling the technological process.
Objects to be Automated
But not only human hands today can be replaced by mechanized devices with high-precision equipment, which is able to respond to the slightest remarks by the manager of the car. In addition to the fact that there is a direct replacement of a person at the machine with a specialized installation, in parallel automation of the following aspects is possible in the process of mechanical engineering:
- The production process - all the work that a person does every day with a reflex repetition of actions worked out to an automaton can be completely uninterruptedly replaced by a machine.
- Design - as mentioned above, not only the results of a person’s physical labor can be reviewed and adapted to their production needs. Intelligent work is also subject to automation. Moreover, some calculations and compilation of algorithms subject to electronic computing technology are the basis for correct computer-aided design.
- Organization - some aspects of the distribution functions for the specific implementation of the actions of the automated structure are only subject to external control. Everything else the technique does itself.
- Planning - calculations and identification of upcoming tasks in the future to fulfill are also assigned to “smart electronics”.
- Management - in order to manage the process of working with automated devices that assemble the machines, it is enough to carry out simple button manipulations, standing behind the control panel.
- Scientific research - all the mathematical aspects and features of miscalculations in the productivity growth of a machine-building plant in dynamics are also subject to automated computing systems.
- Business processes - if you wish, you can calculate the coefficient of your profit and marginal income from the engineering business, because computer technology can do everything for a person.
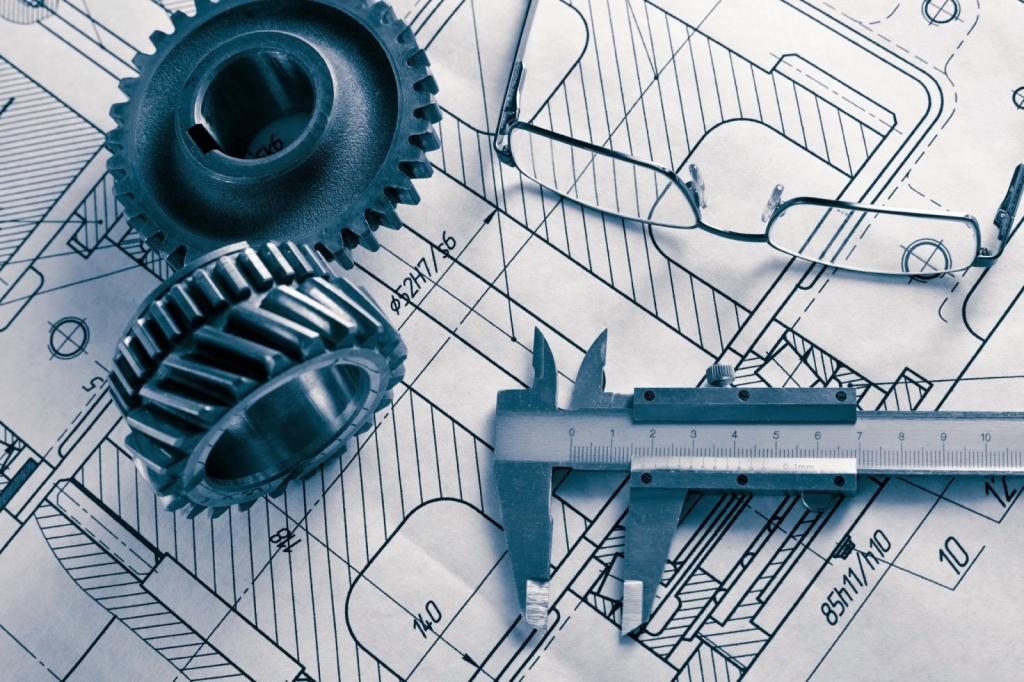
Advantages
The goal of automation of technological processes is to increase labor productivity along with an overall improvement in product quality and the introduction of high-tech equipment. With its help, it becomes possible to optimize the management of machine-building production, to move a person from hazardous industrial zones. And also increase reliability and double the profitability of precision engineering. Since automation increases convertibility and reduces the time it takes to process data during planning.
- What are the positive aspects of the automation of working moments in the machine-building complex? Consider them:
- Firstly, it is possible to save employees working in particularly difficult physical conditions from monotonous and heavy physical labor. For a person, a machine can do everything.
- Secondly, it is possible to save employees from staying at a workplace in professionally dangerous conditions (under a hinged car frame, behind a metal-cutting mechanical machine, and others).
- Thirdly, the prerogative is emerging of setting up an automated system for tasks that, based on the physical capabilities of a person, would not be within his power. We are talking about blocks of heavy weight, speed indicators of the task, endurance and the like criteria.
- Fourth, the main feature of workflow automation is that it has a positive effect on the growth of economic indicators of both the enterprise and the industry as a whole.
disadvantages
However, there are also negative aspects to replacing human labor with automated. Transport engineering, machine tool manufacturing or any other branch industrial enterprise encounters the following negative nuances in the process of labor automation:
- job cuts;
- technical limitations;
- existing security threats;
- unpredictability of the level of implementation and development costs;
- high initial pricing policy.
Technological documentation
Any work based on the procurement, processing and assembly of parts in mechanical engineering must be accompanied by the preparation and execution of the relevant papers. The form of cards and their composition in the general set of documents depends on the type of technological process (group, standard, single), type of production and degree of use of automated control systems at the enterprise. Based on these criteria and taking into account the degree of necessary data granularity, the presentation and content of operations in documents, as well as their completeness, can vary significantly.
Basically, a routing map, an operating room, a sketch map, a tool list, a sheet of technological documents and a bill of materials are often included in a set of documents of a technological process.